Technologie laser pour la production de cellules de batteries à haut rendement énergétique et à performance améliorée
Économiser de l'énergie lors de la production tout en permettant de créer des cellules de batterie ayant une densité de puissance plus élevée et une durée de vie plus longue.
Des cellules de batterie performantes sont une condition préalable essentielle à l'électrification du secteur de la mobilité. Dans cette optique, les chercheurs de l'Institut Fraunhofer de technologie laser ILT d'Aix-la-Chapelle ont mis au point des technologies innovantes basées sur le laser pour produire des batteries lithium-ion qui, par rapport à celles produites de manière conventionnelle, peuvent être chargées plus rapidement et ont une durée de vie plus longue. En outre, le séchage au laser dans le processus d'enrobage des électrodes à base d'eau est nettement plus efficace. Fraunhofer ILT présentera un démonstrateur pour présenter ses technologies laser d'avenir pour la production de cellules de batteries lors de la Hannover Messe 2023.
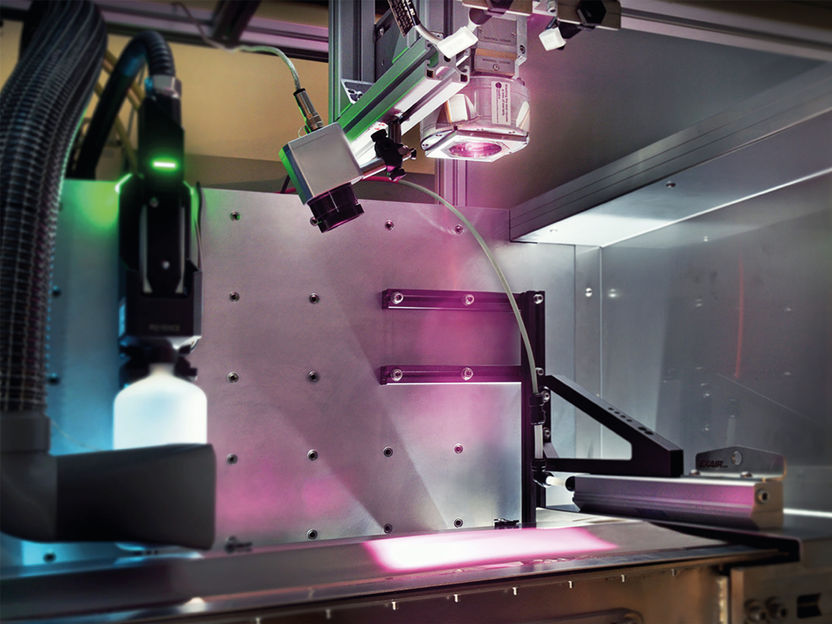
Séchage avec des lasers à diode : Grâce à une optique spéciale, le laser rayonne sur une plus grande surface de la feuille de cuivre recouverte de pâte de graphite. L'interaction entre les particules de graphite et l'énergie lumineuse génère de la chaleur et le liquide s'évapore.
© Fraunhofer ILT
Qu'elles soient utilisées dans des systèmes de stockage d'énergie stationnaires ou dans des voitures, bus, vélos et scooters électriques, les batteries joueront un rôle central dans la mobilité du futur. C'est pourquoi les chercheurs du monde entier travaillent à l'amélioration de la technologie des batteries. Les scientifiques du Fraunhofer ILT d'Aix-la-Chapelle ont récemment mis au point deux technologies de fabrication basées sur le laser qui permettent d'économiser de l'énergie lors de la production tout en rendant possible la création de cellules de batterie ayant une densité de puissance plus élevée et une durée de vie plus longue.
L'une des étapes clés de la production de batteries lithium-ion est la fabrication d'électrodes à base de graphite. Pour ces électrodes, une feuille de cuivre est recouverte d'une pâte de graphite par un procédé de rouleau à rouleau, puis séchée dans un four continu à une température de 160 à 180 degrés Celsius. En plus de consommer une grande quantité d'énergie, les fours continus alimentés au gaz, dans lesquels les feuilles de cuivre sont transportées sur un tapis roulant, occupent beaucoup d'espace : Ils mesurent entre 60 et 100 mètres de long et sèchent jusqu'à 100 mètres de feuilles par minute lorsqu'ils fonctionnent à l'échelle industrielle.
Séchage efficace grâce aux lasers à diodes
Les chercheurs du Fraunhofer ILT ont maintenant mis au point un système dans lequel un laser à diode effectue le processus de séchage. Le laser d'une longueur d'onde de 1 micromètre est associé à un système optique spécial qui éclaire l'électrode sur une grande surface. L'optique a été spécialement conçue pour le système de séchage par Laserline, partenaire industriel de Fraunhofer. Samuel Fink, chef de groupe pour le traitement des couches minces au Fraunhofer ILT, explique le principe de ce procédé : "Contrairement au processus de séchage à l'air chaud, notre laser à diode projette un faisceau de haute intensité sur la feuille de cuivre, qui est recouverte d'une pâte de graphite. Le graphite, d'une couleur noire, absorbe l'énergie. L'interaction qui en résulte provoque l'échauffement des particules de graphite et l'évaporation du liquide". La technologie Fraunhofer présente un certain nombre d'avantages : Comparé aux fours continus gourmands en énergie, le laser à diode est très économe en énergie et le système émet très peu de chaleur dans l'environnement. En outre, le système de séchage par laser prend beaucoup moins de place que les fours conventionnels. "Le séchage par laser à diode réduira l'énergie nécessaire de 50 % et l'espace requis pour un système de séchage à l'échelle industrielle d'au moins 60 %", prévoit M. Fink.
Une structure d'électrode 3D modifiée pour de meilleures performances
Outre ces avantages, l'équipe du Fraunhofer ILT a pu améliorer la densité de puissance et la durée de vie des batteries lithium-ion. Une fois de plus, la technologie laser est à l'honneur : dans ce cas, un laser à impulsions ultracourtes (USP) de haute puissance avec une énergie d'impulsion de 1 millijoule introduit une structure de trous, appelée "canaux", dans l'électrode de la batterie. Ces canaux servent d'autoroutes Li-ion pour les ions - ils réduisent considérablement la distance que les ions doivent parcourir et raccourcissent le processus de charge. En même temps, ils empêchent l'apparition de défauts, ce qui augmente le nombre de cycles de charge potentiels et prolonge en fin de compte la durée de vie de la batterie.
Le processus laser de production des structures à trous et l'effet positif qu'elles ont sur la cellule de la batterie sont bien connus, en théorie. Ce que les chercheurs du Fraunhofer ont fait, c'est transférer les principes du laboratoire à un processus évolutif, prêt pour l'industrie, qui utilise un rayonnement laser à impulsions ultracourtes de l'ordre de la femtoseconde pour modifier les électrodes. "Le court temps d'interaction des impulsions laser est suffisant pour ablater le matériau, mais il empêche également les trous de fondre, ce qui signifie que la batterie ne perd pas d'énergie", explique Matthias Trenn, chef d'équipe pour la structuration des surfaces à l'ILT Fraunhofer.
L'un des défis consistait à déterminer comment utiliser ce procédé sur de plus grandes surfaces afin d'obtenir le rendement élevé requis pour la production industrielle. L'équipe Fraunhofer a résolu ce problème en utilisant un dispositif à faisceaux multiples pour le contrôle des processus parallèles. Quatre scanners, chacun doté de six faisceaux, traitent la bande en parallèle. Ils couvrent une largeur de 250 millimètres et traitent la couche de graphite en continu. L'optique à faisceaux multiples a été développée et mise en œuvre en étroite collaboration avec Pulsar Photonics GmbH, une spin-off de l'ILT Fraunhofer fondée en 2013.
Les recherches menées par le Fraunhofer ILT démontrent que la technologie laser peut être utilisée comme processus de production numérique pour améliorer la qualité des cellules de batteries et accroître considérablement la durabilité pendant la fabrication. "La prochaine étape consiste à faire passer la technologie du prototype à une ligne de production industrielle", explique Matthias Trenn.
Les personnes visitant le stand Fraunhofer (Hall 16, stand A12) à la Hannover Messe 2023 (du 17 au 21 avril) pourront assister à une démonstration illustrant la conception du système.
Note: Cet article a été traduit à l'aide d'un système informatique sans intervention humaine. LUMITOS propose ces traductions automatiques pour présenter un plus large éventail d'actualités. Comme cet article a été traduit avec traduction automatique, il est possible qu'il contienne des erreurs de vocabulaire, de syntaxe ou de grammaire. L'article original dans Anglais peut être trouvé ici.