Nuovi approcci alla produzione di batterie
Dalla lavorazione delle materie prime al riciclaggio
La produzione di batterie è al centro della politica industriale e climatica a livello mondiale. Infatti, la domanda di sistemi di accumulo di energia per la mobilità elettrica e le applicazioni stazionarie è in crescita a livello globale, così come l'importanza di una produzione di batterie efficiente, sostenibile e indipendente a livello regionale.
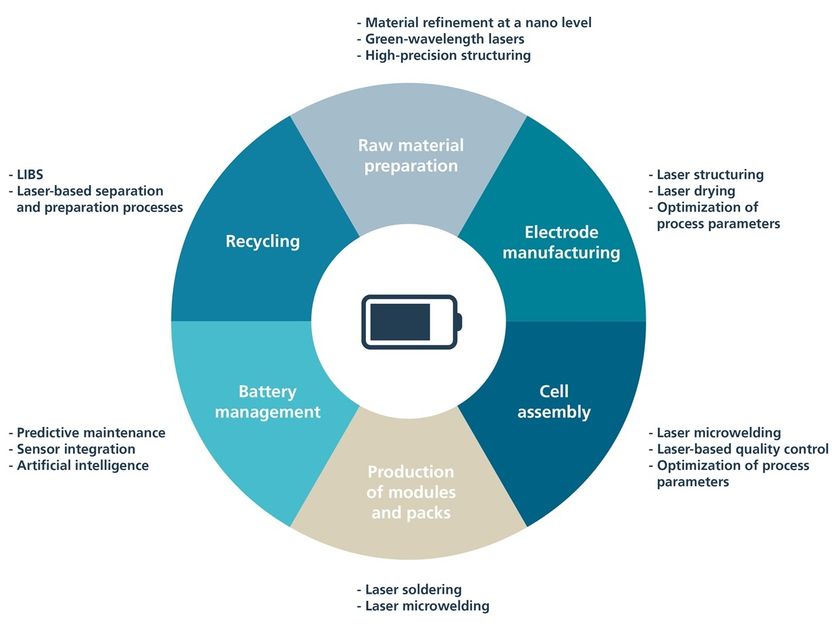
Utilizzo del laser e dell'intelligenza artificiale per la produzione di batterie sostenibili: produzione economica e affidabile.
© Fraunhofer ILT, Aachen
In particolare, l'ambiente commerciale e normativo per la produzione di batterie pone le aziende di fronte a sfide immense: Ad esempio, la dipendenza da materie prime come il litio, il cobalto e il nichel è causa di tensioni geopolitiche. Allo stesso tempo, le catene di approvvigionamento stanno diventando sempre più fragili a causa delle crisi globali e dell'aumento dei costi di trasporto. L'Europa si trova quindi ad affrontare il compito di costruire una catena del valore resiliente che comprenda sia l'estrazione delle materie prime, sia l'ulteriore lavorazione, sia il riciclaggio - dopo tutto, le batterie usate sono la risorsa tedesca di litio più abbondante. Inoltre, i processi di produzione devono essere adattati in modo flessibile ai nuovi design delle batterie, come quelle allo stato solido o agli ioni di sodio, al fine di garantire gli investimenti in esse.
Alla luce di queste sfide, è chiaro che il futuro della produzione di batterie in Europa può essere garantito solo utilizzando tecnologie all'avanguardia. La tecnologia laser, in particolare, offre soluzioni per soddisfare i requisiti chiave: efficienza, precisione e sostenibilità. Una produzione di batterie competitiva e sostenibile in Europa è difficilmente concepibile senza processi laser innovativi, sia nella lavorazione dei materiali che nella produzione di elettrodi o nel riciclaggio.
Lavorazione delle materie prime e raffinazione dei materiali: la base per una produzione sostenibile di batterie
Materiali come il litio e il nichel sono ancora componenti delle attuali celle per batterie. Le loro proprietà chimiche e fisiche rendono possibili alte densità di energia e lunghe durate, ma la loro estrazione e lavorazione pongono problemi complessi.
Tuttavia, le tecnologie delle batterie si stanno sviluppando rapidamente e l'industria punta a ridurre al minimo l'uso di materie prime rare e costose. Nel 2021 il produttore cinese di batterie CATL ha presentato una batteria agli ioni di sodio che rinuncia completamente al litio e al cobalto. Nell'aprile del 2024, CATL ha lanciato una batteria al litio ferro fosfato (LFP) priva di cobalto, in grado di alimentare un'automobile per oltre 1.000 chilometri con una sola carica. In soli dieci minuti può caricare energia sufficiente per 600 chilometri, il che corrisponde a una velocità di ricarica di un chilometro al secondo.
Toyota prevede di utilizzare le batterie allo stato solido nei veicoli ibridi a partire dal 2025. Nissan ha messo in funzione in Giappone un prototipo di impianto di produzione di batterie allo stato solido laminate. Panasonic ha presentato una batteria allo stato solido per i droni. VW e Mercedes, Ford e BMW stanno per introdurre batterie allo stato solido o hanno avviato partnership strategiche.
Un punto di partenza fondamentale per le nuove tecnologie delle batterie è il perfezionamento dei materiali a livello nanometrico, dove le materie prime vengono lavorate e funzionalizzate in modo specifico per massimizzare le loro prestazioni nelle batterie. Questo è ciò che sta esaminando il Dipartimento di Tecnologia delle Superfici e Ablazione dell'Istituto Fraunhofer per la Tecnologia Laser. Con le moderne tecnologie laser è possibile intervenire con precisione sulla struttura del materiale e allo stesso tempo ridurre al minimo il consumo di risorse.
Un altro esempio del successo dell'uso delle tecnologie laser è rappresentato dalla collaborazione tra il Fraunhofer ILT, la cattedra di tecnologia laser LLT dell'Università RWTH di Aquisgrana, TRUMPF e il sincrotrone elettronico tedesco DESY. Utilizzando i raggi X di un acceleratore di particelle, gli ingegneri hanno potuto approfondire le conoscenze sui processi di saldatura laser. Hanno dimostrato che l'uso di laser con una lunghezza d'onda verde migliora l'utilizzo del materiale e riduce gli scarti. Le loro scoperte non solo offrono vantaggi tecnologici, ma contribuiscono anche a una produzione più sostenibile.
"Questi progetti dimostrano che la tecnologia laser innovativa può non solo superare le sfide della lavorazione delle materie prime, ma anche consentire una produzione di batterie sostenibile e competitiva in Europa", spiega il Dr. Alexander Olowinsky, responsabile del settore Giunzione e Taglio del Fraunhofer ILT.
Produzione di elettrodi: innovazioni per una produzione sostenibile
I fogli conduttori di corrente (rame o alluminio) devono essere rivestiti con i materiali elettrodici per l'anodo e il catodo e successivamente essiccati - fasi cruciali che influenzano sia la densità di energia che la durata del ciclo delle batterie. I processi di essiccazione convenzionali basati su forni a convezione, tuttavia, consumano una quantità considerevole di energia e richiedono una grande quantità di spazio, il che limita la sostenibilità e l'efficienza della produzione di batterie.
Il progetto IDEEL (Implementation of Laser Drying Processes for Economical & Ecological Lithium- Ion Battery Production), finanziato dal Ministero federale tedesco dell'Istruzione e della Ricerca, mostra come l'essiccazione laser risolva queste sfide: Nel progetto, anodi e catodi sono stati essiccati per la prima volta in un processo roll-to-roll utilizzando un laser a diodi ad alta potenza. Questo metodo riduce significativamente il consumo energetico, raddoppia la velocità di essiccazione e dimezza lo spazio necessario.
"L'essiccazione laser non solo consente un controllo più efficiente del processo, ma contribuisce anche a migliorare in modo significativo l'impronta di carbonio della produzione di batterie", spiega il dott. Samuel Moritz Fink, responsabile del gruppo Thin-Film Processing del Fraunhofer ILT. Insieme ai partner del progetto, Fink e il suo team hanno sviluppato un modulo di essiccazione laser con ottica adattata e monitoraggio del processo per garantire un'essiccazione uniforme. Questo approccio offre anche flessibilità: I forni a convezione esistenti possono essere adattati alla tecnologia laser, rendendo più facile l'implementazione del processo innovativo nelle linee di produzione esistenti.
In un altro progetto di ricerca, il Fraunhofer ILT sta utilizzando un'ottica multiraggio appositamente sviluppata. Questo gruppo ottico divide il fascio laser in diversi fasci parziali che lavorano simultaneamente un nastro largo 250 millimetri di un anodo di batteria agli ioni di litio. Questa strutturazione di alta precisione aumenta la densità energetica e migliora la capacità di ricarica rapida.
La produzione di elettrodi beneficia anche dell'integrazione dell'intelligenza artificiale nel processo di produzione. I ricercatori del Fraunhofer ILT stanno attualmente studiando come i sistemi supportati dall'intelligenza artificiale possano essere utilizzati per ottimizzare i parametri di processo. Tali sistemi potrebbero non solo aumentare ulteriormente la qualità e la produttività, ma anche gettare le basi per una produzione autonoma.
Assemblaggio delle celle: precisione ed efficienza grazie a tecnologie innovative
Oltre all'essiccazione degli elettrodi, anche la giunzione precisa dei materiali degli elettrodi svolge un ruolo centrale nelle prestazioni e nell'affidabilità delle batterie. La microsaldatura laser si è affermata come tecnologia chiave in questo ambito, poiché è in grado di unire materiali come il rame e l'alluminio, essenziali per gli elettrodi delle batterie, senza metterli a contatto e con un'elevata precisione. Grazie al basso carico termico, la chimica sensibile delle celle rimane intatta, mentre la conducibilità elettrica viene ottimizzata grazie alla riduzione della resistenza di contatto. La microsaldatura laser offre una combinazione di flessibilità ed efficienza che i processi di saldatura tradizionali non possono eguagliare.
I requisiti per la microsaldatura laser variano a seconda del formato della cella, poiché ogni tipo di cella presenta sfide specifiche per quanto riguarda il contatto. Le celle cilindriche richiedono una profondità di saldatura precisa per garantire la conduttività elettrica, da un lato, e per evitare danni dovuti al surriscaldamento, dall'altro. Il contatto con il polo negativo pone particolari problemi, poiché il calore eccessivo può danneggiare la sensibile guarnizione polimerica, con conseguenti perdite di elettrolito. Nel caso delle celle a sacchetto, caratterizzate da un design flessibile e da un'elevata densità energetica, è necessario evitare la saldatura attraverso il rivestimento del film sensibile.
Uno sviluppo promettente nell'assemblaggio delle celle è rappresentato dal progetto XProLas, che TRUMPF sta portando avanti in collaborazione con Fraunhofer ILT e altri partner. L'obiettivo è quello di sviluppare sorgenti di raggi X compatte e guidate dal laser che consentano di effettuare test di qualità in loco direttamente presso la sede del produttore, invece di utilizzare grandi acceleratori di particelle come avveniva in precedenza. Questa nuova tecnologia consente di analizzare le celle delle batterie in tempo reale, permettendo di monitorare con precisione sia i processi di carica e scarica che la qualità del materiale. Questo metodo apre nuove possibilità, soprattutto quando è necessario esaminare il materiale del catodo, che determina le prestazioni e la durata della batteria. "Utilizzando sorgenti di raggi X brillanti, possiamo rilevare impurità e difetti del materiale in una fase precoce e, quindi, accorciare significativamente i tempi di sviluppo", spiega l'Ing. Hans-Dieter Hoffmann, responsabile del Dipartimento Laser e Sistemi Ottici del Fraunhofer ILT.
Anche in questo caso, l'integrazione dell'intelligenza artificiale apre un ulteriore potenziale: I sistemi supportati dall'intelligenza artificiale possono monitorare e regolare i parametri di processo in tempo reale. In questo modo è possibile rilevare e correggere tempestivamente le deviazioni, creando le basi per una produzione autonoma. La visione di una produzione "first-time-right", in cui tutti i componenti sono assemblati senza errori nel primo ciclo, è quindi a portata di mano.
Produzione di moduli e pacchetti: efficienza e precisione grazie alle tecnologie laser
Le singole celle vengono poi collegate per formare moduli o pacchi. La precisione gioca un ruolo decisivo soprattutto a livello di moduli, poiché è necessario integrare diversi cordoni di saldatura senza aumentare il carico termico sulle celle sensibili. I processi laser come la microsaldatura consentono agli utenti di adattare i loro processi a questi requisiti in modo personalizzato.
Una delle innovazioni chiave del Fraunhofer ILT è lo sviluppo di processi che possono essere utilizzati per unire in modo sicuro e preciso alluminio e rame, due materiali con proprietà fisiche molto diverse. Utilizzando una guida laser all'avanguardia, gli ingegneri dell'istituto possono controllare la profondità della saldatura in modo da non danneggiare le cellule sensibili.
"Questa tecnologia è essenziale per la produzione di moduli e pacchetti che devono funzionare in modo affidabile in condizioni estreme, come correnti elevate e carichi termici", spiega Olowinsky. Un esempio è la saldatura laser di celle cilindriche di grandi dimensioni, che l'istituto di Aquisgrana ha continuato a sviluppare insieme a partner come EAS Batteries GmbH. In questo caso, l'attenzione è rivolta alla creazione di un'interconnessione stabile e duratura tra le celle, per garantire una lunga durata e bassi tassi di guasto.
Oltre alla saldatura laser, si è affermata la saldatura laser, in particolare per unire componenti sensibili al calore. Questo processo funziona a temperature più basse rispetto ai metodi di saldatura tradizionali e, quindi, protegge l'elettronica sensibile all'interno dei moduli, rendendo non solo i pacchi batteria più affidabili, ma anche la produzione più efficiente dal punto di vista energetico.
Gestione delle batterie e integrazione dei sensori: intelligenza per sistemi di batterie a prova di futuro
La gestione delle batterie è una delle sfide principali dei moderni sistemi di accumulo di energia. Da essa dipendono in larga misura la sicurezza, la longevità e le prestazioni delle batterie, e non da ultimo l'accettazione della mobilità elettrica. I progressi nell'integrazione dei sensori e l'uso dell'intelligenza artificiale offrono opportunità di trasformazione per soddisfare questi requisiti.
Tradizionalmente, le batterie vengono monitorate a livello macroscopico, ma questo offre solo una visione limitata dei complessi processi all'interno delle celle. È qui che l'integrazione della tecnologia dei sensori durante la produzione offre nuove possibilità. I ricercatori del Fraunhofer ILT stampano i sensori direttamente sui componenti, o addirittura integrano i dispositivi di misurazione intelligenti al loro interno. Questi sensori rendono possibile il monitoraggio in tempo reale, ad esempio misurando le temperature, le forze o persino i cambiamenti chimici all'interno delle batterie durante l'uso.
"Con i sensori prodotti in modo additivo, possiamo monitorare continuamente le condizioni dei moduli delle batterie e reagire tempestivamente a potenziali difetti", spiega Samuel Fink. Questi sensori hanno uno spessore di pochi micrometri, sono precisi e resistenti alle sollecitazioni meccaniche e termiche, caratteristiche che li rendono ideali per l'uso nella batteria e nei moduli della batteria. La loro capacità di fornire dati continui consente la manutenzione predittiva, che rileva potenziali difetti prima che si verifichino.
Tuttavia, la sola integrazione della tecnologia dei sensori non è sufficiente per implementare la manutenzione predittiva. I sensori possono rilevare i cambiamenti nella chimica delle celle, mentre gli algoritmi di intelligenza artificiale analizzano questi dati e fanno previsioni sulla durata delle celle. I ricercatori del dipartimento Data Science and Measurement Technology del Fraunhofer ILT stanno sviluppando tali algoritmi supportati dall'IA che analizzano grandi quantità di dati provenienti da sensori in tempo reale. Questi sistemi consentono anche di adattare dinamicamente i processi, ad esempio ottimizzando i profili di temperatura durante l'assemblaggio delle celle o regolando i parametri di saldatura laser.
Riciclaggio e riutilizzo: il percorso verso un'economia circolare nella tecnologia delle batterie
Parallelamente al boom della tecnologia delle batterie, cresce anche la necessità di strategie sostenibili per il recupero di preziose materie prime. Un'efficace economia circolare è essenziale per ridurre la dipendenza dalle materie prime primarie, minimizzando l'impatto ambientale della produzione di batterie.
Nell'ambito del progetto europeo ADIR, il Fraunhofer ILT collabora con otto partner di tre Paesi per sviluppare un concetto di riciclaggio sostenibile per i dispositivi elettronici. Il progetto ACROBAT mira a sviluppare un piano per il riciclaggio delle batterie al litio-ferro-fosfato prima della loro penetrazione sul mercato su larga scala. L'obiettivo del progetto è recuperare oltre il 90% dei materiali critici. Insieme a partner come Accurec Recycling, il Fraunhofer ILT sta lavorando su metodi di separazione e trattamento innovativi, sostenibili sia dal punto di vista ecologico che economico. Gli esperti di laser di Aquisgrana stanno sviluppando un metodo di caratterizzazione in linea per valutare con precisione la qualità del materiale attivo.
Con il proprio processo di spettroscopia di rottura indotta da laser (LIBS), l'istituto è in grado di identificare e separare con precisione le composizioni complesse dei materiali. I ricercatori intendono adattare questa tecnologia al riciclaggio delle batterie usate per migliorare ulteriormente il recupero di metalli come il cobalto e il tantalio. Anche in questo caso, l'intelligenza artificiale può essere integrata per analizzare le grandi quantità di dati provenienti dalle misurazioni laser e ottimizzare il processo in tempo reale. Il monitoraggio supportato dall'intelligenza artificiale consente di regolare dinamicamente i parametri di riciclaggio, riducendo gli scarti e aumentando la qualità delle materie prime riciclate.
Conclusioni e prospettive
La produzione di batterie è al centro della transizione verso l'elettromobilità e, pertanto, è al centro di innovazioni che combinano efficienza, sostenibilità ed eccellenza tecnologica. Le tecnologie e gli sviluppi presentati lungo la catena di produzione mostrano come i processi laser all'avanguardia possano aprire la strada a un'industria delle batterie sostenibile e competitiva: dalla preparazione delle materie prime alla produzione degli elettrodi, fino all'assemblaggio e al riciclaggio delle celle. Allo stesso tempo, i sistemi di analisi e controllo supportati dall'intelligenza artificiale creano una nuova dimensione di controllo dei processi che migliora la qualità e la sostenibilità della produzione e riduce ulteriormente i costi di produzione.
In futuro, i circuiti di controllo supportati dall'intelligenza artificiale potrebbero consentire una produzione autonoma in cui i processi si adattano alle condizioni mutevoli in tempo reale. Inoltre, le sorgenti di raggi X guidate dal laser e le tecnologie di caratterizzazione in linea aprono nuove possibilità per l'assicurazione della qualità e l'analisi dei materiali.
Nota: questo articolo è stato tradotto utilizzando un sistema informatico senza intervento umano. LUMITOS offre queste traduzioni automatiche per presentare una gamma più ampia di notizie attuali. Poiché questo articolo è stato tradotto con traduzione automatica, è possibile che contenga errori di vocabolario, sintassi o grammatica. L'articolo originale in Inglese può essere trovato qui.