Nouvelles approches dans la production de batteries
De la transformation des matières premières au recyclage
La production de batteries est au cœur de la politique industrielle et climatique mondiale. En effet, la demande de systèmes de stockage d'énergie pour l'électromobilité et les applications stationnaires augmente dans le monde entier, tout comme l'importance d'une production de batteries efficace, durable et indépendante sur le plan régional.
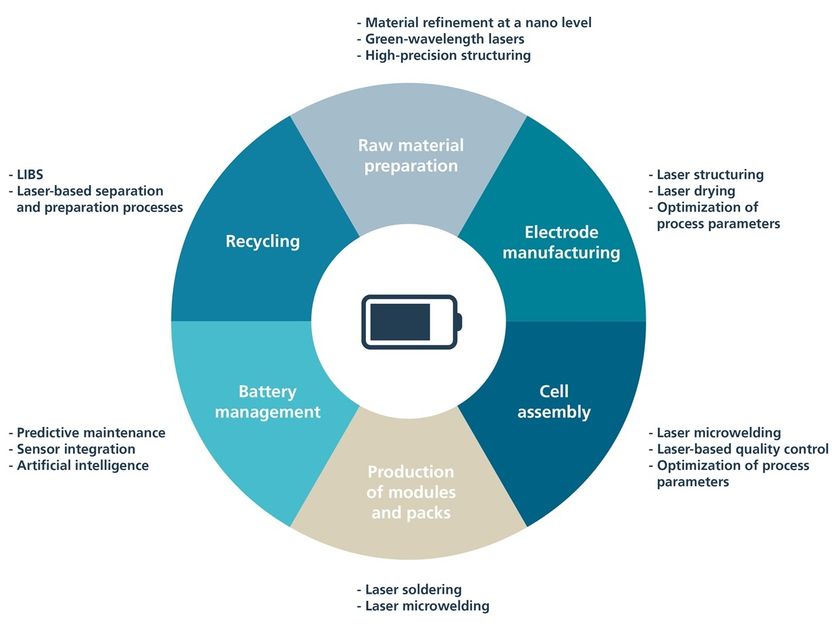
Utilisation des lasers et de l'intelligence artificielle pour la production durable de batteries : production rentable et fiable.
© Fraunhofer ILT, Aachen
En particulier, l'environnement commercial et réglementaire de la production de batteries pose d'immenses défis aux entreprises : Par exemple, la dépendance à l'égard de matières premières telles que le lithium, le cobalt et le nickel provoque des tensions géopolitiques. Parallèlement, les chaînes d'approvisionnement deviennent de plus en plus fragiles à mesure que les crises mondiales s'accumulent et que les coûts de transport augmentent. L'Europe est donc confrontée à la tâche de construire une chaîne de valeur résiliente qui inclut à la fois l'extraction des matières premières, le traitement ultérieur et le recyclage - après tout, les batteries usagées sont la ressource de lithium la plus abondante en Allemagne. En outre, les processus de production doivent être adaptés avec souplesse aux nouvelles conceptions de batteries, telles que les batteries à l'état solide ou les batteries sodium-ion, afin de garantir les investissements dans ces dernières.
Compte tenu de ces défis, il est clair que l'avenir de la production de batteries en Europe ne peut être assuré que par l'utilisation de technologies de pointe. La technologie laser en particulier offre des solutions pour répondre aux exigences clés - efficacité, précision et durabilité. Une production compétitive et durable de batteries en Europe est difficilement concevable sans processus laser innovants, que ce soit dans le traitement des matériaux, la production d'électrodes ou le recyclage.
Traitement des matières premières et affinage des matériaux : la base d'une production durable de batteries
Les matériaux tels que le lithium et le nickel sont encore des composants des piles actuelles. Leurs propriétés chimiques et physiques permettent d'obtenir des densités d'énergie élevées et de longues durées de vie, mais leur extraction et leur traitement posent des problèmes complexes.
Cependant, les technologies des batteries se développent rapidement et l'industrie cherche à minimiser l'utilisation de matières premières rares et coûteuses. Le fabricant chinois de batteries CATL a présenté en 2021 une batterie sodium-ion qui se passe totalement de lithium et de cobalt. En avril 2024, CATL a lancé une batterie au phosphate de fer-lithium (LFP) sans cobalt qui peut alimenter une automobile sur plus de 1 000 kilomètres avec une seule charge. En seulement dix minutes, elle peut charger suffisamment d'énergie pour parcourir 600 kilomètres, ce qui correspond à une vitesse de charge d'un kilomètre par seconde.
Toyota prévoit d'utiliser des batteries à semi-conducteurs dans les véhicules hybrides à partir de 2025. Nissan a mis en service un prototype d'usine de production de batteries à l'état solide laminées au Japon. Panasonic a présenté une batterie à l'état solide pour les drones. VW et Mercedes, Ford et BMW sont sur le point d'introduire des batteries à l'état solide ou ont conclu des partenariats stratégiques.
Un point de départ essentiel pour les nouvelles technologies de batteries est le raffinement des matériaux au niveau nanométrique ; ici, les matières premières sont spécifiquement traitées et fonctionnalisées pour maximiser leurs performances dans les batteries. C'est ce qu'étudie le département de technologie de surface et d'ablation de l'Institut Fraunhofer de technologie laser. Grâce aux technologies laser modernes, il est possible d'intervenir avec précision dans la structure des matériaux tout en minimisant la consommation de ressources.
La collaboration entre le Fraunhofer ILT, la chaire de technologie laser LLT de l'université RWTH d'Aix-la-Chapelle, TRUMPF et le synchrotron électronique allemand DESY est un autre exemple de l'utilisation réussie des technologies laser. En utilisant les rayons X d'un accélérateur de particules, les ingénieurs ont pu mieux comprendre les processus de soudage au laser. Ils ont montré que l'utilisation de lasers à longueur d'onde verte améliore l'utilisation des matériaux et réduit les déchets. Leurs découvertes offrent non seulement des avantages technologiques, mais contribuent également à une production plus durable.
"Ces projets montrent qu'une technologie laser innovante peut non seulement relever les défis du traitement des matières premières, mais aussi permettre une production durable et compétitive de batteries en Europe", explique le Dr Alexander Olowinsky, responsable de l'assemblage et de la découpe au Fraunhofer ILT.
Production d'électrodes : innovations pour une production durable
Les feuilles conductrices de courant (cuivre ou aluminium) doivent être enduites des matériaux d'électrode pour l'anode et la cathode, puis séchées - des étapes cruciales qui influencent à la fois la densité énergétique et la durée de vie des batteries. Les processus de séchage conventionnels basés sur des fours à convection consomment toutefois une quantité considérable d'énergie et nécessitent beaucoup d'espace, ce qui limite la durabilité et l'efficacité de la production de batteries.
Le projet IDEEL (Implementation of Laser Drying Processes for Economical & Ecological Lithium- Ion Battery Production), financé par le ministère fédéral allemand de l'éducation et de la recherche, montre comment le séchage au laser permet de relever ces défis : Dans le cadre de ce projet, les anodes et les cathodes ont été séchées pour la première fois dans un processus de rouleau à rouleau à l'aide d'un laser à diode à haute puissance. Cette méthode permet de réduire considérablement la consommation d'énergie, de doubler la vitesse de séchage et de diviser par deux l'espace nécessaire.
"Le séchage au laser permet non seulement un contrôle plus efficace du processus, mais contribue également à améliorer de manière significative l'empreinte carbone de la production de batteries", explique le Dr Samuel Moritz Fink, directeur du groupe de traitement des couches minces au Fraunhofer ILT. En collaboration avec les partenaires du projet, M. Fink et son équipe ont mis au point un module de séchage laser doté d'une optique adaptée et d'un système de surveillance du processus afin de garantir un séchage uniforme. Cette approche offre également une certaine flexibilité : Les fours à convection existants peuvent être équipés ultérieurement de la technologie laser, ce qui facilite la mise en œuvre du processus innovant dans les lignes de production existantes.
Dans le cadre d'un autre projet de recherche, le Fraunhofer ILT utilise des optiques à faisceaux multiples spécialement développées. Cet assemblage optique divise le faisceau laser en plusieurs faisceaux partiels qui traitent simultanément un ruban de 250 millimètres de large d'une anode de batterie lithium-ion. Cette structuration de haute précision augmente la densité énergétique et améliore la capacité de charge rapide.
La production d'électrodes bénéficie également de l'intégration de l'intelligence artificielle dans le processus de fabrication. Les chercheurs du Fraunhofer ILT étudient actuellement la manière dont les systèmes assistés par l'IA peuvent être utilisés pour optimiser les paramètres du processus. Ces systèmes peuvent non seulement améliorer la qualité et la productivité, mais aussi jeter les bases d'une production autonome.
Assemblage des cellules : précision et efficacité grâce à des technologies innovantes
Outre le séchage des électrodes, l'assemblage précis des matériaux des électrodes joue également un rôle central dans la performance et la fiabilité des batteries. La microsoudure laser s'est imposée comme une technologie clé dans ce domaine, car elle permet d'assembler des matériaux tels que le cuivre et l'aluminium, essentiels pour les électrodes des batteries, sans les mettre en contact et avec une grande précision. Grâce à la faible charge thermique, la chimie sensible des cellules reste intacte, tandis que la conductivité électrique est optimisée par la réduction de la résistance de contact. La microsoudure laser offre une combinaison de flexibilité et d'efficacité que les procédés de soudage traditionnels ne peuvent égaler.
Les exigences de la microsoudure laser varient en fonction du format de la cellule, car chaque type de cellule présente des défis spécifiques en matière de contact. Les cellules cylindriques nécessitent une profondeur de soudage précise pour garantir la conductivité électrique, d'une part, et pour éviter les dommages dus à la surchauffe, d'autre part. Le contact avec le pôle négatif pose des problèmes particuliers, car une chaleur excessive peut endommager le joint polymère sensible, ce qui pourrait entraîner une fuite d'électrolyte. Dans le cas des piles à poche, qui se caractérisent par leur souplesse et leur haute densité énergétique, il faut éviter de souder le film sensible qui les recouvre.
Le projet XProLas, mené par TRUMPF en collaboration avec Fraunhofer ILT et d'autres partenaires, constitue un développement prometteur en matière d'assemblage de cellules. L'objectif est de mettre au point des sources de rayons X compactes, pilotées par laser, qui permettent d'effectuer des tests de qualité sur place, directement dans les locaux du fabricant, au lieu d'utiliser de grands accélérateurs de particules comme c'était le cas jusqu'à présent. Cette nouvelle technologie permet d'analyser les cellules des batteries en temps réel, ce qui permet de contrôler avec précision les processus de charge et de décharge ainsi que la qualité des matériaux. Cette méthode ouvre de nouvelles perspectives, notamment lorsqu'il s'agit d'examiner le matériau de la cathode, qui détermine les performances et la durabilité de la batterie. "En utilisant des sources de rayons X brillantes, nous pouvons détecter les impuretés et les défauts des matériaux à un stade précoce et, par conséquent, réduire considérablement les délais de développement", explique Hans-Dieter Hoffmann, ingénieur diplômé et directeur du département des lasers et des systèmes optiques de l'Institut de technologie de Fraunhofer (ILT).
Ici aussi, l'intégration de l'intelligence artificielle offre un potentiel supplémentaire : Les systèmes assistés par l'IA peuvent surveiller et ajuster les paramètres du processus en temps réel. Les écarts peuvent ainsi être détectés et corrigés à un stade précoce, jetant ainsi les bases d'une production autonome. L'objectif d'une production "première fois correcte", dans laquelle tous les composants sont assemblés sans erreur dès le premier passage, est donc à portée de main.
Production de modules et d'emballages : efficacité et précision grâce aux technologies laser
Les cellules individuelles sont ensuite connectées pour former des modules ou des packs. La précision joue un rôle décisif au niveau du module en particulier, car plusieurs soudures doivent être intégrées sans augmenter la charge thermique des cellules sensibles. Les procédés laser tels que la microsoudure permettent aux utilisateurs d'adapter leurs procédés à ces exigences de manière personnalisée.
L'une des principales innovations du Fraunhofer ILT est la mise au point de procédés permettant d'assembler en toute sécurité et avec précision l'aluminium et le cuivre, deux matériaux aux propriétés physiques très différentes. Grâce à un guidage par faisceau laser de pointe, les ingénieurs de l'institut peuvent contrôler la profondeur de soudage afin de ne pas endommager les cellules sensibles.
"Cette technologie est essentielle pour la production de modules et de packs qui doivent fonctionner de manière fiable dans des conditions extrêmes, telles que des courants élevés et des charges thermiques", explique M. Olowinsky. Le soudage au laser de grandes cellules cylindriques, que l'institut d'Aix-la-Chapelle a continué à développer avec des partenaires tels que EAS Batteries GmbH, en est un exemple. Ils s'attachent à créer une interconnexion stable et durable entre les cellules afin de garantir une longue durée de vie et un faible taux de défaillance.
Outre le soudage au laser, le brasage au laser s'est imposé, en particulier pour l'assemblage de composants sensibles à la chaleur. Ce procédé fonctionne à des températures plus basses que les méthodes de soudage traditionnelles et protège ainsi les composants électroniques sensibles à l'intérieur des modules, ce qui rend non seulement les batteries plus fiables, mais aussi la production plus efficace sur le plan énergétique.
Gestion des batteries et intégration des capteurs : l'intelligence au service de systèmes de batteries à l'épreuve du temps
La gestion des batteries est l'un des principaux défis des systèmes modernes de stockage de l'énergie. La sécurité, la longévité et les performances des batteries en dépendent largement - et notamment l'acceptation de l'électromobilité. Les progrès réalisés dans l'intégration des capteurs et l'utilisation de l'intelligence artificielle offrent des possibilités de transformation pour répondre à ces exigences.
Traditionnellement, les batteries sont surveillées à un niveau macroscopique, mais cela n'offre qu'un aperçu limité des processus complexes qui se déroulent à l'intérieur des cellules. C'est là que l'intégration de la technologie des capteurs pendant la production offre de nouvelles possibilités. Les chercheurs du Fraunhofer ILT impriment des capteurs directement sur les composants, voire y intègrent des dispositifs de mesure intelligents. Ces capteurs permettent une surveillance en temps réel, comme la mesure des températures, des forces ou même des changements chimiques à l'intérieur des batteries lorsqu'elles sont en cours d'utilisation.
"Grâce aux capteurs fabriqués additivement, nous pouvons surveiller en permanence l'état des modules de batterie et réagir à des défauts potentiels à un stade précoce", explique Samuel Fink. Ces capteurs n'ont que quelques micromètres d'épaisseur, ils sont précis et résistants aux contraintes mécaniques et thermiques, ce qui les rend idéaux pour une utilisation dans la batterie et dans les modules de batterie. Leur capacité à fournir des données en continu permet une maintenance prédictive, qui détecte les défauts potentiels avant qu'ils ne se produisent.
Toutefois, l'intégration de la technologie des capteurs ne suffit pas à elle seule à mettre en œuvre la maintenance prédictive. Les capteurs peuvent détecter des changements dans la chimie des cellules, tandis que les algorithmes d'intelligence artificielle analysent ces données et font des prédictions sur la durée de vie des cellules. Les chercheurs du département Science des données et technologies de mesure de l'Institut Fraunhofer ILT développent des algorithmes assistés par l'IA qui analysent en temps réel de grandes quantités de données provenant de capteurs. Ces systèmes permettent également d'adapter dynamiquement les processus, par exemple en optimisant les profils de température pendant l'assemblage des cellules ou en ajustant les paramètres de soudage au laser.
Recyclage et réutilisation : la voie vers une économie circulaire dans la technologie des batteries
L'essor de la technologie des batteries s'accompagne d'un besoin croissant de stratégies durables pour récupérer des matières premières précieuses. Une économie circulaire efficace est essentielle pour réduire la dépendance à l'égard des matières premières primaires tout en minimisant l'impact environnemental de la production de batteries.
Dans le cadre du projet européen ADIR, le Fraunhofer ILT travaille avec huit partenaires de trois pays pour développer un concept de recyclage durable pour les appareils électroniques. Le projet ACROBAT vise à élaborer un plan de recyclage des piles au lithium-fer-phosphate avant qu'elles ne pénètrent le marché à grande échelle. L'objectif du projet est de récupérer plus de 90 % des matériaux critiques. En collaboration avec des partenaires tels qu'Accurec Recycling, le Fraunhofer ILT travaille sur des méthodes de séparation et de traitement innovantes qui sont à la fois écologiquement et économiquement durables. Les experts en laser d'Aix-la-Chapelle développent une méthode de caractérisation en ligne pour évaluer précisément la qualité du matériau actif.
Grâce à son propre procédé de spectroscopie par claquage induit par laser (LIBS), l'institut est en mesure d'identifier et de séparer avec précision des compositions de matériaux complexes. Les chercheurs souhaitent adapter cette technologie au recyclage des piles usagées afin d'améliorer encore la récupération de métaux tels que le cobalt et le tantale. Ici aussi, l'IA peut être intégrée pour analyser les grandes quantités de données issues des mesures laser et optimiser le processus en temps réel. Cette surveillance assistée par l'IA permet un ajustement dynamique des paramètres de recyclage, ce qui réduit les déchets et augmente la qualité des matières premières recyclées.
Conclusion et perspectives
La production de batteries est au cœur de la transition vers l'électromobilité et, par conséquent, au centre des innovations qui allient efficacité, durabilité et excellence technologique. Les technologies et les développements présentés tout au long de la chaîne de production montrent comment les processus laser de pointe peuvent ouvrir la voie à une industrie des batteries durable et compétitive : de la préparation des matières premières et de la production d'électrodes à l'assemblage et au recyclage des cellules. Parallèlement, les systèmes d'analyse et de contrôle assistés par l'IA créent une nouvelle dimension du contrôle des processus qui améliore la qualité et la durabilité de la production et réduit encore les coûts de production.
À l'avenir, les boucles de contrôle assistées par l'IA pourraient permettre une production autonome dans laquelle les processus s'adaptent aux conditions changeantes en temps réel. En outre, les sources de rayons X pilotées par laser et les technologies de caractérisation en ligne ouvrent de nouvelles possibilités en matière d'assurance qualité et d'analyse des matériaux.
Note: Cet article a été traduit à l'aide d'un système informatique sans intervention humaine. LUMITOS propose ces traductions automatiques pour présenter un plus large éventail d'actualités. Comme cet article a été traduit avec traduction automatique, il est possible qu'il contienne des erreurs de vocabulaire, de syntaxe ou de grammaire. L'article original dans Anglais peut être trouvé ici.