New titanium manufacturing process saves energy
Whether for stopping cars or bullets, titanium is the material of choice, but it has always been too expensive for all but the most specialized applications. That could change, however, with a non-melt consolidation process being developed by Oak Ridge National Laboratory and industry partners. The new processing technique could reduce the amount of energy required and the cost to make titanium parts from powders by up to 50 percent, making it feasible to use titanium alloys for brake rotors, artificial joint replacements and armor for military vehicles.
Peter noted that the non-melt approach, which includes roll compaction for directly fabricating sheets from powder, press and sinter techniques to produce net shape components and extrusion, offers many advantages over traditional melt processing.
"Instead of using conventional melt processing to produce products from titanium powder, with the new method the powders remain in their solid form during the entire procedure," Peter said. "This saves a tremendous amount of energy required for processing, greatly reduces the amount of scrap and allows for new alloys and engineered composites."
While powder metallurgy has been used to produce components for many years, titanium products have not widely been fabricated using these methods because of the high cost of conventional titanium powders. Now, however, new low-cost titanium powders are enabling ORNL, International Titanium Powders, Ametek and BAE Systems to develop these technologies for titanium.
In coming years, researchers expect lightweight corrosion-resistant titanium alloys to make their way into many other products, including automobiles, which will benefit from the decreased weight and will be able to deliver improved fuel economy.
Most read news
Organizations
Other news from the department research and development
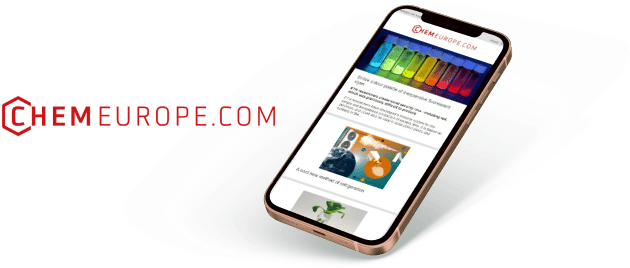
Get the chemical industry in your inbox
By submitting this form you agree that LUMITOS AG will send you the newsletter(s) selected above by email. Your data will not be passed on to third parties. Your data will be stored and processed in accordance with our data protection regulations. LUMITOS may contact you by email for the purpose of advertising or market and opinion surveys. You can revoke your consent at any time without giving reasons to LUMITOS AG, Ernst-Augustin-Str. 2, 12489 Berlin, Germany or by e-mail at revoke@lumitos.com with effect for the future. In addition, each email contains a link to unsubscribe from the corresponding newsletter.