The world's first-ever 4D printing for ceramics
A research team at City University of Hong Kong (CityU) has achieved a ground-breaking advancement in materials research by successfully developing the world's first-ever 4D printing for ceramics, which are mechanically robust and can have complex shapes. This could turn a new page in the structural application of ceramics.
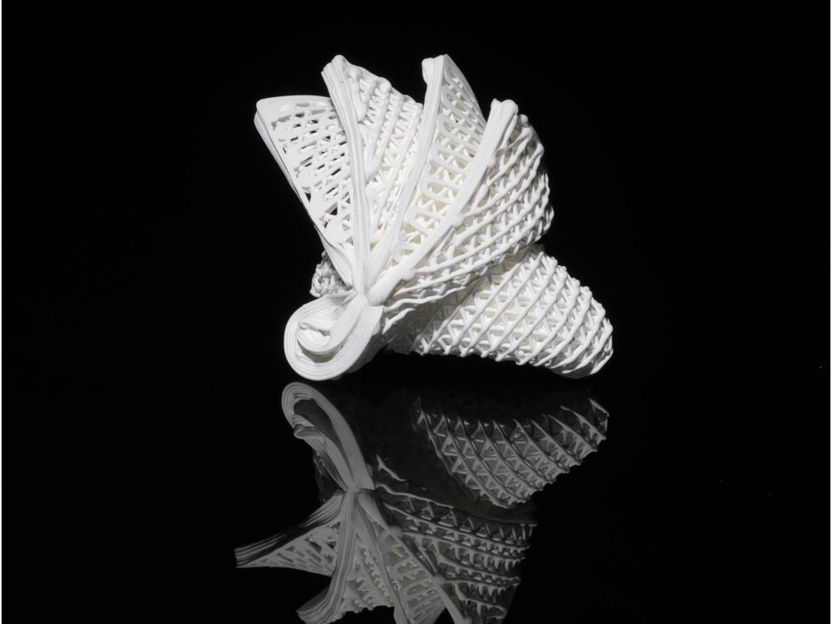
Printed ceramic origami mimicking the Sydney Opera House.
City University of Hong Kong
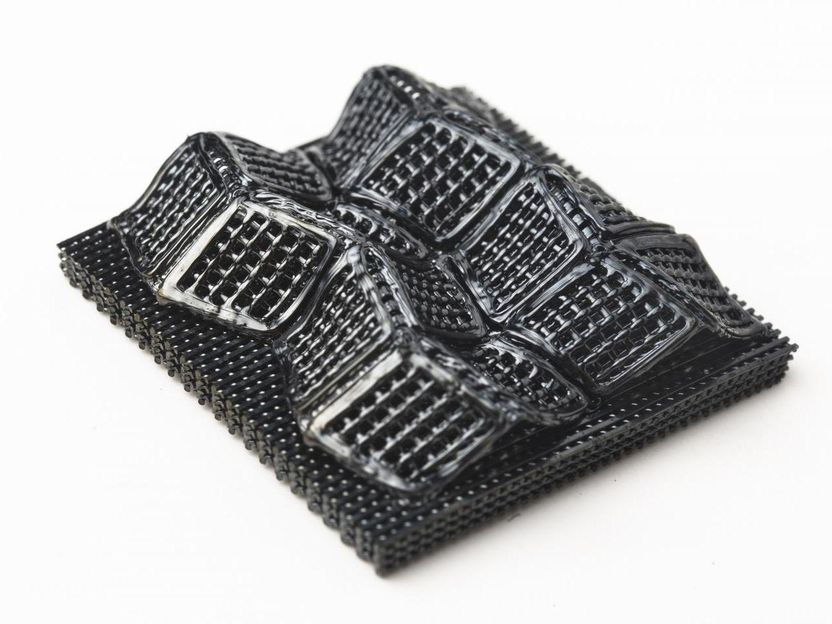
4D-printed ceramic Miura-ori
City University of Hong Kong
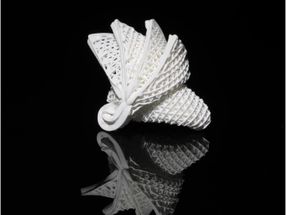
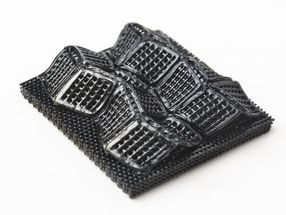
Ceramic has a high melting point, so it is difficult to use conventional laser printing to make ceramics. The existing 3D-printed ceramic precursors, which are usually difficult to deform, also hinder the production of ceramics with complex shapes.
To overcome these challenges, the CityU team has developed a novel "ceramic ink", which is a mixture of polymers and ceramic nanoparticles. The 3D-printed ceramic precursors printed with this novel ink are soft and can be stretched three times beyond their initial length. These flexible and stretchable ceramic precursors allow complex shapes, such as origami folding. With proper heat treatment, ceramics with complex shapes can be made.
The team was led by Professor LU Jian, Vice-President (Research and Technology) and Chair Professor of Mechanical Engineering, who is a distinguished materials scientist with research interests ranging from fabricating nanomaterials and advanced structural materials to the computational simulation of surface engineering.
With the development of the elastic precursors, the research team has achieved one more breakthrough by developing two methods of 4D printing of ceramics.
4D printing is conventional 3D printing combined with the additional element of time as the fourth dimension, where the printed objects can re-shape or self-assemble themselves over time with external stimuli, such as mechanical force, temperature, or a magnetic field.
In this research, the team made use of the elastic energy stored in the stretched precursors for shape morphing. When the stretched ceramic precursors are released, they undergo self-reshaping. After heat treatment, the precursors turn into ceramics.
The resultant elastomer-derived ceramics are mechanically robust. They can have a high compressive strength-to-density ratio (547 MPa on 1.6 g cm-3 microlattice), and they can come in large sizes with high strength compared to other printed ceramics.
"The whole process sounds simple, but it's not," said Professor Lu. "From making the ink to developing the printing system, we tried many times and different methods. Like squeezing icing on a cake, there are a lot of factors that can affect the outcome, ranging from the type of cream and the size of the nozzle, to the speed and force of squeezing, and the temperature."
It took more than two and a half years for the team to overcome the limitations of the existing materials and to develop the whole 4D ceramic printing system.
In the first shaping method, a 3D-printed ceramic precursor and substrate were first printed with the novel ink. The substrate was stretched using a biaxial stretching device, and joints for connecting the precursor were printed on it. The precursor was then placed on the stretched substrate. With the computer-programmed control of time and the release of the stretched substrate, the materials morphed into the designed shape.
In the second method, the designed pattern was directly printed on the stretched ceramic precursor. It was then released under computer-programming control and underwent the self-morphing process.
"With the versatile shape-morphing capability of the printed ceramic precursors, its application can be huge!" said Professor Lu. One promising application will be for electronic devices. Ceramic materials have much better performance in transmitting electromagnetic signals than metallic materials. With the arrival of 5G networks, ceramic products will play a more important role in the manufacture of electronic products. The artistic nature of ceramics and their capability to form complex shapes also provide the potential for consumers to tailor-make uniquely designed ceramic mobile phone back plates.
Furthermore, this innovation can be applied in the aero industry and space exploration. "Since ceramic is a mechanically robust material that can tolerate high temperatures, the 4D-printed ceramic has high potential to be used as a propulsion component in the aerospace field," said Prof Lu.
Riding on the breakthrough in material and 4D-printing technique advancement, Prof Lu said the next step is to enhance the mechanical properties of the material, such as reducing its brittleness.