Pilot plant for manufacture of high-temperature superconductors goes on stream
Deutsche Nanoschicht GmbH, a wholly owned subsidiary of BASF New Business GmbH, has opened its new pilot plant for the manufacture of high temperature superconductors. The facility located in Rheinbach is based on an in-house developed chemical manufacturing process and has a fifty times higher capacity than the company laboratory plant used to date. The pilot plant is an important step on the way to market launch of the superconductors. BASF New Business provides customers with samples of the wire manufactured in the new plant to produce prototypes for innovative, high-efficiency applications in power grids. Primary examples are current limiters and cables for direct and alternating current.
New applications through high-current carrying capacity
Compared to conventional cables, superconducting cables can transmit electric current with negligible loss and therefore much more efficiently, and can transport a much greater amount of energy in relation to the conductor cross-section. High-temperature superconductors already conduct current at the temperature of liquid nitrogen (77 Kelvin / minus 196 degrees Celsius) without resistance. This temperature can be achieved reliably and cost-effectively and maintained during operation by commercial refrigerating machines. The ten to one hundred times higher current-carrying capacity compared to copper allows very compact new cable applications and more lightweight systems for generators and motors. Current limiters compensate current peaks in public or industrial distribution grids and can thereby prevent power failures caused by short circuits.
Dedicated process offers cost advantage
To produce wires for high-temperature superconductors, Deutsche Nanoschicht uses a dedicated coating process based on chemical solution deposition. In a continuous process, very thin films of a superconducting material and several buffer layers are applied to a metal strip. In contrast to other, physical methods, the chemical process requires neither a vacuum nor a clean room environment. This presents a decisive advantage for the manufacturing costs of the superconducting wires.
"Our unique coating technology will enable us in future to produce superconductors with the price-performance ratio necessary for wide-scale launch in the energy sector and further consolidate our position in the energy and resources growth market," says Dr. Guido Voit, Managing Director of BASF New Business. "With the new pilot plant, we can offer our customers superconducting wire in good and reliable quality." With immediate effect, the team is not only providing customers with samples but also conducting production technology trials. "Our manufacturing process is highly scalable. We are planning to put a large-scale plant into operation in the medium term."
Most read news
Other news from the department manufacturing
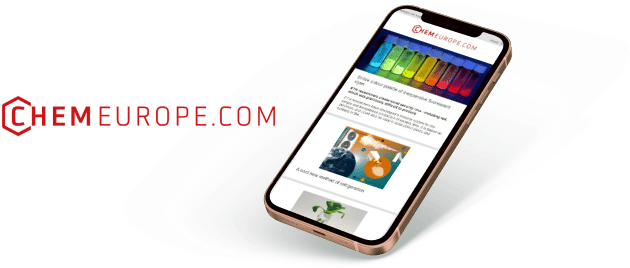
Get the chemical industry in your inbox
By submitting this form you agree that LUMITOS AG will send you the newsletter(s) selected above by email. Your data will not be passed on to third parties. Your data will be stored and processed in accordance with our data protection regulations. LUMITOS may contact you by email for the purpose of advertising or market and opinion surveys. You can revoke your consent at any time without giving reasons to LUMITOS AG, Ernst-Augustin-Str. 2, 12489 Berlin, Germany or by e-mail at revoke@lumitos.com with effect for the future. In addition, each email contains a link to unsubscribe from the corresponding newsletter.