NIST calculates high cost of hydrogen pipelines, shows how to reduce it
The National Institute of Standards and Technology (NIST) has put firm numbers on the high costs of installing pipelines to transport hydrogen fuel - and also found a way to reduce those costs.
Pipelines to carry hydrogen cost more than other gas pipelines because of the measures required to combat the damage hydrogen does to steel's mechanical properties over time. NIST researchers calculated that hydrogen-specific steel pipelines can cost as much as 68 percent more than natural gas pipelines, depending on pipe diameter and operating pressure. By contrast, a widely used cost model suggests a cost penalty of only about 10 percent.
But the good news, according to the new NIST study, is that hydrogen transport costs could be reduced for most pipeline sizes and pressures by modifying industry codes to allow the use of a higher-strength grade of steel alloy without requiring thicker pipe walls. The stronger steel is more expensive, but dropping the requirement for thicker walls would reduce materials use and related welding and labor costs, resulting in a net cost reduction. The code modifications, which NIST has proposed to the American Society of Mechanical Engineers (ASME), would not lower pipeline performance or safety, the NIST authors say.
"The cost savings comes from using less - because of thinner walls - of the more expensive material," says NIST materials scientist James Fekete, a co-author of the study. "The current code does not allow you to reduce thickness when using higher-strength material, so costs would increase. With the proposed code, in most cases, you can get a net savings with a thinner pipe wall, because the net reduction in material exceeds the higher cost per unit weight."
The NIST study is part of a federal effort to reduce the overall costs of hydrogen fuel, which is renewable, nontoxic and produces no harmful emissions. Much of the cost is for distribution, which likely would be most economical by pipeline. The U.S. contains more than 300,000 miles of pipelines for natural gas but very little customized for hydrogen. Existing codes for hydrogen pipelines are based on decades-old data. NIST researchers are studying hydrogen's effects on steel to find ways to reduce pipeline costs without compromising safety or performance.
As an example, the new code would allow a 24-inch pipe made of high-strength X70 steel to be manufactured with a thickness of 0.375 inches for transporting hydrogen gas at 1500 pounds per square inch (psi). (In line with industry practice, ASME pipeline standards are expressed in customary units.) According to the new NIST study, this would reduce costs by 31 percent compared to the baseline X52 steel with a thickness of 0.562 inches, as required by the current code. In addition, thanks to its higher strength, X70 would make it possible to safely transport hydrogen through bigger pipelines at higher pressure (36-inch diameter pipe to transport hydrogen at 1500 psi) than is allowed with X52, enabling transport and storage of greater fuel volumes. This diameter-pressure combination is not possible under the current code.
The proposed code modifications were developed through research into the fatigue properties of high-strength steel at NIST's Hydrogen Pipeline Material Testing Facility. In actual use, pipelines are subjected to cycles of pressurization at stresses far below the failure point, but high enough to result in fatigue damage. Unfortunately, it is difficult and expensive to determine steel fatigue properties in pressurized hydrogen. As a result, industry has historically used tension testing data as the basis for pipeline design, and higher-strength steels lose ductility in such tests in pressurized hydrogen. But this type of testing, which involves steadily increasing stress to the failure point, does not predict fatigue performance in hydrogen pipeline materials, Fekete says.
NIST research has shown that under realistic conditions, steel alloys with higher strengths (such as X70) do not have higher fatigue crack growth rates than lower grades (X52). The data have been used to develop a model for hydrogen effects on pipeline steel fatigue crack growth, which can predict pipeline lifetime based on operating conditions.
Organizations
Other news from the department science
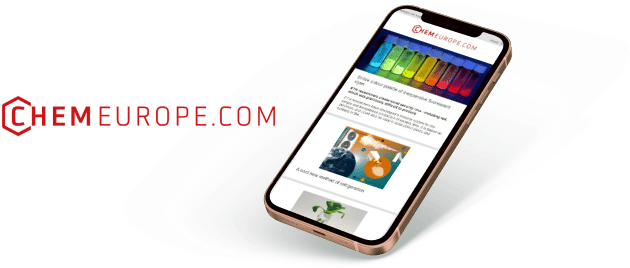
Get the chemical industry in your inbox
By submitting this form you agree that LUMITOS AG will send you the newsletter(s) selected above by email. Your data will not be passed on to third parties. Your data will be stored and processed in accordance with our data protection regulations. LUMITOS may contact you by email for the purpose of advertising or market and opinion surveys. You can revoke your consent at any time without giving reasons to LUMITOS AG, Ernst-Augustin-Str. 2, 12489 Berlin, Germany or by e-mail at revoke@lumitos.com with effect for the future. In addition, each email contains a link to unsubscribe from the corresponding newsletter.