The thinnest, smoothest metallic lines in the world helps speed up miniaturisation of electronic devices
New method creates super-thin, high integrity, continuous metal lines that surpass today’s semiconductor industry requirements
Scientists from Singapore A*STAR’s Institute of Materials Research and Engineering (IMRE), University of Cambridge (UK) and Sungkyunkwan University (South Korea) have created metallic lines so thin and smooth that they can only be seen using powerful electron microscopes. This research will be published in Advanced Functional Materials.
At line widths of just 7 nm, their line width roughness , which are the variations in thickness along the line itself, stands at 2.9 nm, a value which is below the 2010 target of 3.2 nm and closer to 2011’s target line width roughness of 2.8 nm indicated in the International Technology Roadmap for Semiconductors .
The ability to create such distinct lines and patterns on a sub-10 nm scale level is essential in the further miniaturisation of electronic components. Rough, undefined patterns and lines results in poorly made, energy-inefficient devices. The process is very delicate and precise because of the scale at which the work is done. For comparison, the width of the average human hair is 100 µm, which is about 14,000 times the width of a single 7 nm-wide metal line.
“Our thin, unbroken and smooth lines are important in ensuring the efficiency of ever shrinking electronic devices and may lead to more powerful processors. Furthermore, our work shows that continuous metallic lines as small as 4 nm are possible to make”, says Dr MSM Saifullah, a Research Scientist with IMRE. The method could be potentially used to make interconnects, the ‘highways’ that carry electrical pulses and data in extremely small integrated circuits (ICs). The smoother and uninterrupted ‘highways’ lead to faster data transfer rates and less energy wasted, in the form of heat.
The novelty of the method was in the material and the technique that was used. The current “lift-off” approach for making metal lines at this scale requires more steps, uses more materials and results in rough, and quite often broken lines on a sub-10 nm scale. The researchers used an organometallic material which is made up of a metallic and an organic component. Using a combination of electron beam lithography and subsequent gas treatment, the researchers were able to easily chip away the organic portions in a uniform manner, leaving the desired metallic patterns, in this case, thin metal lines.
“The published results is a testament to the cutting-edge nanotechnology research that is done in Singapore, where we push, and sometimes lead, the rest of the world”, says Prof Andy Hor, IMRE’s new Executive Director, who took the helm of Singapore’s materials research institute in June 2010.
“Our obvious expertise in the area of nanopatterning is also a reason why we are driving a concerted effort for the industry to adopt technologies such as this into their manufacturing processes”, explains Prof Hor. IMRE will be launching an Industrial Consortium on Nanoimprinting (ICON) on 3 August 2010 to encourage industry to take full advantage of the benefits that advanced nanopatterning has to offer.
Most read news
Organizations
Other news from the department science
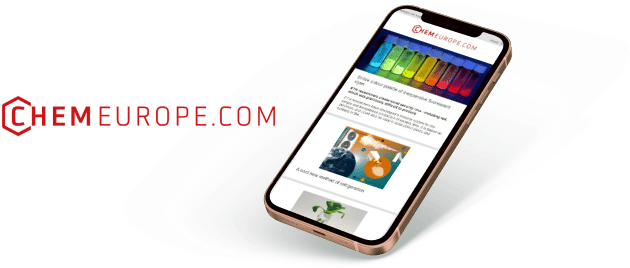
Get the chemical industry in your inbox
By submitting this form you agree that LUMITOS AG will send you the newsletter(s) selected above by email. Your data will not be passed on to third parties. Your data will be stored and processed in accordance with our data protection regulations. LUMITOS may contact you by email for the purpose of advertising or market and opinion surveys. You can revoke your consent at any time without giving reasons to LUMITOS AG, Ernst-Augustin-Str. 2, 12489 Berlin, Germany or by e-mail at revoke@lumitos.com with effect for the future. In addition, each email contains a link to unsubscribe from the corresponding newsletter.