From trash to treasure: new method efficiently regenerates spent lithium cobalt oxide batteries
A significant step toward sustainable battery reuse
lithium-ion batteries are essential for powering electronics and electric vehicles, yet their limited lifespan—typically 5 to 8 years—leads to massive volumes of hazardous waste. Current recycling technologies such as pyrometallurgy and hydrometallurgy are energy-intensive, environmentally harmful, and inefficient, especially when dealing with severely degraded cathodes. These materials often suffer from structural collapse, lithium depletion, and the formation of surface spinel phases like Co₃O₄, which hinder regeneration. While direct recycling offers a cleaner alternative, it struggles with uneven lithium diffusion and high energy barriers. These challenges highlight the urgent need for innovative, low-impact methods that can effectively restore the functionality of spent LIB cathodes.、
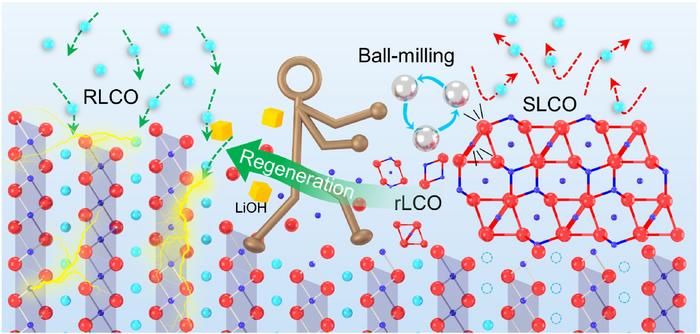
Schematic illustration of the regeneration process for heavily degraded lithium cobalt oxide (LCO) cathodes. Through ball milling, the spinel-phase structured spent LCO (SLCO) is transformed into an amorphous intermediate (rLCO), facilitating lithium replenishment and structural restoration. Subsequent treatment with LiOH enables the formation of regenerated LCO (RLCO) with restored layered architecture and electrochemical performance.
Energy Materials and Devices, Tsinghua University Press
Published in March 2025, in Energy Materials and Devices, a collaborative study unveiled a ball milling-assisted technique to revitalize aged LiCoO₂ (LCO) cathodes. By transforming degraded crystal structures into amorphous intermediates, followed by sintering at high temperatures, the researchers successfully reconstructed the layered architecture and regained battery-grade performance. The regenerated cathodes demonstrated a capacity of 179.10 mAh·g⁻¹ at 0.5 C, matching that of new commercial materials. The method offers compelling advantages over conventional recycling pathways in terms of efficiency, cost, and environmental footprint—marking a significant step toward sustainable battery reuse.
At the heart of this study lies a structural transformation strategy driven by ball milling. The process converts the rigid and defect-prone spinel phase (Co₃O₄), commonly formed on degraded LCO cathodes, into a homogeneous amorphous phase. This intermediate not only alleviates internal stress but also facilitates uniform lithium reintegration during subsequent high-temperature sintering. The regenerated LCO (RLCO) cathodes achieved a high discharge capacity of 179.10 mAh·g⁻¹ at 0.5 C, closely matching commercial standards. Performance metrics were promising: 91.7% initial Coulombic efficiency and 88% capacity retention after 100 cycles. Finite element modeling confirmed superior lithium diffusion within the amorphous phase, compared to conventional repair techniques. Economically, the method reduces recycling costs by approximately 25% compared to hydrometallurgy, eliminates the generation of toxic wastewater, and offers a projected profit of $1,503 per kilogram of recovered material. Advanced characterization techniques—including HAADF-STEM, XRD, and XPS—verified the full restoration of the layered crystal structure and the removal of Co²⁺-related defects. The results address longstanding barriers in direct cathode regeneration and lay the foundation for extending this method to other widely used cathode chemistries, such as nickel-manganese-cobalt (NMC) and lithium iron phosphate (LFP).
“This work reframes structural degradation as an opportunity,” said Dr. Guangmin Zhou, co-corresponding author of the study. “The amorphous intermediate acts as a ‘repair highway’ for lithium, offering a generalizable strategy for regenerating other cathode materials like NMC or LFP.” Independent experts have highlighted the method’s potential for large-scale deployment, citing its ability to cut raw material dependency and reduce electronic waste. The study’s balance of scientific rigor and practical feasibility makes it an important reference for the future of battery recycling.
This regeneration technique holds strong promise for sustainable battery technology and circular economy efforts. By enabling efficient, large-scale recycling of degraded LCO cathodes, the method could significantly reduce dependence on virgin cobalt and lithium—critical resources with constrained and geopolitically sensitive supply chains. Its cost-effectiveness and operational simplicity position it well for industrial adoption, with potential integration into existing battery manufacturing workflows. Furthermore, it aligns with stringent environmental regulations such as the EU Battery Regulation, offering a low-carbon, waste-free alternative to legacy recycling systems. Beyond LCO, the underlying principles of amorphous-phase engineering and structural restoration could be applied to other chemistries, supporting broader innovation in next-generation energy storage solutions.
Original publication
Other news from the department science
These products might interest you
Most read news
More news from our other portals
See the theme worlds for related content
Topic World Battery Technology
The topic world Battery Technology combines relevant knowledge in a unique way. Here you will find everything about suppliers and their products, webinars, white papers, catalogs and brochures.
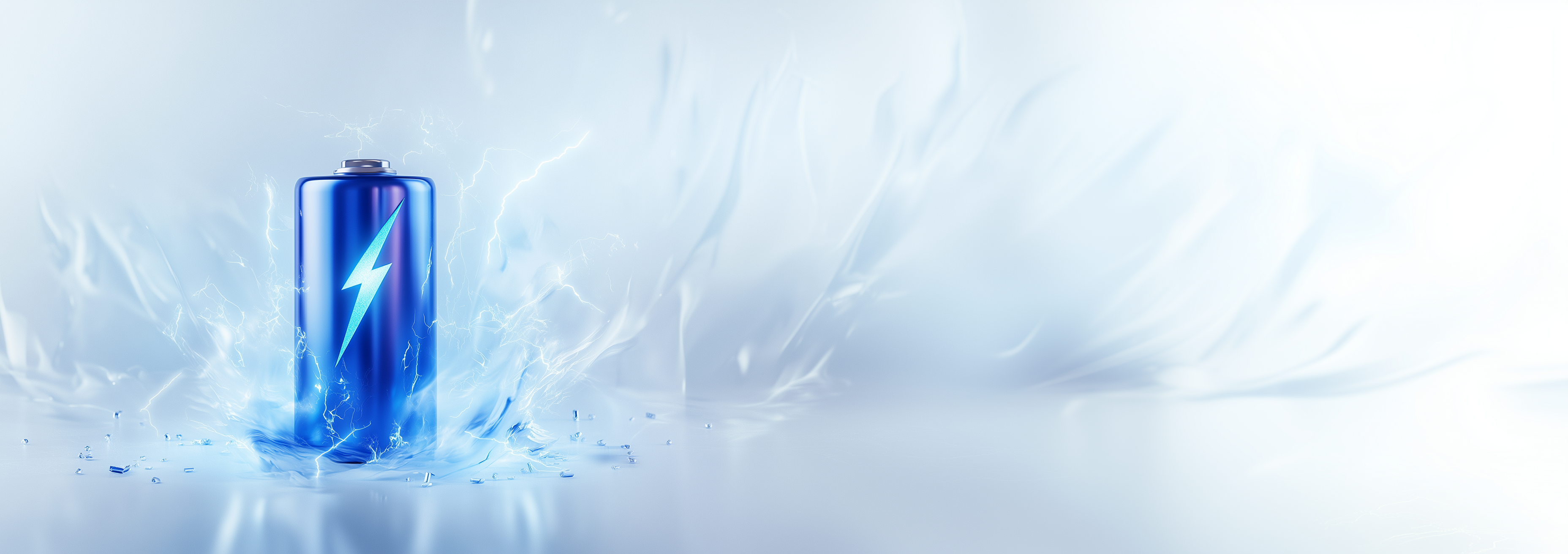
Topic World Battery Technology
The topic world Battery Technology combines relevant knowledge in a unique way. Here you will find everything about suppliers and their products, webinars, white papers, catalogs and brochures.