Sustainable chemistry: Researchers develop method to reduce carbon footprint of chemical industry
An efficient way to hydrogenate nitrogen-containing aromatic compounds
Successful reduction of the chemical manufacturing industry’s environmental impact relies on finding a greener way to make the chemical building blocks for common and massively consumed compounds.
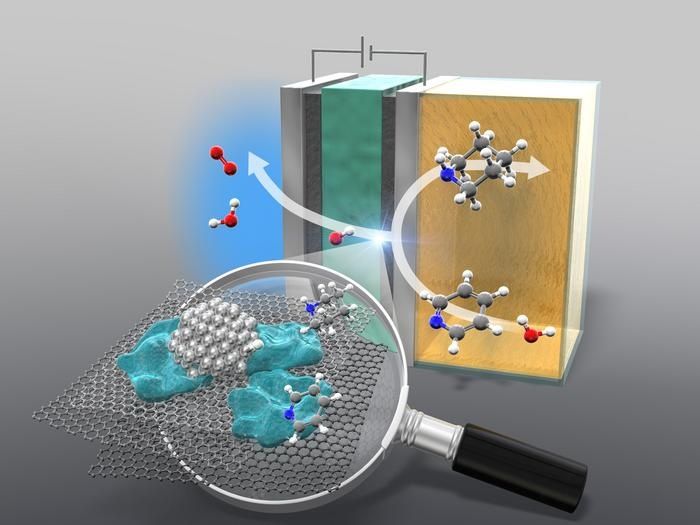
The anion-exchange membrane reactor hydrogenates pyridine to piperidine.
Yokohama National University
It’s no secret manufacturing processes have some of the most impactful and intense effects on the environment, with the chemical manufacturing industry topping the charts for both energy consumption and emissions output. While this makes sense thanks to the grand scale in which manufactured chemicals are involved in daily life, it still leaves a lot to be desired for sustainability’s sake. By focusing on renewable energy sources and alternative methods for creating the chemical building blocks of some of the most commonly used compounds, researchers hope to reduce the chemical manufacturing industry’s footprint with some green innovation.
Researchers published their results in the Journal of the American Chemical Society on October 7.
The main focus of this study is cyclic amines, as these are the most important building blocks for fine chemicals. These compounds are arranged in a ring and, in this case, have a nitrogen atom. One of the stars of the show is pyridine, which gives way to piperidine, a cyclic amine that is of key importance in the fine chemical industry. Piperidine, for example, provides the framework for many materials such as FDA-approved drugs, pesticides and everyday materials used in many people’s lives.
Typical methods of adding hydrogen to a nitrogen-containing cyclic amine involve using hydrogen gas as a proton and electron source. The hydrogenation process relies on hydrogen obtained through the steam reforming of methane, a major greenhouse gas. Not only is this method energy-intensive, but it also is responsible for around 3% of the global carbon dioxide emissions. This process is also highly dependent on fossil fuels and takes a great amount of energy. Fortunately, researchers have found a way around this by developing an anion-exchange membrane (AEM) electrolyzer.
An AEM electrolyzer allows for the hydrogenation of different kinds of pyridines at ambient temperature and pressure, without having to use acidic additives like in traditional methods. The electrolyzer works to split water into its components, atomic hydrogen and oxygen. The atomic hydrogen obtained is then added to the cyclic compound. The AEM electrolyzer also demonstrates great versatility with other nitrogen-containing aromatics, making it a promising path for a wide set of applications. Additionally, by developing a method that can be used at ambient temperatures and pressures, the electrical energy needed for the process is dramatically decreased.
“The method offers significant potential for industrial-scale applications in pharmaceuticals and fine chemicals, contributing to the reduction of carbon emissions and advancing sustainable chemistry,” said Naoki Shida, first author of the study and researcher at Yokohama National University.
This process uses water and renewable electricity as an energy source, contrasting with the reliance on fossil fuels for the conventional method. Efficiency has not been compromised with this method and the percent yield on a large scale is 78%, further affirming this technology can be reasonably scalable. One issue that might be encountered is an increase in cell voltage during the electrolysis process, but this can be mitigated through either improved AEM or, preferably, designing an AEM with organic electrosynthesis specifically in mind.
For the electrocatalytic hydrogenation technology to catch on and make a difference, it needs to be scalable to an industrial scale for pharmaceutical and fine chemical companies to use it. The more this technology is used, the easier it is to transition it to be used for other nitrogen-containing aromatic compounds, further expressing the practicality of the electrocatalytic hydrogenation process. Ideally, this method would establish itself as the alternative to traditional methods used in the chemical industry and down the line would reduce the overall carbon footprint chemical manufacturing leaves behind.
Naoki Shida, Mahito Atobe, Yugo Shimizu, Akizumi Yonezawa, Juri Harada, Yuka Furutani and Yusuke Muto of the Department of Chemistry and Life Science at Yokohama National Univeristy with Naoki Shida and Mahito Atobe also of the Institute of Advanced Sciences at Yokohama National University and Naoki Shide of PRESTO at the Japan Science and Technology Agency, Ryo Kurihara and Kazuhide Kamiya of the Research Center for Solar Energy Chemistry at Osaka Univeristy, Junko N. Kondo of the Institute of Innovative Research at the Tokyo Institute of Technology, Eisuke Sato, Koichi Mitsudo and Seiji Suga of the Division of Applied Chemistry at Okayama University, Shoji Iguchi of the Graduate School of Engineering at Kyoto Univeristy, and Kazuhide Kamiya of the Innovative Catalysis Science Division at Osaka University contributed to this research.
Original publication
Naoki Shida, Yugo Shimizu, Akizumi Yonezawa, Juri Harada, Yuka Furutani, Yusuke Muto, Ryo Kurihara, Junko N. Kondo, Eisuke Sato, Koichi Mitsudo, Seiji Suga, Shoji Iguchi, Kazuhide Kamiya, Mahito Atobe; "Electrocatalytic Hydrogenation of Pyridines and Other Nitrogen-Containing Aromatic Compounds"; Journal of the American Chemical Society, 2024-10-7
Other news from the department science
Most read news
More news from our other portals
See the theme worlds for related content
Topic world Synthesis
Chemical synthesis is at the heart of modern chemistry and enables the targeted production of molecules with specific properties. By combining starting materials in defined reaction conditions, chemists can create a wide range of compounds, from simple molecules to complex active ingredients.
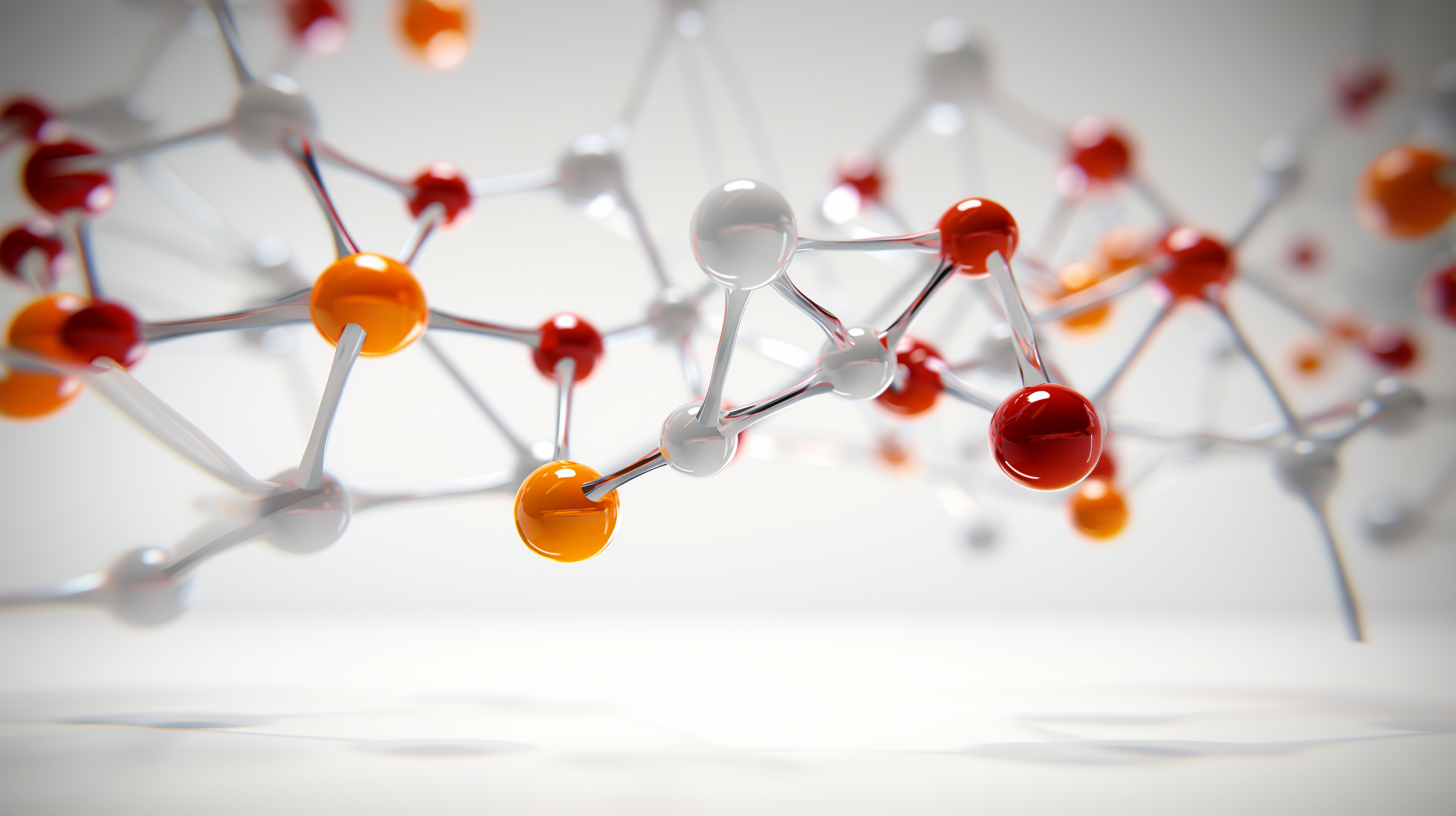
Topic world Synthesis
Chemical synthesis is at the heart of modern chemistry and enables the targeted production of molecules with specific properties. By combining starting materials in defined reaction conditions, chemists can create a wide range of compounds, from simple molecules to complex active ingredients.