Recovering instead of shredding: recycling batteries more efficiently
KIT researchers are working with industry to develop a more sustainable recycling process to recycle materials from lithium-ion batteries more effectively
The market for electric cars is growing rapidly and with it the demand for lithium-ion batteries (LIB). Their recycling is also an important component in the production cycle. Current processes break down the active battery materials into their molecular components - using large amounts of energy and chemicals. In a large-scale joint project, researchers from the Karlsruhe Institute of Technology (KIT) and partners from industrial companies are therefore developing a complete process chain to recycle used batteries more efficiently by recovering the active components while preserving their function. The Federal Ministry of Education and Research is funding the project with almost three million euros.
The electrification of mobility is an important contribution to achieving Germany's climate protection targets and is therefore a megatrend for the automotive industry in Germany. "The associated high demand for lithium-ion batteries requires sustainable and closed material cycles - from the battery materials through the entire life cycle to recycling - as well as a recyclable production of battery cells," says Dr. Marco Gleiß from the Institute of Mechanical Process Engineering and Mechanics, who is coordinating the joint project "Agile process chain for direct recycling of lithium-ion batteries and regeneration of active materials" (DiRecReg) on the KIT side. "By closing the value chain, we can simultaneously reduce Germany's and the European Union's dependence on raw materials," says Gleiß.
Preserving instead of shredding or decomposing
Current processes shred the battery cells and dissolve the active materials down to the molecular level in order to later extract them from the liquid in the form of metal salts. Although up to 90 percent of the critical elements, such as cobalt, nickel and manganese, can be recovered in this way, the amount of energy and chemicals required is very high. In addition, battery material has to be produced from scratch from the recovered materials, which requires a great deal of energy and raw materials. Newer, promising approaches for used batteries and production rejects are based on the direct recycling of active materials. "The active materials are no longer completely dissolved. Instead, they are broken down into their individual cell components and then mechanically separated in order to recover them as purely as possible," explains Gleiß.
Active recovery of battery materials still in its infancy
However, such a process chain for direct recycling has not yet become established in the industry. It is not yet possible to predict the material behavior of the recovered recyclate. Furthermore, there are no criteria or rules for assessing the usability of the aged material. Furthermore, there is currently still a lack of practical, economical solutions for dismantling the various battery packs down to the individual components without great effort. "Our joint project addresses these critical points and is primarily concerned with the development of an agile process chain for the direct recycling of lithium-ion batteries and the regeneration of the active materials recovered in this way," says project coordinator Dr. Thomas Dreyer from Weber Ultrasonics AG. It is also important that the process is variably tailored to different starting materials for battery production as well as for production rejects and can process different battery formats and designs. "The aim is also to replace the energy-intensive process steps of the recycling methods currently in use and to supply sustainably recycled, high-quality secondary materials in the sense of a circular economy," says Gleiß.
Three million euros for joint project with four research and seven industrial partners
The DiRecReg project will run for three years and is being funded by the Federal Ministry of Education and Research with 2.95 million euros. The project consortium, led by Weber Ultrasonics AG, consists of ten partners and one associated partner. It comprises four KIT institutes - wbk Institute of Production Engineering, Institute of Mechanical Process Engineering and Mechanics, Institute of Applied Geosciences - Chair of Geochemistry & Deposit Science and the Thin Film Technology working group - as well as six industrial partners: the battery cell manufacturer PowerCo SE, the materials technology and recycling group Umicore AG & Co. KG, the experts for gripping and handling technology SCHUNK SE & Co. KG, the company FIBRO LÄPPLE TECHNOLOGY GMBH as system integrator and the system manufacturers Carl Padberg Zentrifugenbau GmbH and Weber Ultrasonics AG. In addition, Siemens is supporting the project from a control and digitalization perspective as part of an associated partnership.
Note: This article has been translated using a computer system without human intervention. LUMITOS offers these automatic translations to present a wider range of current news. Since this article has been translated with automatic translation, it is possible that it contains errors in vocabulary, syntax or grammar. The original article in German can be found here.
Other news from the department science
These products might interest you
Most read news
More news from our other portals
See the theme worlds for related content
Topic World Battery Technology
The topic world Battery Technology combines relevant knowledge in a unique way. Here you will find everything about suppliers and their products, webinars, white papers, catalogs and brochures.
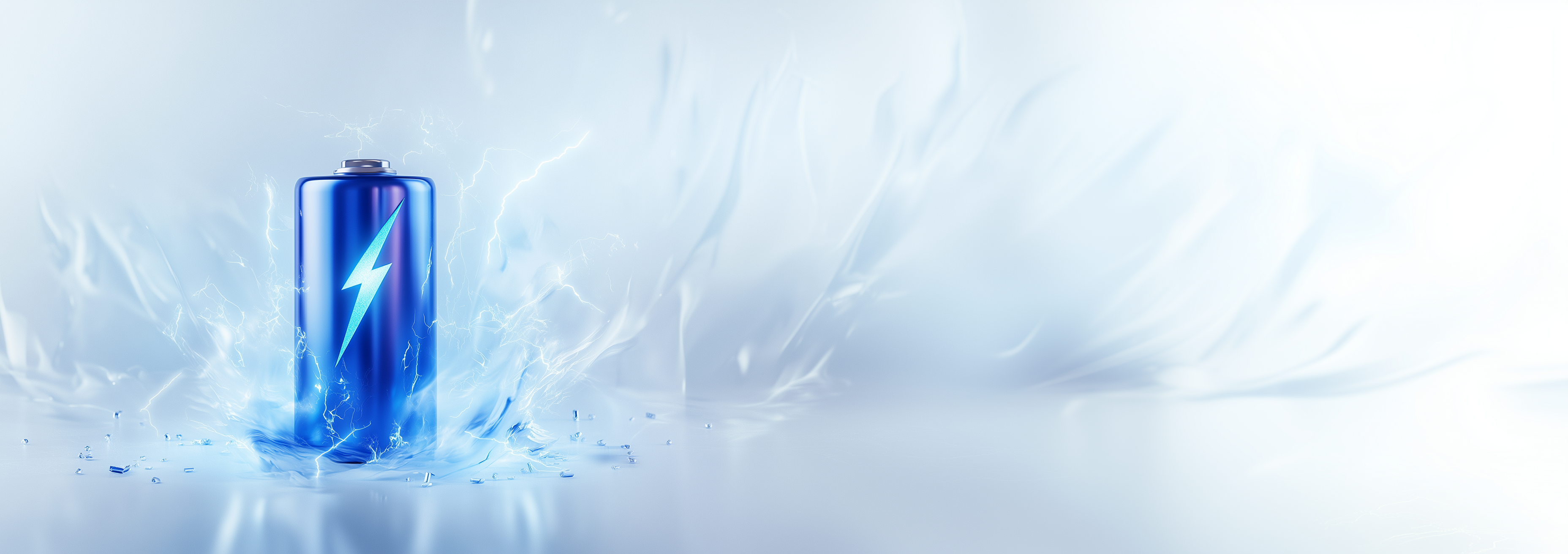
Topic World Battery Technology
The topic world Battery Technology combines relevant knowledge in a unique way. Here you will find everything about suppliers and their products, webinars, white papers, catalogs and brochures.