Durable, inexpensive electrocatalyst generates clean hydrogen and oxygen from water
hydrogen is a highly combustible gas that can help the world achieve its clean energy goals if manufactured in an environmentally responsible way. The primary hurdle to creating hydrogen gas from water is the large amount of energy required for the electrolysis of water, or splitting water molecules into hydrogen gas (H2) and oxygen (O2). A new electrocatalyst made of nickel (Ni), iron (Fe) and silicon (Si) that decreases the amount of energy required to synthesize H2 from water has been manufactured in a simple and cost-effective way, increasing the practicality of H2 as a clean and renewable energy of the future.
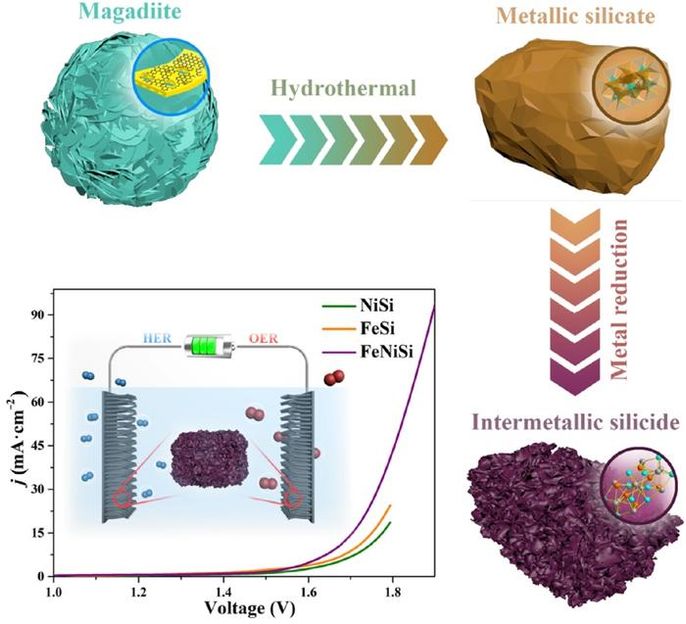
Natural clay magadiite containing silicon (Si) was heated in a sealed vessel in a water-based solution containing iron chloride (FeCl3) and nickel chloride (NiCl2) to create a metallic silicate made up of nickel (Ni), iron (Fe) and Si. The metallic silicate was then reduced by adding electrons to metallic silicate atoms with magnesium, salt and heat to create the more organized intermetallic silicide (ferric-nickel silicide) structure. The graph illustrates the lower voltage required for the ferric-nickel silicide (FeNiSi) alloy electrocatalyst to produce hydrogen and oxygen gas compared to NiSi and FeSi alloys.
Nano Research Energy, Tsinghua University Press
Most H2 produced today is derived from fossil fuels, which contributes to global warming. Manufacturing H2 from water through the hydrogen evolution reaction (HER) requires the use of a catalyst, or agent that lowers the amount of energy required for a chemical reaction. Until recently, these catalysts were made up of rare earth metals, like platinum, reducing the cost-efficiency and practicality of clean hydrogen production. A group of material scientists from Dalian University of Technology in Dalian, China manufactured an electrocatalyst, or a catalyst that uses electricity, using inexpensive materials and methods to effectively decrease the energy required to generate clean H2 from water. Importantly, the ferric-nickel silicide (FeNiSi) alloy, or mixture, also reduces the energy required to generate O2 from water, making the catalyst bifunctional.
The researchers published their study in Nano Research Energy on November 3, 2023.
“What really limits the development and practical application of water electrolysis technology is electrocatalytic materials. At present, common catalysts, such as precious metals…, are mostly single-function catalysts, which limits the practical application of water electrolysis for hydrogen production. Therefore, the research and development of efficient, stable, cheap and environmentally friendly bifunctional electrocatalytic materials is a primary goal in the field of electrocatalysis,” said Yifu Zhang, senior author of the study and researcher in the School of Chemistry at Dalian University of Technology.
Transition metal silicide alloys are unique compounds that are commonly used in energy-related fields, are cheaply produced and show promise as potential water hydrolysis electrocatalysts. These alloys are made from transition metals, which are excellent catalysts that freely donate and accept electrons in chemical reactions, and Si atoms, which enhance the stability, heat resistance and accessibility of alloy transition metal atoms when electricity is applied.
Fe and Ni, two transition metals, are well-suited for use in a transition metal silicide for water splitting. “Nickel silicide has been… deeply studied for its low resistance and high metal activity, especially… in electrochemical fields. In addition, many recent studies have shown that Fe-Ni based materials have considerable potential in the field of electrochemical water splitting. The aim of this work was to develop a low-cost, environmentally friendly route to prepare iron nickel silicide as a bifunctional electrolytic water catalyst (EWS),” said Zhang.
The research team manufactured FeNiSi in two steps. First, natural clay magadiite, a source of silicon, iron chloride and nickel chloride were heated under pressure to create a ferric-nickel silicate. The ferric-nickel silicate was then combined and heated with magnesium and sodium chloride (table salt) to develop the ordered structure of the FeNiSi alloy. Importantly, this was the first time a metallic silicide alloy had been manufactured using this type of chemical reaction using metallic silicates as a reaction material.
Electron microscopy and X-ray characterization techniques revealed that the manufacturing process created many pore structures in the final FeNiSi alloy, increasing its surface area and overall electrocatalytic performance. The FeNiSi alloy lowers the potential required to split oxygen and hydrogen from water by 308 mV for the oxygen evolution reaction (OER) and 386 mV for the HER, respectively, at a current of 10 mA·cm−2. The electrocatalyst also demonstrated sufficient durability after 15 hours of use.
The research team looks forward to FeNiSi and other transition metal silicates contributing to the synthesis of clean hydrogen gas for future energy needs. “This work not only provides an easy method for the synthesis of intermetallic silicide with considerable porous structures but also allows the intermetallic silicide to be considered as a bifunctional electrocatalyst for EWS. Low-cost and efficient intermetallic silicide electrocatalysts will provide new opportunities for… renewable energy conversion,” said Zhang.