Making materials more durable through science
Researchers develop molecule that reduces wear and tear
A team at Sandia National Laboratories developed a molecule that helps change the way some materials react to temperature fluctuations, which makes them more durable. It’s an application that could be used in everything from plastic phone cases to missiles.
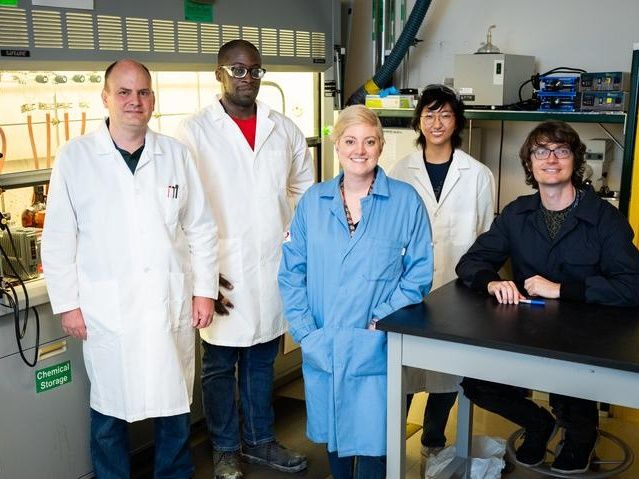
Chad Staiger, Kenneth Lyons, Erica Redline, Alana Yoon and Eric Nagel, left to right, are part of a research team helping make materials more durable at Sandia National Laboratories.
Craig Fritz/Sandia National Laboratories
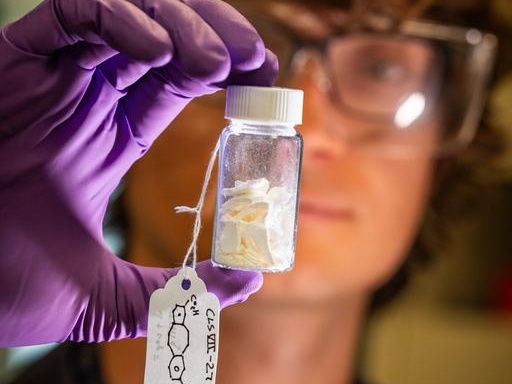
Eric Nagel showing the latest batch of material developed by his team at Sandia National Laboratories as they work to reproduce a molecule that changes the traditional behavior of polymers.
Craig Fritz/Sandia National Laboratories
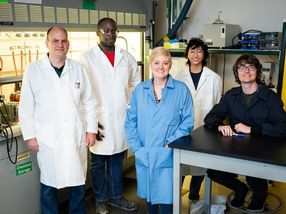
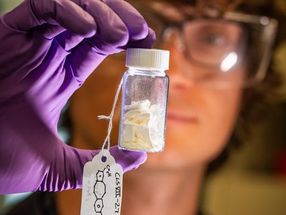
Polymers, which include various forms of plastics, are made up of many smaller molecules, bonded together. This bond makes them especially strong and an ideal product to be used to protect delicate components in a wide variety of items. But with time, use and exposure to different environments, all materials begin to deteriorate.
Hot to cold, cold to hot, the big problem
One of the biggest factors in materials deterioration is repeated exposure from hot to cold temperatures and back. Most materials expand when heated and contract when cooled, but each material has its own rate of change. Polymers, for example, expand and contract the most, while metals and ceramics contract the least.
Erica Redline, a materials scientist who leads the team, said most items are made up of more than one kind of material.
“Take for example, your phone, which has a plastic housing, coupled to a glass screen, and inside that, the metals and ceramics that make up the circuitry,” Redline said. “These materials are all screwed, glued or somehow bonded together and will start expanding and contracting at different rates, putting stresses on one another which can cause them to crack or warp over time.”
Redline said she kept hearing the same complaint from Sandia’s many customers.
“They’re always talking about thermal expansion mismatch problems and how their existing systems are hard to work with because of all the filler they need to add to compensate,” Redline said.
With that, Redline’s idea was born.
“I thought, what if I conjured up a perfect material, what would that look like,” Redline said.
Redline thinks she’s done it, with the help of her team Chad Staiger, Jason Dugger, Eric Nagel, Koushik Ghosh, Jeff Foster, Kenneth Lyons, Alana Yoon and academic alliance collaborators Professor Zachariah Page and graduate student Meghan Kiker.
The molecule in action
The team modified a molecule so that it can easily be incorporated into a polymer to change its properties.
“This really is a unique molecule that when you heat it up, instead of it expanding, it actually contracts by undergoing a change in its shape,” Redline said.
“When it’s added to a polymer, it causes that polymer to contract less, hitting expansion and contraction values similar to metals. To have a molecule that behaves like metal is pretty remarkable.”
Endless possibilities
This molecule could be used in endless ways. Polymers are used as protective coatings in electronics, communications systems, solar panels, automotive components, printed circuit boards, aerospace applications, defense systems, flooring and more.
“The molecule not only solves current issues but significantly opens up design space for more innovations in the future,” said Jason Dugger, a Sandia chemical engineer who has been looking at potential applications, especially in defense systems.
Another key to this invention is that it can be incorporated into different parts of a polymer at different percentages, in 3D printing.
“You could print a structure with certain thermal behaviors in one area, and other thermal behaviors in another to match the materials in different parts of the item,” Dugger said.
Another benefit is helping reduce the weight of materials by eliminating heavy fillers.
“It would enable us to do things much lighter to save mass,” Dugger said. “That is especially important when launching a satellite, for example. Every gram we can save is huge.”
Redline said she has also been approached by an epoxy formulator who believes this molecule could be incorporated into adhesives.
The next step
The team has only created this molecule in small quantities, but they are working to find a way to scale up production so that other Sandia researchers can test the molecule to fit mission needs.
Chad Staiger, an organic chemist at Sandia, makes the molecule. He said it takes him about 10 days to make between 7-10 grams.
“It’s unfortunately a long synthesis for this molecule,” Staiger said. “More steps equal more time and more money. You usually see five- to six-step syntheses in higher value materials such as pharmaceuticals. In polymers, the cheaper the better for wide scale adoption.”
The team is working to reduce the steps using $100,000 in funding through Sandia’s technology maturation program, which helps ready products for the marketplace.
“My role is to see if there is an easier way to make it at a commercial level,” said postdoc Eric Nagel. “There is nothing like it out there. I am really excited at the possibilities of what this technology can do and the applications that could be associated with this.”
“It’s pretty phenomenal and pretty wide open,” Staiger said.
Dugger agreed: “It really is a sky’s the limit kind of thing.”