Showa Denko Develops Neural Network Models to Predict Mechanical Properties of Aluminum Alloys Accurately
AI and Computational Science Realizes Efficient Optimization of Design Conditions of Aluminum Alloys at High Temperatures
Showa Denko K.K. has developed neural network models to predict mechanical properties of 2000-series aluminum alloys from their design conditions with high accuracy in collaboration with National Institute for Material Science (NIMS) and The University of Tokyo (UTokyo). The developed models enable us to accelerate the process to explore optimal compositions and heat-treatment conditions for aluminum alloys that can maintain strength at high temperatures and shorten development time for aluminum alloys to about half to one-third of that with conventional development method, which was not easy in the past.
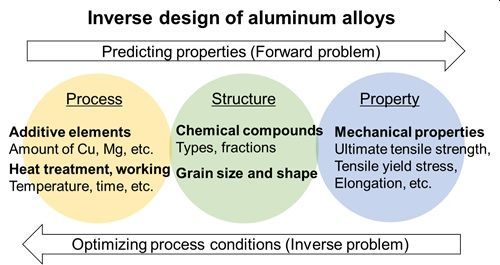
Showa Denko
Aluminum has various applications because it is lighter than iron and easy to work. However, it is usually used as an aluminum alloy containing copper, magnesium and other additive elements because pure aluminum has low strength. The development of aluminum alloys that can maintain sufficient strength for a particular use at high temperatures is desired because conventional aluminum alloys lose strength when their temperature rises to 100 degrees Celsius or higher. However, the mechanical properties of aluminum alloys depend on many process factors, including many kinds of additive elements and heat-treatment conditions. Developing high-performance aluminum alloys usually takes time because designing aluminum alloys requires developers' knowledge-rich experience and repetition of analysis and evaluation.
Aiming to solve these problems, SDK has been taking part in a project under Council for Science, Technology and Innovation (CSTI), Cross-ministerial Strategic Innovation Promotion Program (SIP), "Materials Integration" for Revolutionary Design System of Structural Materials. In this Development, SDK, NIMS, and UTokyo have collaboratively developed a computer system using neural networks, an artificial intelligence (AI) algorithm, to accelerate the development of materials and explore globally for aluminum-alloy designing conditions that realize optimal mechanical properties.
In this development, we focused on 2000-series aluminum alloys, utilized design data of 410 records of aluminum alloys listed in public databases, including the Japan Aluminum Association, and developed neural network models that accurately predict the strength of aluminum alloys at various temperatures ranging from room temperature to high temperature. In addition, we optimized the architecture and parameters of the neural network with Bayesian inference by applying the replica-exchange Monte Carlo Method. As a result, it became possible for us to evaluate aluminum alloy strength and its prediction uncertainty. Moreover, this neural network model can estimate the strengths of aluminum alloys under 10,000 different conditions within 2 seconds. Thus it became possible to evaluate aluminum alloys with various design factors comprehensively in a short time.
Furthermore, we successfully developed "an inverse design tool," which suggests a set of aluminum-alloy design conditions that maximizes the probability of satisfying the desired strength at arbitrary temperature. Thus it enables us to design high-strength aluminum alloys at high temperatures above 200 degrees Celsius.
In its "Long-term Vision for Newly Integrated Company," the Showa Denko Group has announced that it will continue committing itself to make the most of artificial intelligence and computational science, which is the core of its fundamental research activities. We will accelerate our material development programs by applying the results of this Development to our activities to develop various new materials, and provide our customers with solutions for their problems, thereby contributing to the prosperity of society.
Detail of the results of this Development will be presented at the virtual session of the 2021 Materials Research Society Fall Meeting, which will be held from December 6 to 8 in the United States and broadcasted to the world via the Internet.
Other news from the department science
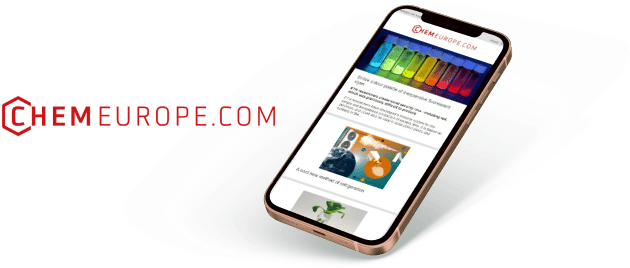
Get the chemical industry in your inbox
By submitting this form you agree that LUMITOS AG will send you the newsletter(s) selected above by email. Your data will not be passed on to third parties. Your data will be stored and processed in accordance with our data protection regulations. LUMITOS may contact you by email for the purpose of advertising or market and opinion surveys. You can revoke your consent at any time without giving reasons to LUMITOS AG, Ernst-Augustin-Str. 2, 12489 Berlin, Germany or by e-mail at revoke@lumitos.com with effect for the future. In addition, each email contains a link to unsubscribe from the corresponding newsletter.