Novas abordagens na produção de pilhas
Do processamento de matérias-primas à reciclagem
A produção de baterias está no centro da política industrial e climática a nível mundial. De facto, a procura de sistemas de armazenamento de energia para aplicações de electromobilidade e estacionárias está a crescer globalmente, tal como a importância de uma produção de baterias eficiente, sustentável e independente a nível regional.
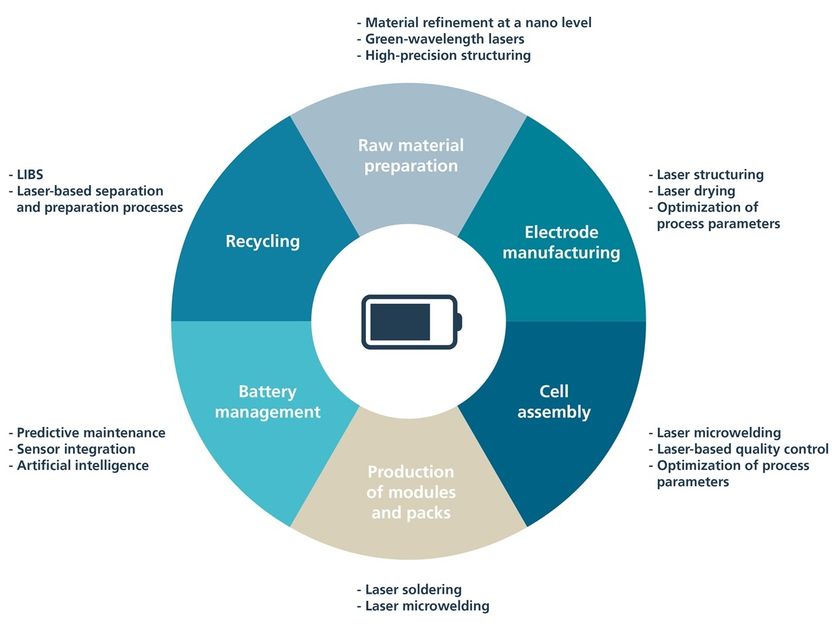
Utilização de lasers e IA para a produção sustentável de pilhas: produção rentável e fiável.
© Fraunhofer ILT, Aachen
Em particular, o ambiente empresarial e regulamentar para a produção de baterias coloca imensos desafios às empresas: Por exemplo, a dependência de matérias-primas como o lítio, o cobalto e o níquel está a causar tensões geopolíticas. Ao mesmo tempo, as cadeias de abastecimento estão a tornar-se cada vez mais frágeis à medida que as crises globais se agravam e os custos de transporte aumentam. A Europa vê-se, por isso, confrontada com a tarefa de construir uma cadeia de valor resiliente que inclua a extração de matérias-primas, a transformação posterior e a reciclagem - afinal, as baterias usadas são o recurso alemão mais abundante de lítio. Além disso, os processos de produção têm de ser adaptados de forma flexível a novos modelos de baterias, como as baterias de estado sólido ou de iões de sódio, a fim de garantir os investimentos nas mesmas.
Tendo em conta estes desafios, é evidente que o futuro da produção de baterias na Europa só pode ser assegurado através da utilização de tecnologias de ponta. A tecnologia laser, em particular, oferece soluções para satisfazer os principais requisitos - eficiência, precisão e sustentabilidade. A produção competitiva e sustentável de baterias na Europa é dificilmente concebível sem processos laser inovadores, seja no processamento de materiais, na produção de eléctrodos ou na reciclagem.
Processamento de matérias-primas e refinamento de materiais: a base para a produção sustentável de baterias
Materiais como o lítio e o níquel continuam a ser componentes das actuais células de bateria. As suas propriedades químicas e físicas tornam possíveis densidades de energia elevadas e tempos de vida longos, mas a sua extração e processamento colocam questões complexas.
No entanto, as tecnologias de baterias estão a desenvolver-se rapidamente, com a indústria a tentar minimizar a utilização de matérias-primas raras e dispendiosas. O fabricante chinês de baterias CATL apresentou em 2021 uma bateria de iões de sódio que dispensa completamente o lítio e o cobalto. Em abril de 2024, a CATL lançou uma bateria de fosfato de ferro e lítio (LFP) sem cobalto que pode alimentar um automóvel durante mais de 1.000 quilómetros com uma única carga. Em apenas dez minutos, pode carregar energia suficiente para 600 quilómetros, o que corresponde a uma velocidade de carregamento de um quilómetro por segundo.
A Toyota planeia utilizar baterias de estado sólido em veículos híbridos a partir de 2025. A Nissan colocou em funcionamento no Japão um protótipo de uma fábrica de produção de baterias de estado sólido laminadas. A Panasonic apresentou uma bateria de estado sólido para drones. A VW e a Mercedes, a Ford e a BMW estão prestes a introduzir baterias de estado sólido ou estabeleceram parcerias estratégicas.
Um ponto de partida fundamental para as novas tecnologias de baterias é o refinamento dos materiais a nível nano; aqui, as matérias-primas são especificamente processadas e funcionalizadas para maximizar o seu desempenho nas baterias. É isto que o Departamento de Tecnologia de Superfícies e Ablação do Instituto Fraunhofer de Tecnologia Laser está a examinar. Com as modernas tecnologias laser, é possível intervir com precisão na estrutura do material e, ao mesmo tempo, minimizar o consumo de recursos.
Um outro exemplo da utilização bem sucedida das tecnologias laser é a colaboração entre o Fraunhofer ILT, a cátedra de tecnologia laser LLT da Universidade RWTH Aachen, a TRUMPF e o German Electron Synchrotron DESY. Utilizando os raios X de um acelerador de partículas, os engenheiros conseguiram obter uma visão mais profunda dos processos de soldadura a laser. Mostraram que a utilização de lasers com um comprimento de onda verde melhora a utilização do material e reduz o desperdício. As suas descobertas não só oferecem vantagens tecnológicas, como também contribuem para uma produção mais sustentável.
"Estes projectos mostram que a tecnologia laser inovadora pode não só ultrapassar os desafios do processamento de matérias-primas, mas também permitir uma produção sustentável e competitiva de baterias na Europa", explica o Dr. Alexander Olowinsky, responsável pelo departamento de Junção e Corte do Fraunhofer ILT.
Produção de eléctrodos: inovações para uma produção sustentável
As folhas condutoras de corrente (cobre ou alumínio) têm de ser revestidas com os materiais dos eléctrodos para o ânodo e cátodo, e subsequentemente secas - passos cruciais que influenciam tanto a densidade energética como o ciclo de vida das baterias. No entanto, os processos de secagem convencionais baseados em fornos de convecção consomem uma quantidade considerável de energia e requerem uma grande quantidade de espaço, o que limita a sustentabilidade e a eficiência da produção de baterias.
O projeto IDEEL (Implementation of Laser Drying Processes for Economical & Ecological Lithium- Ion Battery Production), financiado pelo Ministério Federal Alemão da Educação e Investigação, mostra como a secagem a laser resolve estes desafios: No projeto, os ânodos e cátodos foram secos num processo rolo a rolo pela primeira vez, utilizando um laser de díodo de alta potência. Este método reduz significativamente o consumo de energia, duplica a velocidade de secagem e reduz para metade o espaço necessário.
"A secagem a laser não só permite um controlo mais eficiente do processo, como também ajuda a melhorar significativamente a pegada de carbono da produção de baterias", explica o Dr. Samuel Moritz Fink, gestor do grupo de Processamento de Película Fina do Fraunhofer ILT. Juntamente com os parceiros do projeto, Fink e a sua equipa desenvolveram um módulo de secagem a laser com ótica adaptada e monitorização do processo para garantir uma secagem uniforme. Esta abordagem também oferece flexibilidade: Os fornos de convecção existentes podem ser adaptados com a tecnologia laser, facilitando a implementação do processo inovador nas linhas de produção existentes.
Num outro projeto de investigação, o Fraunhofer ILT está a utilizar uma ótica de feixes múltiplos especialmente desenvolvida. Este conjunto ótico divide o feixe laser em vários feixes parciais que processam simultaneamente uma fita de 250 milímetros de largura de um ânodo de bateria de iões de lítio. Esta estruturação de alta precisão aumenta a densidade energética e melhora a capacidade de carregamento rápido.
A produção de eléctrodos também beneficia da integração da inteligência artificial no processo de fabrico. Os investigadores do Fraunhofer ILT estão atualmente a investigar a forma como os sistemas apoiados por IA podem ser utilizados para otimizar os parâmetros do processo. Estes sistemas podem não só aumentar ainda mais a qualidade e a produtividade, mas também lançar as bases para a produção autónoma.
Montagem de células: precisão e eficiência através de tecnologias inovadoras
Para além da secagem dos eléctrodos, a união precisa dos materiais dos eléctrodos também desempenha um papel central no desempenho e fiabilidade das baterias. A micro-soldadura a laser estabeleceu-se como uma tecnologia-chave neste domínio, uma vez que pode unir materiais como o cobre e o alumínio, essenciais para os eléctrodos das baterias, sem entrar em contacto com eles e com elevada precisão. Graças à baixa carga térmica, a química sensível da célula permanece intacta, enquanto a condutividade eléctrica é optimizada através da redução da resistência de contacto. A micro-soldadura a laser oferece uma combinação de flexibilidade e eficiência que os processos de soldadura tradicionais não conseguem igualar.
Os requisitos para a micro-soldadura a laser variam consoante o formato da célula, uma vez que cada tipo de célula apresenta desafios específicos no que diz respeito ao contacto. As células cilíndricas requerem uma profundidade de soldadura precisa para garantir a condutividade eléctrica, por um lado, e para evitar danos devido a sobreaquecimento, por outro. O contacto com o pólo negativo coloca desafios particulares, uma vez que o calor excessivo pode danificar o vedante de polímero sensível, o que pode resultar em fugas de eletrólito. No caso das células tipo "pouch", que se caracterizam pela sua conceção flexível e pela sua elevada densidade energética, é necessário evitar a soldadura através do revestimento de película sensível.
Um desenvolvimento promissor na montagem de células pode ser encontrado no projeto XProLas, que a TRUMPF está a realizar em colaboração com a Fraunhofer ILT e outros parceiros. O objetivo é desenvolver fontes de raios X compactas, acionadas por laser, que permitam testes de qualidade no local, diretamente nas instalações do fabricante, em vez de utilizar grandes aceleradores de partículas, como acontecia anteriormente. Esta nova tecnologia possibilita a análise de células de bateria em tempo real, permitindo monitorizar com precisão os processos de carga e descarga e a qualidade do material. Este método abre novas possibilidades, especialmente quando o material do cátodo precisa de ser examinado; o material determina o desempenho e a durabilidade da bateria. "Ao utilizar fontes de raios X brilhantes, podemos detetar impurezas e defeitos do material numa fase inicial e, assim, reduzir significativamente os tempos de desenvolvimento", explica o Engenheiro Hans-Dieter Hoffmann, diretor do Departamento de Lasers e Sistemas Ópticos do Fraunhofer ILT.
Também aqui, a integração da inteligência artificial abre um potencial adicional: Os sistemas apoiados por IA podem monitorizar e ajustar os parâmetros do processo em tempo real. Com isso, os desvios podem ser detectados e corrigidos numa fase inicial, criando a base para a produção autónoma. A visão de uma produção "à primeira", em que todos os componentes são montados sem erros na primeira execução, está, portanto, ao nosso alcance.
Produção de módulos e embalagens: eficiência e precisão através de tecnologias laser
As células individuais são depois ligadas para formar módulos ou pacotes. A precisão desempenha um papel decisivo ao nível dos módulos, em particular porque é necessário integrar vários cordões de soldadura sem aumentar a carga térmica nas células sensíveis. Os processos laser, como a micro-soldadura, permitem aos utilizadores adaptar os seus processos a estes requisitos de forma personalizada.
Uma das principais inovações do Fraunhofer ILT é o desenvolvimento de processos que podem ser utilizados para unir com segurança e precisão o alumínio e o cobre - dois materiais com propriedades físicas muito diferentes. Utilizando a mais moderna orientação de feixes de laser, os engenheiros do instituto podem controlar a profundidade da soldadura de modo a não danificar células sensíveis.
"Esta tecnologia é essencial para a produção de módulos e pacotes que têm de funcionar de forma fiável em condições extremas, como correntes elevadas e cargas térmicas", explica Olowinsky. Um exemplo disto é a soldadura a laser de células cilíndricas de grandes dimensões, que o instituto sediado em Aachen tem continuado a desenvolver em conjunto com parceiros como a EAS Batteries GmbH. Neste caso, estão a prestar atenção à criação de uma interconexão estável e duradoura entre as células para garantir uma longa vida útil e baixas taxas de falha.
Para além da soldadura a laser, a soldadura a laser também se estabeleceu, especialmente para unir componentes sensíveis ao calor. Este processo funciona a temperaturas mais baixas do que os métodos de soldadura tradicionais e, assim, protege a eletrónica sensível dentro dos módulos, tornando não só as baterias mais fiáveis, mas também a produção mais eficiente em termos energéticos.
Gestão de baterias e integração de sensores: inteligência para sistemas de baterias à prova de futuro
A gestão de baterias é um dos principais desafios dos modernos sistemas de armazenamento de energia. A segurança, a longevidade e o desempenho das baterias dependem em grande parte dela - e não menos importante a aceitação da electromobilidade. Os avanços na integração de sensores e a utilização da IA oferecem oportunidades transformadoras para satisfazer estes requisitos.
Tradicionalmente, as baterias são monitorizadas a um nível macroscópico, mas isso apenas oferece uma visão limitada dos processos complexos no interior das células. É aqui que a integração da tecnologia de sensores durante a produção oferece novas possibilidades. Os investigadores do Fraunhofer ILT imprimem sensores diretamente nos componentes, ou até integram os dispositivos de medição inteligentes nos mesmos. Estes sensores permitem uma monitorização em tempo real, como a medição de temperaturas, forças ou mesmo alterações químicas nas baterias durante a sua utilização.
"Com os sensores fabricados aditivamente, podemos monitorizar continuamente o estado dos módulos de bateria e reagir a potenciais defeitos numa fase inicial", explica Samuel Fink. Estes sensores têm apenas alguns micrómetros de espessura, são precisos e resistentes ao stress mecânico e térmico, o que os torna ideais para utilização na bateria e nos módulos de bateria. A sua capacidade de fornecer dados contínuos permite a manutenção preditiva, que detecta potenciais defeitos antes de estes ocorrerem.
No entanto, a integração da tecnologia de sensores, por si só, não é suficiente para implementar a manutenção preditiva. Os sensores podem detetar alterações na química das células, enquanto os algoritmos de IA analisam estes dados e fazem previsões sobre a vida útil das células. Os investigadores do Departamento de Ciência de Dados e Tecnologia de Medição do Fraunhofer ILT estão a desenvolver esses algoritmos apoiados por IA que analisam grandes quantidades de dados de sensores em tempo real. Estes sistemas também permitem adaptar dinamicamente os processos, por exemplo, optimizando os perfis de temperatura durante a montagem das células ou ajustando os parâmetros de soldadura a laser.
Reciclagem e reutilização: o caminho para uma economia circular na tecnologia de baterias
Juntamente com o boom da tecnologia de baterias, a necessidade de estratégias sustentáveis para recuperar matérias-primas valiosas também está a crescer. Uma economia circular efectiva é essencial para reduzir a dependência de matérias-primas primárias, minimizando simultaneamente o impacto ambiental da produção de baterias.
No projeto da UE ADIR, o Fraunhofer ILT está a trabalhar com oito parceiros de projeto de três países para desenvolver um conceito de reciclagem sustentável para dispositivos electrónicos. O projeto ACROBAT visa desenvolver um plano de reciclagem de baterias de fosfato de ferro e lítio antes de estas entrarem no mercado em grande escala. O objetivo do projeto é recuperar mais de 90 por cento dos materiais críticos. Juntamente com parceiros como a Accurec Recycling, o Fraunhofer ILT está a trabalhar em métodos inovadores de separação e processamento que sejam ecológica e economicamente sustentáveis. Os especialistas em laser de Aachen estão a desenvolver um método de caraterização em linha para avaliar com precisão a qualidade do material ativo.
Com o seu próprio processo de espetroscopia de rutura induzida por laser (LIBS), o instituto pode identificar e separar com precisão composições complexas de materiais. Os investigadores pretendem adaptar esta tecnologia à reciclagem de baterias usadas para melhorar ainda mais a recuperação de metais como o cobalto e o tântalo. Também aqui, a IA pode ser integrada para analisar as grandes quantidades de dados das medições a laser e otimizar o processo em tempo real. Esta monitorização apoiada por IA permite o ajuste dinâmico dos parâmetros de reciclagem, o que reduz os resíduos e aumenta a qualidade das matérias-primas recicladas.
Conclusão e perspectivas
A produção de baterias está no centro da transição da electromobilidade e, por conseguinte, no centro das inovações que combinam eficiência, sustentabilidade e excelência tecnológica. As tecnologias e desenvolvimentos apresentados ao longo da cadeia de produção mostram como os processos laser de ponta podem abrir caminho para uma indústria de baterias sustentável e competitiva: desde a preparação de matérias-primas e produção de eléctrodos até à montagem e reciclagem de células. Ao mesmo tempo, os sistemas de análise e controlo apoiados pela IA criam uma nova dimensão de controlo de processos que melhora a qualidade e a sustentabilidade da produção e reduz ainda mais os custos de produção.
No futuro, os circuitos de controlo apoiados pela IA poderão permitir uma produção autónoma em que os processos se adaptam às condições em mudança em tempo real. Além disso, as fontes de raios X acionadas por laser e as tecnologias de caraterização em linha abrem novas possibilidades para a garantia de qualidade e a análise de materiais.
Observação: Este artigo foi traduzido usando um sistema de computador sem intervenção humana. A LUMITOS oferece essas traduções automáticas para apresentar uma gama mais ampla de notícias atuais. Como este artigo foi traduzido com tradução automática, é possível que contenha erros de vocabulário, sintaxe ou gramática. O artigo original em Inglês pode ser encontrado aqui.