Autoclaves at a Glance: Products, Function and Applications
Autoclaves are hermetically sealed devices used to sterilize laboratory equipment and medical instruments and to heat treat industrial materials using high pressure and temperature. On this page you will find an overview of products from various manufacturers.
You are looking for general information about this topic? Our autoclave guide gives you all the info you need on how they work and what they're used for.
Autoclaves at a Glance: Products, Function and Applications
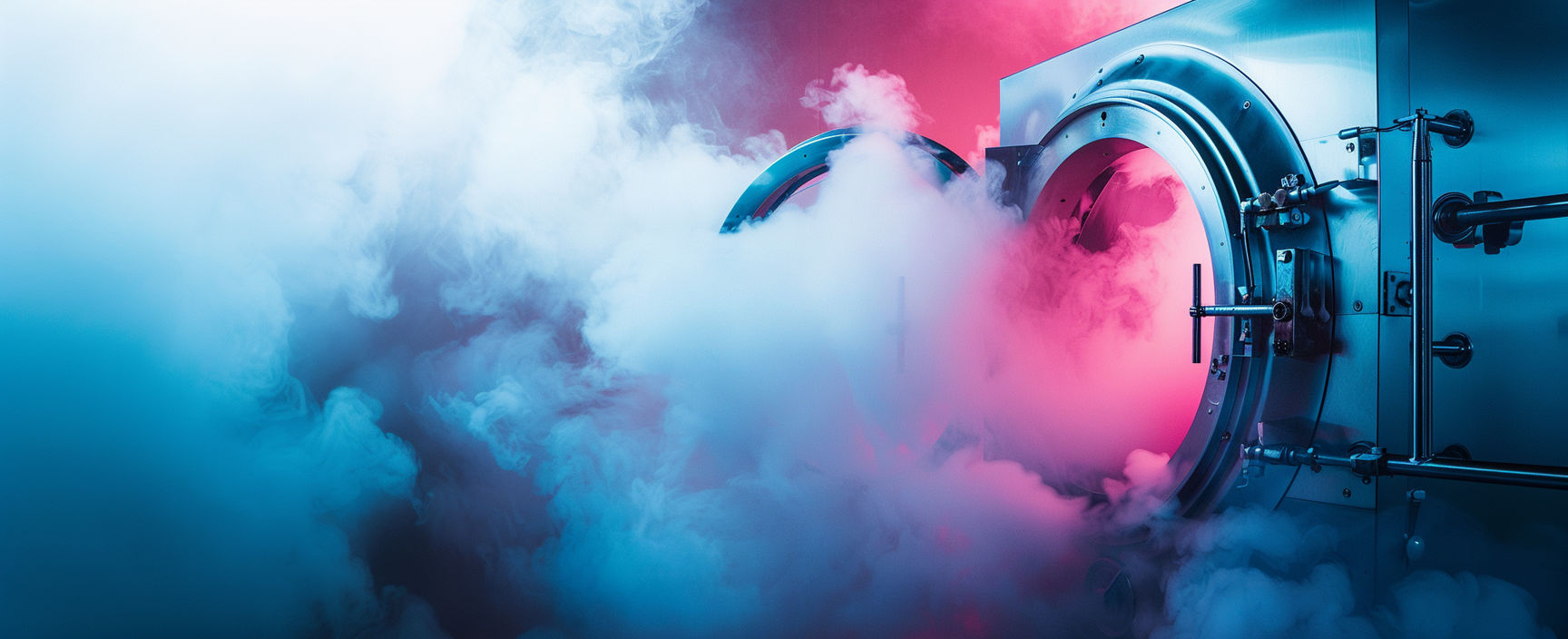
Autoclaves are hermetically sealed devices used to sterilize laboratory equipment and medical instruments and to heat treat industrial materials using high pressure and temperature. On this page you will find an overview of products from various manufacturers.
You are looking for general information about this topic? Our autoclave guide gives you all the info you need on how they work and what they're used for.
Autoclaves at a glance
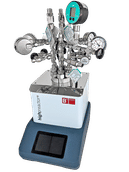
Hochdruck-Parallelreaktor BRHS mit BT-25 by Berghof
Pressure reactors for screening tests up to 300°C and 200 bar incl. temperature and pressure measure
Screening tests & parallel syntheses - Operating up to 6 mini high-pressure reactors simultaneously
Highest performance - operate 6 high-pressure reactors with 25 mL, 200 bar, 300°C simultaneously ✓ All-in-one - combines heating, control, logging and stirring in a clear, space-saving design ✓ Screening/parallel synthesis - same reaction conditions guaranteed for all high-pressure reactors ✓
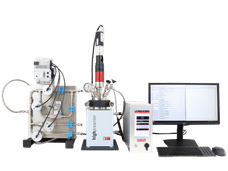
Fully automated hydrogenation reactor BR/H2 by Berghof
Fully automated hydrogenation reactor: Precise and safe hydrogenation at the flick of a switch
Optimised process control with leakage tests, gas consumption measurement and modular expandability
Fully automatic control - purging, gas exchange and post-dosing of reactive gases possible ✓ Safety and handling - safe, automatic process control, leakage tests, with quick-release fastener ✓ Reproducibility - recipe operation with SOPs, seamless data acquisition, gas consumption measurement ✓
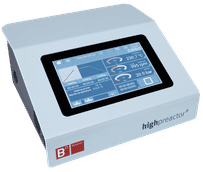
BRC - Berghof Reactor Controller by Berghof
BRC - complete package for data acquisition, storage and control of all process parameters
Touch controllers are easy to use and provide quick access to all important functions
Intuitive operation - user-friendly user interface via 7" touchscreen with swipe function ✓ Auto-tuning enables optimum process control through specifically optimized PID parameters ✓ Numerous interfaces enable small systems to be controlled fully automatically or manually ✓
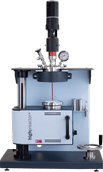
Berghof Reaktortechnologie - Hoch- und Niederdruckreaktoren, Druckbehälter und metallfreie Reaktoren by Berghof
Safe high- and low-pressure systems for aggressive media
Corrosion-resistant reactors with PTFE lining - individually configurable
PTFE lining for effective corrosion protection allows the use of highly corrosive media ✓ Flexibility and individuality - The modularly designed reactors are individually configured ✓ Easy handling - You simply open/close the quick-release fastener by hand without tools ✓
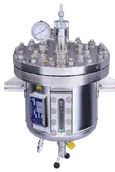
JUCHHEIM LabClave: Druckreaktoren by JUCHHEIM Laborgeräte
Customized stainless steel reactors - configured for your needs
Perfect for extraction, digestion, hydrolysis, hydrogenation or synthesis
Suitable for vacuum to high-pressure processes ✓ Made of stainless steel, Hastelloy. PTFE-coated or special alloys ✓ Optional accessories: agitator, container lift, sensors, etc ✓
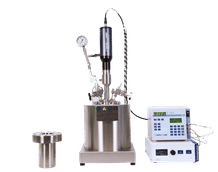
BUCHI NOVOCLAVE by C3 Prozess- und Analysentechnik
Extreme performance for demanding laboratory applications - Discover the new high-pressure autoclave!
The new Büchi novoclave laboratory stirred autoclave offers extreme performance with operating conditions of up to 500 bar and 500°C. The vessels are
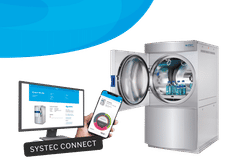
Systec H-Series by Systec
Safe, reproducible and validatable sterilization of liquids, solids and waste
Autoclaves with 65-1580 liters usable space, flexibly expandable for various applications
Short and efficient process times, newly developed touch screen control, CFR 21 Part 11 solution ✓ Various options, accessories and programs (such as glass test, rubber closure test) available ✓ Monitoring in real time via PC/App with Systec Connect Documentation Software ✓
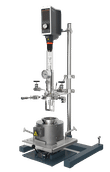
HiClave by JUCHHEIM Laborgeräte
Modular high-pressure reactors - flexible to configure
Ideal for hydrogenation, oxidation, carbonylation, polymerization
High-pressure stirred-tank system ✓ Pressures from 0 to 400 bar ✓ Temperatures from -200 to +400 °C ✓ Modular design ✓ Long-lasting & rugged ✓
Choose autoclaves by product category
Select autoclaves for your application
Buy autoclaves for the lab or the production process
Related product categories
Autoclave guide: Everything you need to know, clearly explained
Autoclaves are highly specialized devices that are indispensable in the sterilization and high-pressure treatment of materials. They are widely used in laboratories, medical facilities, industry and other areas where sterility and precise treatment of materials are crucial. By using saturated steam under high pressure, autoclaves can not only kill microorganisms, but also influence the physical and chemical properties of materials.
Autoclaves: definition, how they work, history
An autoclave is a hermetically sealed pressure vessel that is used to carry out sterilization and high-pressure processes. Sterilization is carried out using saturated steam, which is heated to temperatures of 121 to 134 degrees Celsius and is under a pressure of around 2 to 3 bar. This process leads to the denaturation of proteins and the destruction of microorganisms, including heat-resistant spores. Autoclaves can vary in design and size depending on the application, from small tabletop units to large industrial systems.
Historical background
The development of the autoclave goes back to Denis Papin, who invented the first pressure vessel, also known as “Papin's pot”, in 1679. This early model laid the foundation for modern autoclaves. Over the centuries, the technologies have been further refined and adapted to meet the increasing demands of science, medicine and industry. Today, autoclaves are available in a variety of designs and for a wide range of applications.
What types of autoclaves are there?
Laboratory autoclaves
These autoclaves are designed for the specific needs of research laboratories and scientific institutions. They are mainly used for the sterilization of glassware, culture media, laboratory waste and other laboratory equipment. Laboratory autoclaves often have to meet high standards of precision and reliability to ensure a contamination-free environment.
Industrial autoclaves
In industrial applications, autoclaves are used to sterilize and treat materials such as composites, building materials, plastics and metals. These autoclaves often have to handle large volumes and complex processes. They are characterized by their versatility and efficiency and are designed to meet the specific requirements of industrial applications.
Medical autoclaves
In medical facilities, autoclaves are crucial for the sterilization of surgical instruments, implants, textiles and other medical devices. These devices must meet strict medical standards and offer a high level of reliability and sterilization safety.
Special autoclaves
In certain industries, such as the food industry, the production of building materials and the manufacture of fiber composites, special autoclaves are used that are tailored to the specific requirements of these applications. These autoclaves often have to meet special pressure and temperature profiles as well as specific safety requirements. They are designed to treat and preserve materials or to impart specific physical properties.
Important criteria when selecting an autoclave
Volume and size
When selecting an autoclave, the volume to be sterilized plays a decisive role. Smaller benchtop models are ideal for laboratories with limited space and low sterilization requirements, while larger floor models are suitable for industrial applications with high throughput. An autoclave should offer sufficient capacity to meet the specific requirements of the application without the need for frequent loading and unloading.
Pressure and temperature requirements
Different materials and applications require specific pressure and temperature settings. An autoclave should be able to precisely control these parameters to ensure optimal sterilization and material treatment. High-pressure autoclaves are suitable for treating composite materials, for example, while low-pressure models are used in the food industry.
Additional functions and options
Modern autoclaves offer a variety of additional functions that make operation safer and more efficient. These include quick-release locks, automatic door locks, programmable controls and special safety mechanisms. The modularity of the devices makes it possible to add additional functions such as data logging, remote monitoring and special sterilization cycles to meet specific requirements.
In which areas are autoclaves used?
Use of autoclaves for sterilization processes
There are various sterilization processes used in autoclaves, including steam sterilization, vacuum processes and dry steam processes. The choice of process depends on the materials to be sterilized and the specific requirements. Steam sterilization is the most widely used, as it is effective, fast and reliable. The vacuum process, also known as a pre-vacuum autoclave, is used for materials that require more thorough sterilization by removing air from the chamber before steam is introduced. On average, a sterilization cycle takes between 30 and 60 minutes, depending on the type and amount of material to be sterilized.
Autoclaves in medicine
- Sterilization of medical instruments: Autoclaves are used in hospitals and clinics to sterilize surgical instruments, implants and other medical devices. The high temperature and pressure of the steam kills all microorganisms, making the instruments safe to use.
- Sterilization of waste material: Medical facilities also use autoclaves to sterilize biological waste material before it is disposed of. This reduces the risk of infection and contamination. Strict safety measures must be observed when operating an autoclave to prevent accidents and injuries. These include staff training, regular maintenance of the device and compliance with legal regulations.
Autoclaves in research
- Sterilization of laboratory equipment: In research laboratories, autoclaves are essential for sterilizing glassware, culture media and other laboratory utensils. Sterile conditions are crucial for the accuracy of experiments and research results.
- Preparation of samples: Autoclaves are used to prepare samples for experiments. Sterilization can eliminate unwanted microorganisms that could falsify research results.
Autoclaves in the food industry
- Preservation of food: Autoclaves are used in the food industry to preserve food. By applying steam under high pressure, food can be sterilized safely and effectively, which extends its shelf life.
- Production of convenience food: Autoclaves are used in the production of ready meals to pasteurize the products, making them safe for the consumer. This reduces the risk of food-borne illnesses.
Autoclaves in the industry
- Production of composite materials: Autoclaves play a crucial role in the production of fiber composites such as carbon fiber and fiberglass. They enable materials to be cured under controlled pressure and temperature conditions, resulting in improved material properties.
- Treatment of building materials: Autoclaves are also used in the building materials industry to treat materials such as bricks and concrete. The use of steam and pressure improves the physical properties of building materials, increasing their strength and durability.
Autoclaves in the pharmaceutical industry
- Sterilization of pharmaceutical products: In the pharmaceutical industry, autoclaves are used to sterilize medicines, vaccines and other pharmaceutical products. This ensures that the products are free from microorganisms and can be used safely.
- Production of medical packaging: Autoclaves are also used to sterilize packaging materials for medical products. This prevents contamination of the products during storage and transportation.
Sterilization process in an autoclave
The sterilization process in an autoclave comprises several sub-steps that ensure that the materials to be sterilized are completely free of microorganisms. Here is a detailed description of the entire process:
1. Preparation
Cleaning: Before the materials enter the autoclave, they should be thoroughly cleaned to remove gross contamination. This can be done by manual scrubbing or using special cleaning machines.
Packaging: The items to be sterilized are packed in special sterilization packaging such as autoclave paper, sterilization pouches or containers. This packaging must be steam-permeable to ensure effective sterilization.
Labeling: Each package should be labeled with information such as contents, sterilization date and person responsible to ensure traceability.
2. Loading
Proper placement: The packaged materials are placed in the autoclave. It is important to place the materials so that the steam can circulate freely. Overloading should be avoided to ensure even steam penetration.
Check: Check that the autoclave is correctly loaded and that all safety precautions have been taken.
3. Closing and locking
Close the door: Close the autoclave door and lock it properly. Modern autoclaves have automatic locking systems that close the door securely.
4. Vacuum phase (optional, for pre-vacuum autoclaves)
Air removal: In pre-vacuum autoclaves, the air is removed from the chamber to ensure complete steam penetration. This is done by several vacuum pulses followed by steam inlets.
5. Heating phase
Steam generation: The autoclave generates saturated steam, which is directed into the chamber. The steam displaces the remaining air and increases the temperature and pressure in the chamber.
Temperature attainment: The temperature is brought to the desired level (typically 121 to 134 degrees Celsius).
6. Sterilization phase
Maintaining the temperature: The chamber maintains the set temperature and pressure for a predetermined time (usually 15-30 minutes). During this phase, the steam penetrates the packaging and materials and kills all microorganisms, including heat-resistant spores.
7. Cooling and drying phase
Pressure release: After the sterilization phase, the pressure in the chamber is slowly released to allow safe opening.
Drying (optional): In some cases, the chamber is dried to ensure that the materials are dry after the sterilization process. This is done by vacuum or heating.
8. Unloading
Opening the door: After the pressure has been completely released, the door of the autoclave can be opened. Care must be taken here to avoid burns from hot steam.
Removing the materials: The sterilized materials are removed. It is important not to touch them immediately as they may still be hot.
9. Storage
Cooling: Allow the sterilized materials to cool completely before storing or using them.
Sterile storage: The sterilized materials should be stored in a clean, sterile area to avoid recontamination.
10. Documentation
Record keeping: The sterilization process should be documented. This includes details of the materials sterilized, the sterilization cycle, the date and the person responsible. These records are important for traceability and quality assurance.
Care and maintenance of autoclaves
Regular maintenance
Regular maintenance of an autoclave includes checking seals, valves and heating elements. Careful maintenance extends the service life of the device and ensures that it is always ready for use. Autoclaves should be cleaned regularly to avoid deposits and contamination.
Safety and functional checks
Regular safety and functional checks are essential to ensure the proper functioning of an autoclave. Legal requirements and internal standards must be strictly adhered to. Safety measures such as the handling of high-pressure steam and compliance with legal regulations are essential.
Troubleshooting and support
Common problems such as pressure loss or insufficient sterilization can be solved through targeted troubleshooting. In the event of an error message, the operating instructions should be consulted first and simple troubleshooting carried out. For more complex problems, the manufacturer's technical support is available.
What does an autoclave cost?
When purchasing an autoclave, the investment costs should be evaluated in relation to the longevity and benefits of the device. High-quality autoclaves often offer better performance and a longer service life.
Benchtop autoclaves, which are often used in dental practices or small laboratories, range in price from 2,000 to 5,000 USD for entry-level models. Higher-quality and specialized models with additional functions such as pre-vacuum, advanced controls or higher capacities cost between 5,000 and 15,000 USD.
Larger floor-standing autoclaves, which are often used in larger clinics or research laboratories, range in price from 10,000 to 30,000 USD for mid-range models. Models for more extensive applications can cost between 30,000 and 50,000 USD or more.
Industrial autoclaves, which are used in food processing, the production of composite materials or other industrial applications, are priced between 50,000 and 100,000 USD. Highly specialized autoclaves with very large capacities or special technical requirements can be significantly more expensive, often in the range of 100,000 to 500,000 USD or more.
Research facilities and universities sometimes require customized autoclaves that have to meet special requirements. The cost of such specialized equipment varies widely, but often starts at around 50,000 USD and can go well beyond that.
Operating costs
The running costs of operating an autoclave include energy, water and consumables. These costs should be taken into account when planning the budget. Maintenance costs vary depending on the model and frequency of use.
Final summary
Autoclaves are indispensable devices for sterilization and high-pressure treatment in various industries. When selecting an autoclave, volume, pressure and temperature requirements as well as additional functions should be taken into account. Regular maintenance and safety checks are crucial for the longevity and functionality of the equipment. A careful cost-benefit analysis will help you decide on the right model.
Haven't found the right product yet?
The chemeurope.com Product Search
Start your targeted search now with a wide selection of filter options. Here you can easily find the right product for your search, including manufacturer information and options for requesting a quote or downloading the corresponding brochure.