Nanoscale coating protect products - and the economy
UWM researcher creates smart coatings that fortify materials
Put steel under a powerful microscope, revealing its microstructure, and prepare to be surprised. Known for its strength, the metal will appear pitted and pocked. "It is intrinsic to the material," says Carolyn Aita, a Wisconsin Distinguished Professor at the University of Wisconsin–Milwaukee (UWM). "A pit can begin to develop from a physiochemical defect in the steel itself."
The pitting is cause for concern for industry because it can progress and lead to corrosion. But Aita's research can help. In her lab at the College of Engineering and Applied Science, she has developed a host of coatings that heal shallow pits and fractures on almost any material – from metal to glass to silicon. The coatings also prevent further degradation. "My coatings are designed to work in adverse environments, such as in salt spray, oil, and high humidity," says Aita. "We design them to address whatever causes damage to the substrate."
In her current work, which is funded by a Rockwell Catalyst Grant from the UWM Research Foundation, Aita and four graduate students are creating new coatings that can withstand the corrosion that occurs in metals in an industrial setting. The work is valuable to its sponsor, Rockwell Automation .
In addition to natural imperfections, materials like stainless steel are susceptible to the environments in which they are used, says Christopher Genthe, a materials project engineer in Rockwell's Chemistry & Materials Engineering group who also is one of Aita's graduate students.
Rockwell's materials engineers are interested in protecting the metal parts the company manufactures – like enclosures that house electronics, for example – from high humidity, temperature and industrial contaminants.
Aita's nanolaminate coating is applied to the metal surface in ultra-thin layers, and together they adjust in response to a wide range of adverse conditions. The tiny crystals in the layers transform to surround and contain the defect.
Achieving the right characteristics for these protective coatings depends on choosing the right combination of elements and manipulating them to act in a precise way. For the Rockwell project, the team in Aita's Advanced Coatings Experimental Laboratory (AceLab) uses hafnia, zirconia and alumina in their smart ceramic coatings for metal. "We engineer these to behave differently than they would in a ceramic with a larger microstructure," says Elizabeth Hoppe, the AceLab manager and a Ph.D. student of Aita's. "We grow the film in layers so that the growth of tiny crystals within a layer is stopped at a particular size, which allows us to control their behavior."
It's the arrangements of the molecules in the tiny crystals embedded in a layer that ultimately determine film characteristics, says Aita. Because they work at the nanoscale, the job of actually applying the thin films falls on "Dorothy," a large "sputter deposition" apparatus in the AceLab. In sputter deposition, energetic ions formed from a vapor bombard a disk, or "target," made of a particular element, sending energetic atoms from it scattering like billiard balls in a game of pool. Those atoms then coat the substrate in ultra-thin layers.
Most read news
Other news from the department science
These products might interest you
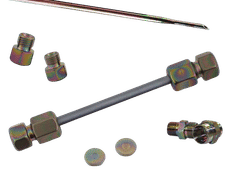
Dursan by SilcoTek
Innovative coating revolutionizes LC analysis
Stainless steel components with the performance of PEEK - inert, robust and cost-effective
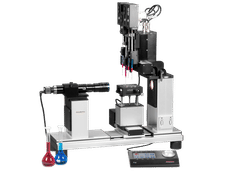
OCA 200 by DataPhysics
Using contact angle meter to comprehensively characterise wetting behaviour, solids, and liquids
With its intuitive software and as a modular system, the OCA 200 answers to all customers’ needs
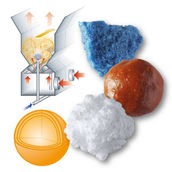
Tailor-made products for specific applications by IPC Process Center
Granulates and pellets - we develop and manufacture the perfect solution for you
Agglomeration of powders, pelletising of powders and fluids, coating with melts and polymers
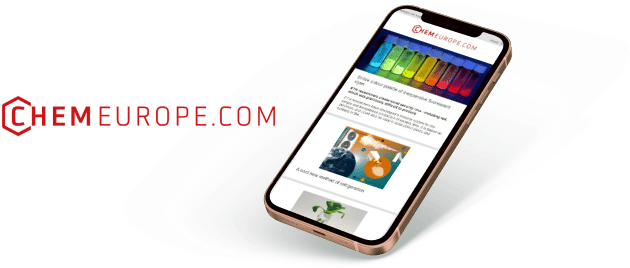
Get the chemical industry in your inbox
By submitting this form you agree that LUMITOS AG will send you the newsletter(s) selected above by email. Your data will not be passed on to third parties. Your data will be stored and processed in accordance with our data protection regulations. LUMITOS may contact you by email for the purpose of advertising or market and opinion surveys. You can revoke your consent at any time without giving reasons to LUMITOS AG, Ernst-Augustin-Str. 2, 12489 Berlin, Germany or by e-mail at revoke@lumitos.com with effect for the future. In addition, each email contains a link to unsubscribe from the corresponding newsletter.