Fine print: New technique allows fast printing of microscopic electronics
A new technique for printing extraordinarily thin lines quickly over wide areas could lead to larger, less expensive and more versatile electronic displays as well new medical devices, sensors and other technologies. Solving a fundamental and long-standing quandary, chemical engineers at Princeton developed a method for shooting stable jets of electrically charged liquids from a wide nozzle. The technique, which produced lines just 100 nanometers wide, offers at least 10 times better resolution than ink-jet printing and far more speed and ease than conventional nanotechnology.
"It is a liquid delivery system on a micro scale," said Ilhan Aksay, professor of chemical engineering. "And it becomes a true writing technology."
Aksay and graduate student Sibel Korkut published the results in Physical Review Letters. The paper also includes as a co-author Dudley Saville, a chemical engineering professor who initiated the project but died in 2006. The research was funded by grants from the Army Research Office, the National Science Foundation and NASA.
The key to the process is something called an "electrohydrodynamic (EHD) jet" - a stream of liquid forced from a nozzle by a very strong electric field. Such jets were first investigated in 1917 and are now commonly used in a variety of industrial processes. However, one of the main features of EHD jets is that the stream of liquid becomes unstable soon after it leaves the nozzle and either whips around uncontrollably or breaks up into fine liquid drops. Engineers have used these effects to their advantage in spinning fibers and in industrial electrospray painting, but the reason for the whipping instability, and thus any hope of stopping it, has been a long-standing problem.
In the early part of this decade, two researchers working independently - Princeton graduate student Hak Poon and Cornell University physicist Harold Craighead - found that the jet was stable for a very short distance after leaving the nozzle, but the result was still not practical and the reasons were still elusive. "To understand how to control the jet in any engineering application we had to understand why this was happening," Aksay said.
Korkut took up the challenge and worked for nearly six years to nail down the mechanisms at play. In the end, she found that a key factor was that the liquid jet was transferring some of its electrical charge to the surrounding gas, which breaks into charged particles and carries some of the electrical current. Korkut's predecessors and other scientists had looked only at the density of the electrical charges on the surface of the liquid jet.
Expanding her view of the system led Korkut to a simple way to control the stability of the jet by changing the gas and the amount of water vapor. She was able to produce an extremely straight and stable jet more than 8 millimeters from the nozzle. The result is highly practical not only because of the fineness of the stream but also because the large size of the nozzle and the distance from the nozzle to the printed surface will prevent clogs or jams.
Aksay said a chief use for the technique could be in printing electrically conducting organic polymers (plastics) that could be the basis for large electronic devices. Conventional techniques for making wires of that size (100 nanometers) require laboriously etching the lines with a beam of electrons, which can only be done in very small areas. The new technique can lay down lines at the rate of meters per second as opposed to millionths of a meter per second. Another application would be to use a liquid that solidifies into a fiber for making precise three-dimensional lattices. Such a product could be used as a scaffold to promote blood clotting in wounds and in other medical devices.
Princeton University has filed for a patent on the discovery and has licensed rights to Vorbeck Materials Corp., a specialty chemical company based in Maryland.
Other news from the department research and development
These products might interest you
Most read news
More news from our other portals
See the theme worlds for related content
Topic world Sensor technology
Sensor technology has revolutionized the chemical industry by providing accurate, timely and reliable data across a wide range of processes. From monitoring critical parameters in production lines to early detection of potential malfunctions or hazards, sensors are the silent sentinels that ensure quality, efficiency and safety.
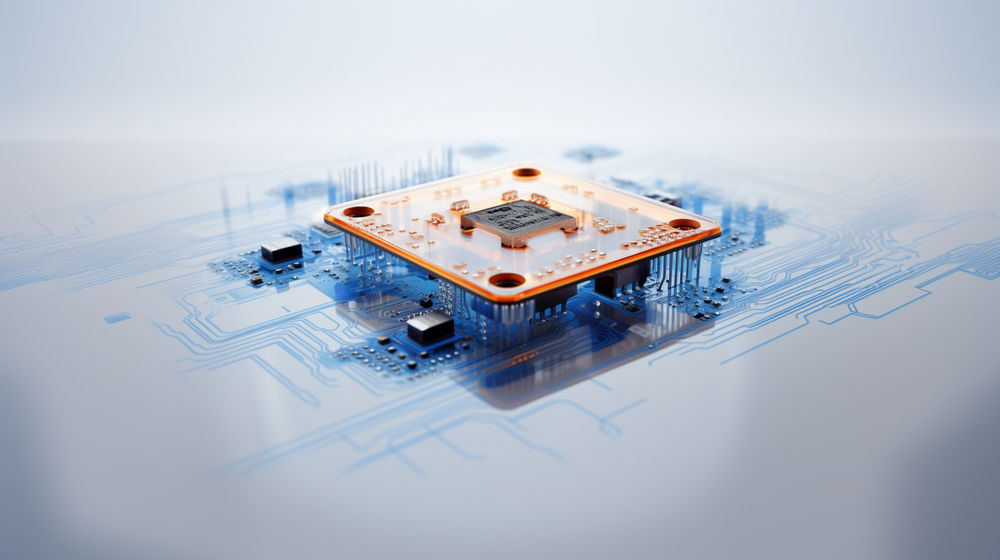
Topic world Sensor technology
Sensor technology has revolutionized the chemical industry by providing accurate, timely and reliable data across a wide range of processes. From monitoring critical parameters in production lines to early detection of potential malfunctions or hazards, sensors are the silent sentinels that ensure quality, efficiency and safety.