Dow Corning implements environmentally friendly manufacturing technology
$50 million investment to significantly reduce CO2 emissions, natural gas consumption
Dow Corning Corp. announced a $50 million investment in new equipment for its Midland, Mich., plant that is expected to reduce carbon dioxide emissions by 20 percent, total emissions by 75 percent, and lower the site's consumption of natural gas by 400 billion Btu per year - the equivalent of heating more than 3,500 homes over the winter.
The new equipment includes a recycle system designed to remove and recycle by-products from manufacturing processes, and a thermal oxidizer that will reduce air emissions from the site while generating steam for process heating.
The recycling system uses a plasma gasification process that separates the waste material generated in the chlorosilanes manufacturing process into organic and chlorine parts. The organic portion is converted into a synthetic gas for use in the steam boilers. The chlorine portion will be converted into one of the raw materials used to make chlorosilanes. Remaining materials will be turned into a relatively small amount of inert obsidian-likeglass that is also recyclable.
When fully operational this process will generate approximately one-third of the site's steam load, significantly reducing the consumption of natural gas.
Dow Corning is working with two companies on the project. The waste processing system will be owned by Integrated Environmental Technologies, LLC. A second company, Veolia Environmental Services was contracted by IET to operate the recycling equipment. Several of the new jobs created from this investment will be Veolia Environmental Services employees.
The Midland plant upgrades are the latest in a series of sustainability activities announced by Dow Corning, which in 2005 announced a five-year plan to improve employee and process safety, energy efficiency, waste and emission reduction, and environmental compatibility.
Most read news
Topics
Organizations
Other news from the department business & finance
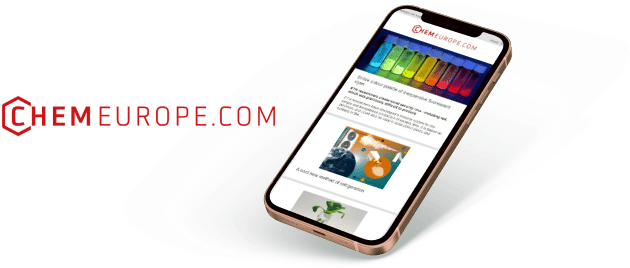
Get the chemical industry in your inbox
By submitting this form you agree that LUMITOS AG will send you the newsletter(s) selected above by email. Your data will not be passed on to third parties. Your data will be stored and processed in accordance with our data protection regulations. LUMITOS may contact you by email for the purpose of advertising or market and opinion surveys. You can revoke your consent at any time without giving reasons to LUMITOS AG, Ernst-Augustin-Str. 2, 12489 Berlin, Germany or by e-mail at revoke@lumitos.com with effect for the future. In addition, each email contains a link to unsubscribe from the corresponding newsletter.