Chemistry keeps the black gold gushing
Oilfield chemicals from BASF help in extracting the sought-after raw material crude oil from the ground more efficiently
Another 50 years, estimates the Association of the German Petroleum Industry, is how long the currently known oil reserves will last. Admittedly, such estimates are contested among experts. The real question is how much of these subterranean resources can be brought to the surface at a justifiable cost using existing technologies. The pressure in the oil reservoir forces only the first 3 percent of a deposit to the surface, and 10 to 20 percent can be raised with traditional pumping technology. But gaining access to at least part of the remaining oil requires the use of more advanced technologies and support from chemistry.
This is where BASF plays a major role with its full range of oilfield chemicals. "From the first test drill onwards, BASF products accompany the entire production process and allow the deposits to be accessed much more intensively. Only with these materials can we achieve an oilfield yield of 30 percent and more", explains Dr. Gregor Brodt, responsible for the development and applications technology of oilfield chemicals at BASF. The range of products offered by the Ludwigshafen company is as diverse and varied as the much sought-after raw material itself. Because oil is not the same everywhere, and each well produces a different type of black gold. Crude oil quality extends from viscid, almost tarry heavy oils to very light, tea-colored variants. And in each case, specially selected oilfield chemicals are used from the drilling to the production stage: the drill head has to be cooled and lubricated, the cuttings dispersed and flushed upwards; the technical process is optimized by additives to the drill flushing fluid circulating in the closed system. Other chemicals prevent the surrounding rock formations from swelling, which could otherwise trap the drill or even cause it to snap.
BASF additives are also used to control the flowability and setting time of the concrete, allowing it to be ideally adjusted to the prevailing conditions. And even when the borehole has finally advanced as far as the deposit, the engineers are often called upon to provide ingenious solutions. Because oil doesn't just lie around in underground lakes waiting to be pumped to the surface. Rather, it is enclosed in porous rock formations that only grudgingly yield up their riches. To promote the flow of oil, the tiny pores in the limestone are widened with the aid of hydrochloric acid. Unfortunately, this attacks not only the limestone but also the valuable oil production facilities - so corrosion inhibitors from BASF are used to protect the sensitive equipment by forming a thin protective film on the metal.
To prevent the widened pores from closing again under the weight of the rock formations bearing down on them, special support materials called proppants are required. These include special sands produced by the US company Engelhard recently acquired by BASF. The special sand can be pumped like a liquid around the borehole into the pores that have been created, where it produces a maximum of hollow spaces through which the oil can flow from the deposit to the tubing.
Topics
Organizations
Other news from the department research and development
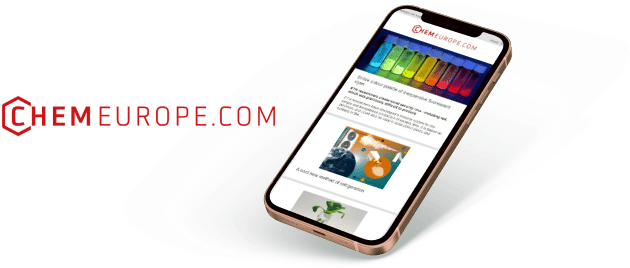
Get the chemical industry in your inbox
By submitting this form you agree that LUMITOS AG will send you the newsletter(s) selected above by email. Your data will not be passed on to third parties. Your data will be stored and processed in accordance with our data protection regulations. LUMITOS may contact you by email for the purpose of advertising or market and opinion surveys. You can revoke your consent at any time without giving reasons to LUMITOS AG, Ernst-Augustin-Str. 2, 12489 Berlin, Germany or by e-mail at revoke@lumitos.com with effect for the future. In addition, each email contains a link to unsubscribe from the corresponding newsletter.
Most read news
More news from our other portals
Last viewed contents
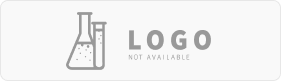
ARGUS - Additive Plastics GmbH - Büren, Germany
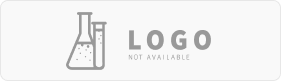
E+E Elektronik Ges.m.b.H. - Engerwitzdorf, Austria
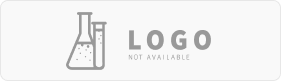
BASF Argentina S.A. - Buenos Aires, Argentina
Lehigh University professor receives Astellas Award for arsenic groundwater remediation efforts
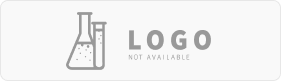
L&R Kältetechnik GmbH & Co.KG - Sundern, Germany
Deep Earth heat surprise
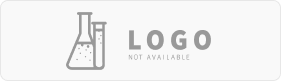
Bohncke GmbH - Hünstetten-Wallbach, Germany
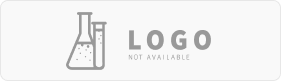
TRM Systec - Ettringen, Germany
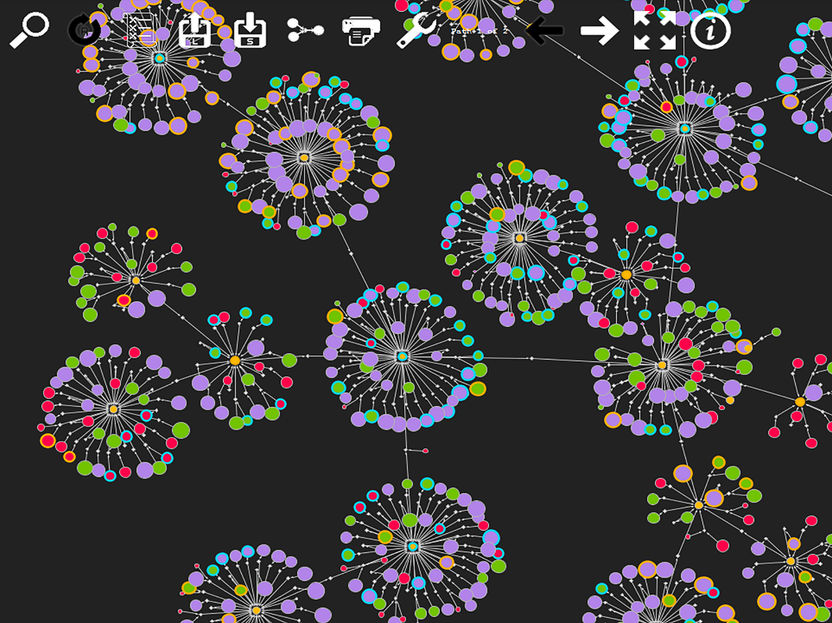