Hot off the Press
Universal ink for microcontact printing
"Printing" on the micrometer scale is the technology of the future for the production of the electronic components used for such things as flat-screen monitors or (bio)sensors. Metal surfaces a few tens of square centimeters in size can already be structured without much experimental difficulty through a combination of microcontact printing and an etching process. Researchers are currently working to develop a simple production technology that is also broadly applicable for large surfaces. A team at Philips Research in Eindhoven in the Netherlands has now developed a universally applicable "ink" for microcontact printing.
The first step in microcontact printing is the production of an elastomeric malleable stamp by means of a mold. The stamp is then loaded with a special "ink" and is pressed onto the metal surface to be printed. The ink sticks to the metal surface and reproduces the microstructure of the stamp in a monomolecular layer. This monolayer acts as a corrosion-resistant mask in the subsequent etching process: the coated areas are not affected, whereas the metal in the uncoated areas is etched away, transferring the microstructure to the metal. Precious and coinage metals are both used, as are materials with oxidic surfaces, such as silicon and aluminum. Each type of surface requires a different type of ink to stick to it: precious and coinage metals need ink molecules that can be bound by means of a metal-sulfur bond. Oxidic surfaces bind molecules with an acid functionality, such as carboxylic acids or phosphonic acids. Substrates that have different types of metals on their surface are thus not easy to structure. Also, identical structures cannot be transferred onto different substrates with the same stamp, because once loaded, the stamp cannot be "washed" off and loaded with a different ink easily-and production of a new stamp is the most expensive part of the process.
The researchers led by Dirk Burdinski have now developed a universally applicable ink. It consists of a mixture of both types of ink, sulfur-containing octadecanethiol and octadecanephosphonic acid. When polydimethylsiloxane stamps are loaded with this ink, both types of metals can be structured. The individual components of the ink are selectively transferred to their corresponding surface without interfering with each other. This universal ink is potentially also useful for the coating of microfluidic systems on diagnostic chips, as these often have inner wall structures made of different materials. Also electronic component blocks requiring good adherence of the protective coating to different components could thus first be homogenized at the surface, allowing for better sealing.
Original publication. D. Burdinski et al.; "Universal Ink for Microcontact Printing"; Angewandte Chemie International Edition 2006.
Most read news
Organizations
Other news from the department science
These products might interest you
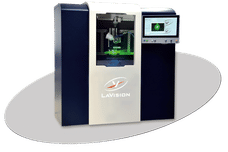
SprayMaster inspex by LaVision
Quality Control for Your Spraying Process Through Digital Spray and Particle Analysis
Reliable, Automated, Digital - The Geometry Measurement of Your Spraying Process in Real Time
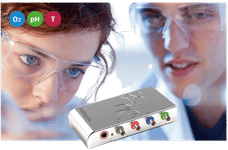
FireSting-PRO by PyroScience
New fiber optic measuring device: Precise measurements even in the smallest volumes
Measure pH, oxygen and temperature even under sterile conditions
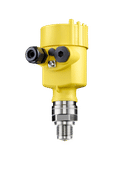
VEGAPULS | VEGABAR | VEGASWING by VEGA Grieshaber
Cyber-safe level measurement - here's how it works
Find out more about the unique sensor for liquid and solid media
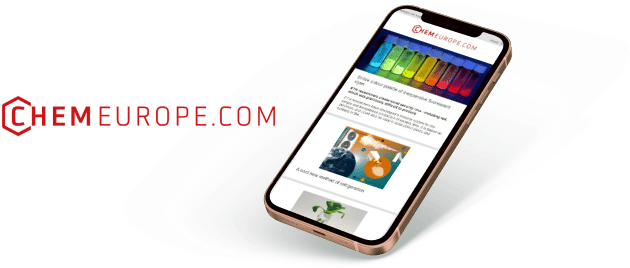
Get the chemical industry in your inbox
By submitting this form you agree that LUMITOS AG will send you the newsletter(s) selected above by email. Your data will not be passed on to third parties. Your data will be stored and processed in accordance with our data protection regulations. LUMITOS may contact you by email for the purpose of advertising or market and opinion surveys. You can revoke your consent at any time without giving reasons to LUMITOS AG, Ernst-Augustin-Str. 2, 12489 Berlin, Germany or by e-mail at revoke@lumitos.com with effect for the future. In addition, each email contains a link to unsubscribe from the corresponding newsletter.
Most read news
More news from our other portals
See the theme worlds for related content
Topic world Sensor technology
Sensor technology has revolutionized the chemical industry by providing accurate, timely and reliable data across a wide range of processes. From monitoring critical parameters in production lines to early detection of potential malfunctions or hazards, sensors are the silent sentinels that ensure quality, efficiency and safety.
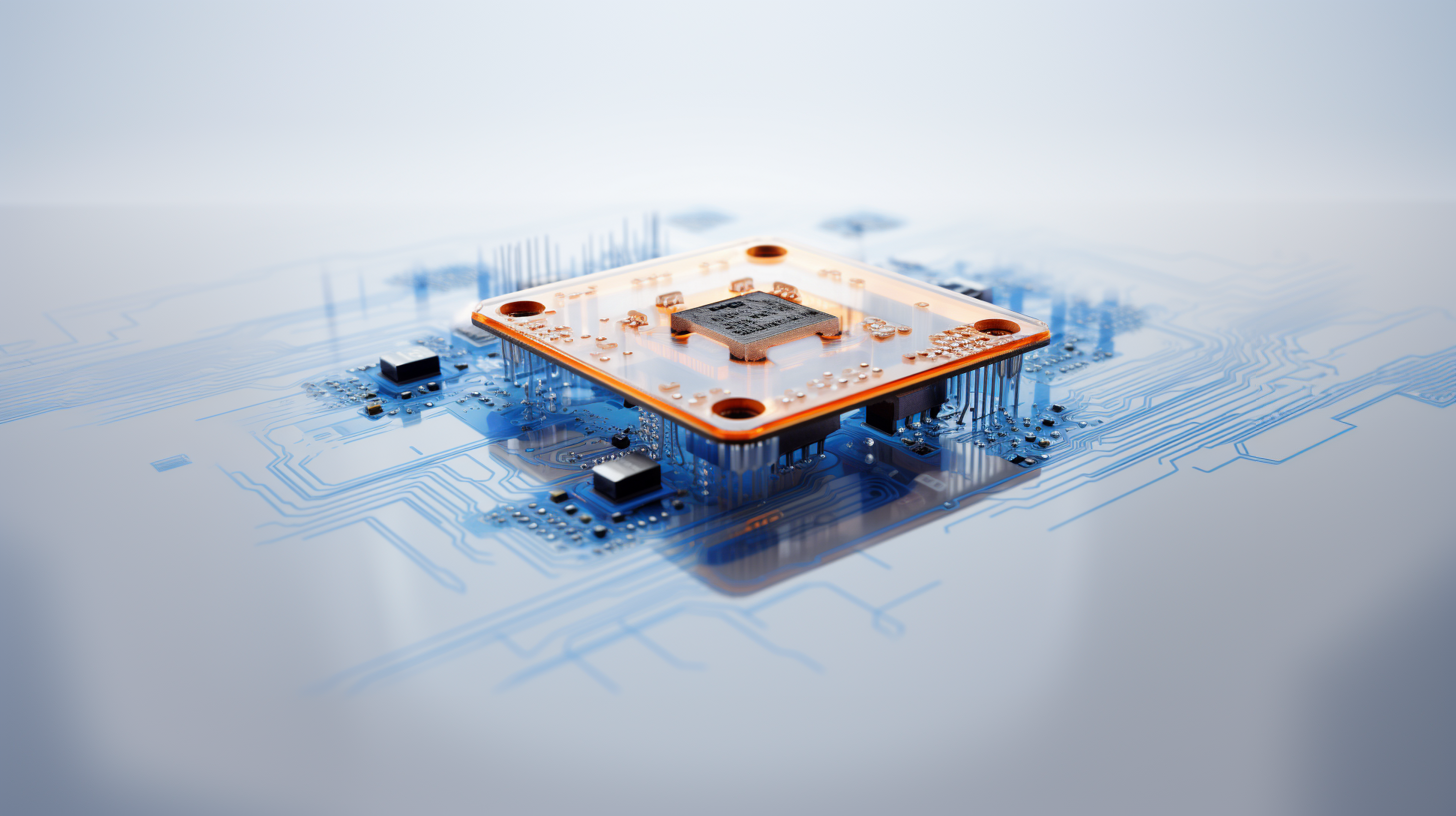
Topic world Sensor technology
Sensor technology has revolutionized the chemical industry by providing accurate, timely and reliable data across a wide range of processes. From monitoring critical parameters in production lines to early detection of potential malfunctions or hazards, sensors are the silent sentinels that ensure quality, efficiency and safety.
Last viewed contents
Labcyte and Deerac Fluidics Combine Forces to Enhance Low Volume Liquid Handling
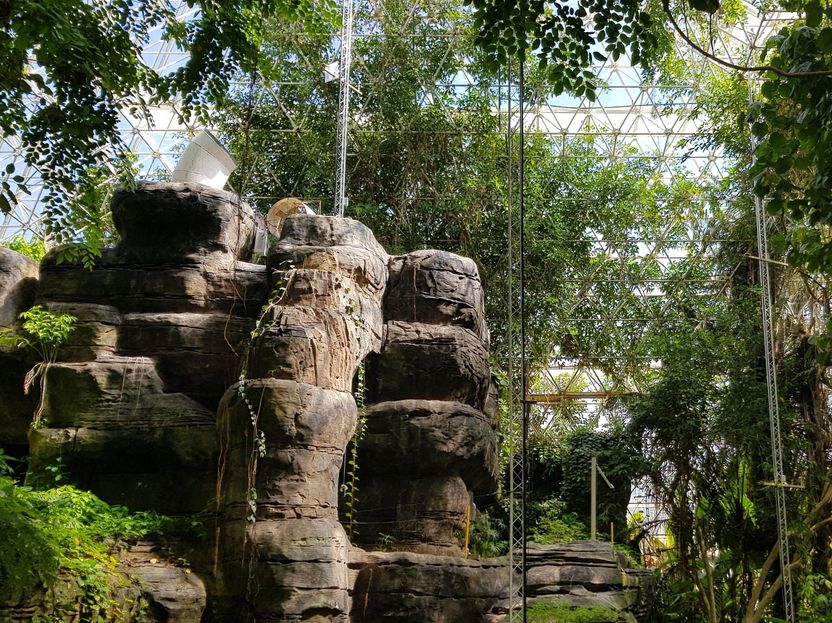
Mirror image molecules reveal drought stress in forests - Ecosystem changes can be more accurately predicted by emissions of chiral compounds
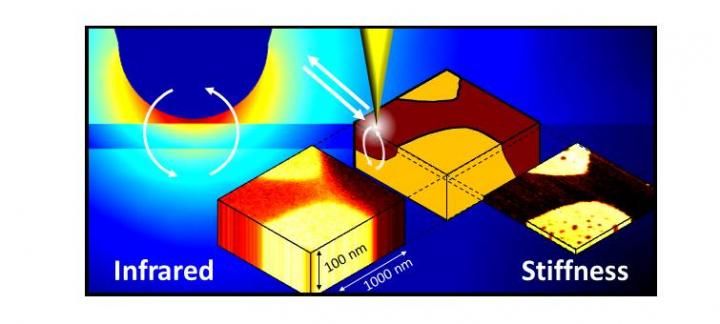
New depths in infrared nanospectroscopy - Subsurface chemical nanoidentification by nano-FTIR spectroscopy
Improved quality control of silicon carbide epiwafers by a new fast and contactless inline inspection tool
Organic nanoparticles from LANXESS now ready for series production
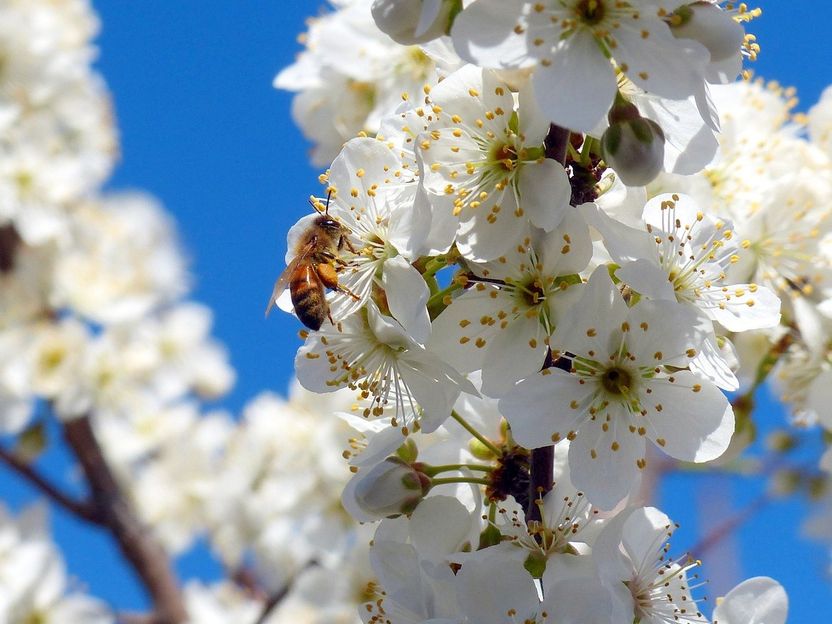
Neonicotinoid pesticides cause harm to honeybees
Bruker Corporation Appoints Charles F. Wagner, Jr. as Executive Vice President and New Chief Financial Officer
Rhodia and SIBUR sign letter of intent for joint venture in surfactants in Russia and CIS
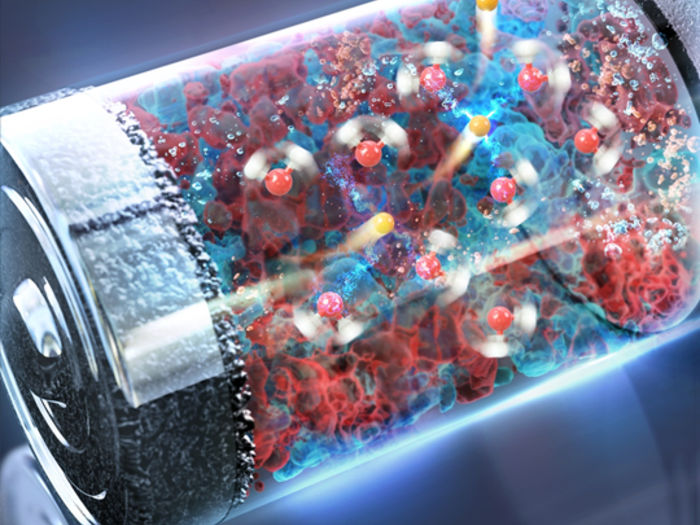
New research reveals the mechanism of ion transport in aqueous Li-ion batteries - Microscopic understanding of solvation structure reveals heterogeneity in the superconcentrated water-in-salt electrolytes
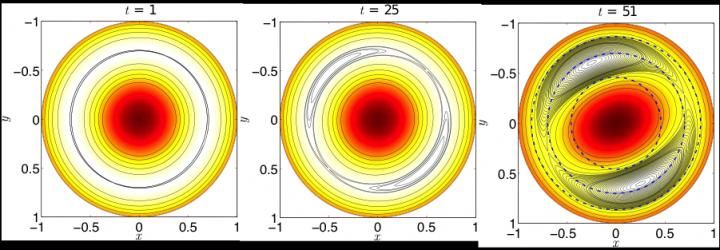
Explaining a mysterious barrier to fusion known as the 'density limit'
Investing in the future: Bohle Technology Center to be opened in March 2015
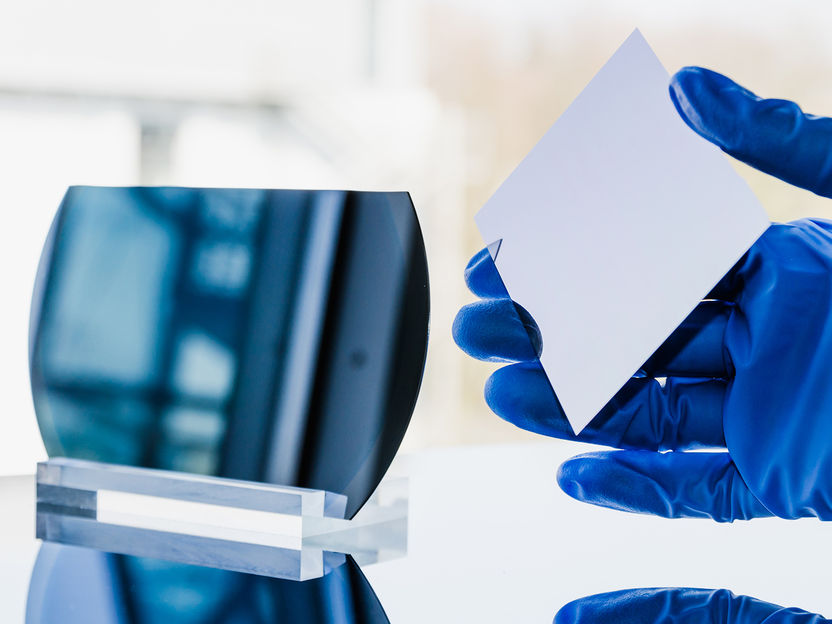