Plastics Materials - Cutting-Edge Technologies and Trends
Global competitiveness in plastics application development is set to centre on a sustained commitment to relating the "parts to the whole" of plastics materials technology. To maintain competitiveness, plastics material suppliers are also expected to continually hone their technical expertise in an effort to provide unique, technologically advanced products to end users.
"The foundation of global, cost performance effective, plastics application development is driven by early adoption of emerging, cutting-edge plastics materials technology trends in the volume oriented, intermediate cost/performance and higher-end specialty polymer industry segments," notes Technical Insights Sr. Research Analyst, Dr. Donald Rosato.
An ability to offer unique, differentiated value-added plastics materials is being viewed as critical to market success. In particular, the productivity enhancement provided by plastics materials is likely to underpin their widespread acceptance by manufacturing customers. Accordingly, plastics material suppliers are likely to be compelled to sharpen focus on technical development and launch innovative materials in the market.
"Customer- or application-specific grade development and customised offerings - whether in terms of grades, colours or special effects - are essential to maintaining growth," adds Dr. Rosato. "Leveraging expertise in part renderings through to finished design, highly selective and technology driven reinvestment back into R&D and application development will be key requirements of plastics materials suppliers globally."
With cutting-edge technologies emerging across all segments of the plastics industry, a keen understanding of evolving trends in related segments is likely to be fundamental to any successful integrated plastics technology programme.
Already, the industry is witnessing several exciting new technological developments including the introduction of economical, metallocene-based polypropylenes with polyethylene terephthalate (PET) -like properties that are poised to make forays into hot-fill packaging.
Weatherable, scratch/chemical resistance, durability over a 10-year period and a Class A decorative finish are underlining the appeal of a 'paintless' polycarbonate copolymer film in the automotive industry and related plastics end-use markets. The film is expected to remove the need for paint ovens and reduce related capital equipment and part costs by half on average.
High-tech ethylene propylene diene monomer (EPDM) rubber is significantly augmenting the toughness range in vulcanised thermoplastic olefins (TPOs). Ultra high performance, rigid rod, self reinforced polymers are eliminating the need for added fillers, while providing properties not achievable with traditional engineering plastics, positioning them as potential substitutes to metals and composites.
New compounded, semi-crystalline polyesters are poised to open up a host of new opportunities for plastics materials to replace metals across numerous applications. Plastic transistor chips that could be used in everything from walls to cars and with the potential to be spray-painted onto are set to redefine conventional thinking on human-machine interface.
"Future plastics materials application development will require not only leveraging traditional, well-defined cost performance parameters, but discerning secondary yet strategic nuances that will sustain market growth in the long term," cautions Dr. Rosato.
"Strategic nuances existing today include such focal points as regulatory legislation, particularly in the areas of continuous improvement in size and weight reduction; product design for enhanced reusability; automated/robotic handling systems that make it important that a finished plastic product conforms to a precise size and cradle to grave recyclability," he adds.
For instance, European legislation pressuring end users to lessen secondary packaging weight is favouring stretch hoods and stretch wrap over thicker shrink hoods. As a consequence, the blown film business for stretch hood applications is exploding in Europe, with the market forecast to increase by an annual average of 22 per cent through 2007.
Most read news
Other news from the department business & finance
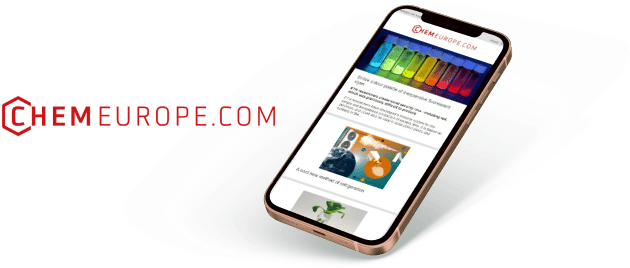
Get the chemical industry in your inbox
By submitting this form you agree that LUMITOS AG will send you the newsletter(s) selected above by email. Your data will not be passed on to third parties. Your data will be stored and processed in accordance with our data protection regulations. LUMITOS may contact you by email for the purpose of advertising or market and opinion surveys. You can revoke your consent at any time without giving reasons to LUMITOS AG, Ernst-Augustin-Str. 2, 12489 Berlin, Germany or by e-mail at revoke@lumitos.com with effect for the future. In addition, each email contains a link to unsubscribe from the corresponding newsletter.