Electrochemical extraction of silicon: new approach for a more environmentally friendly large-scale process?
Environmentally Friendly Silicon Production
silicon plays an essential role in electronic components such as solar cells and semiconductor chips, as well as in the production of silicones. The semimetal is also an important constituent of alloys. Today, industrial processes for the production of elemental silicon are generally based on the reduction of silicon dioxide (SiO2, quartz) by carbon at 1700 °C. In this reaction, the carbon reacts with the oxygen in the quartz to form carbon dioxide (CO2). In 2002, about 4.1 million tonnes of silicon was produced world-wide, with a corresponding release of 6.5 million tonnes of the greenhouse gas CO2 into the atmosphere. This undesired release could be avoided with a new electrochemical process for the extraction of silicon, which would also require less energy than the classical carbothermal process. The new technique, developed by chemists at Wuhan University in China, could form the basis for large-scale production of silicon.
For the electrochemical extraction of silicon, George Z. Chen and his team took the approach of using silicon dioxide itself as the material for the negative electrode (cathode). Molten calcium chloride is well suited as the electrolyte for such electrochemical reductions of metal oxides at high temperatures. The problem is that silicon dioxide is an insulator-it doesn't conduct electricity. However, initial tests showed that conversion of quartz to elemental silicon occurs at the three-phase boundary between the silicon dioxide, the electrolyte, and the flattened end of a tungsten wire, which is used to connect the electrode to the circuit. As the electrolysis continues, the newly formed silicon then takes on the role of conductor. Theoretically, the reaction should work its way through the entire quartz electrode. However, in practice only a small area around the tungsten plate is converted. The reason for this is that the electrolytic melt cannot get sufficiently deep through the produced silicon layer that forms on the surface of the quartz electrode, preventing further formation of the three-phase boundary. Chen and his co-workers have found a practical solution: instead of using a solid quartz electrode, they use a silicon dioxide powder that have been pressed into thin pellets and then sintered. The pellets are porous, so the electrolytic melt can get in. The particles are only a few micrometers in size and are completely converted to silicon powder by the electrolysis. In addition, by mixing the quartz powder with other metal-oxide powders it is possible to directly produce alloys with strictly controlled compositions.
Most read news
Topics
Organizations
Other news from the department science
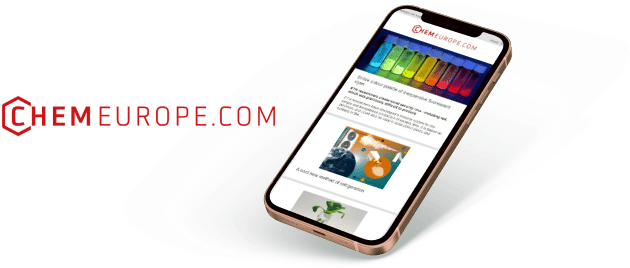
Get the chemical industry in your inbox
By submitting this form you agree that LUMITOS AG will send you the newsletter(s) selected above by email. Your data will not be passed on to third parties. Your data will be stored and processed in accordance with our data protection regulations. LUMITOS may contact you by email for the purpose of advertising or market and opinion surveys. You can revoke your consent at any time without giving reasons to LUMITOS AG, Ernst-Augustin-Str. 2, 12489 Berlin, Germany or by e-mail at revoke@lumitos.com with effect for the future. In addition, each email contains a link to unsubscribe from the corresponding newsletter.