Air Products' chemical delivery solution revolutionizes ampoule change time and cost
New system slashes downtime, cost and increases utilization rates
Air Products announced today that its new Fast Ampoule Change System (FACS) can reduce the downtime needed for the exchange of containers that deliver low vapor pressure chemicals by up to 95 percent without using heating or solvents that can add cost, require additional hardware or create solvent hazardous waste. FACS will be manufactured at Schumacher, which is headquartered in Carlsbad, California.
Along with reducing downtime, FACS boasts a design that maximizes chemical utilization. In addition, FACS removes chemical residue to levels of cleanliness comparable to, or better than, the established solutions of solvent purge systems and heating designs.
FACS is the latest product conceived and built by Air Products' Electronics Equipment Solutions business unit, unveiled in March as part of the company's vision to be the premier materials solution and service provider to the electronics industry throughout the world. The business unit has manufacturing and customer support centers in the United States, Europe, and the Pacific Rim, and includes eight distinct product lines offering customers from around the globe flexible and cost-effective ultrahigh purity materials delivery.
"Electronic Equipment Solutions business unit was created to offer our customers innovative solutions that not only met, but anticipated their needs, and this new FACS is a great example of that," said Joe Stockunas, General Manager, Electronics Equipment Solutions. "In creating FACS, we leveraged our numerous resources, including analytical resources, control systems expertise and material compatibility testing abilities to essentially build a better mouse trap. In other words, we used our unique gases and chemicals know-how to find a problem and design a solution that offers not only cost savings to our customers, but operational improvements as well," he added.
Turning Theory Into Practice
In today's chemical vapor deposition (CVD) processes, ultra low vapor pressure chemicals (less than 100mTorr) are commonly used in production. In practice, a typical ampoule replacement may take days to complete, which means the annual tool downtime can add up to weeks depending on usage and degree of success in obtaining a leak-free connection of the container. In field tests at customer sites, the FACS system reduced the tool downtime required for chemical container change outs to several hours. In laboratory tests with prototype equipment, the change out time was reduced to less than one hour.
The calculated cost savings from a decrease in downtime alone are significant, but that figure doesn't tell the whole story. Additional savings can be found by reducing the cost of facilitation, maintenance and floor space for additional tools that would normally be required to make up for the excessive downtime of current systems.
Most read news
Topics
Organizations
Other news from the department research and development
These products might interest you
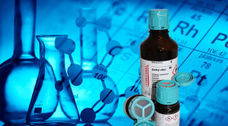
ERBAdry by CARLO ERBA Reagents
Anhydrous solvents from CARLO ERBA Reagents in a clever redesign
ERBAdry series impresses with the latest generation of septa and sealing caps
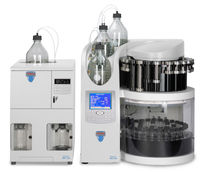
Thermo Scientific™ Dionex™ ASE™ 150 or 350 Accelerated Solvent Extractor systems by Thermo Fisher Scientific
Accelerated Solvent Extraction (ASE) – Maximize results and reduce errors in food analysis!
More extractions in less time using less solvent
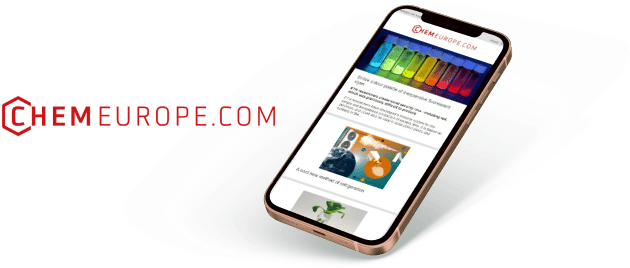
Get the chemical industry in your inbox
By submitting this form you agree that LUMITOS AG will send you the newsletter(s) selected above by email. Your data will not be passed on to third parties. Your data will be stored and processed in accordance with our data protection regulations. LUMITOS may contact you by email for the purpose of advertising or market and opinion surveys. You can revoke your consent at any time without giving reasons to LUMITOS AG, Ernst-Augustin-Str. 2, 12489 Berlin, Germany or by e-mail at revoke@lumitos.com with effect for the future. In addition, each email contains a link to unsubscribe from the corresponding newsletter.