Energy-efficient green route to magnesium production
Oxide (dolomite: MgO, CaO), which is a raw material for magnesium metal, does not absorb microwave energy well and does not generate heat. This time, when electrically conductivity ferrosilicon (FeSi) used as a reducing agent was mixed with the raw dolomite material and made into an antenna structure, it became easier to absorb the microwave energy and reduce the temperature. Internal heating and contact point heating, which are microwave characteristics, were observed, and the average reaction temperature for this smelting was lowered from the conventional 1,200 - 1,400°C to 1,000°C.
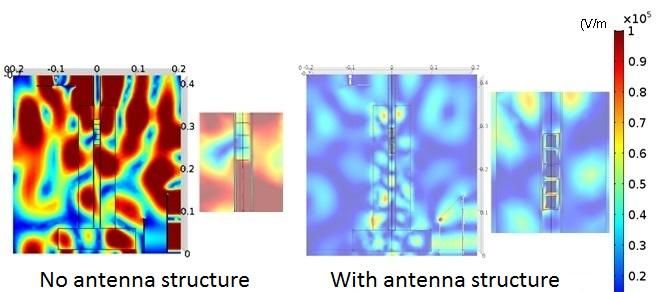
Difference in the distribution of the electric field in the applicator with and without the antenna structure through simulation.
Tokyo Institute of Technology
Research Highlights
The researchers developed a new smelting method for magnesium, which is the lightest industrial-used metal. They devised a forming method for materials to improve thermal conductivity during microwave irradiation. This is expected to result in energy savings for smelting other useful metals.
Currently, the smelting of magnesium metal is mainly performed using the Pidgeon method (thermal reduction method) where the material temperature is raised using a large amount of coal as the heat source. About 80% of magnesium metal is produced in China. A large amount of coal is consumed for smelting, resulting in the generation of the air pollutant PM 2.5 (fine particulate matter) and the release of carbon dioxide to the atmosphere, which are major problems.
The Pidgeon method is a technique for heating dolomite ore and silicon iron to high temperatures and then cooling the evaporated magnesium to obtain magnesium metal.
Research Achievements
Normally, dolomite is a poor absorber of microwave energy and does not generate heat. However, by using ferrosilicon as the reducing agent, devising the shape of the raw material pellet obtained by mixing dolomite and ferrosilicon and forming it as an antenna so that it has a resonance structure of 2.45 GHz (same as the frequency for microwave ovens), it was possible to confine the microwave energy to the pellet.
In a small-scale experimental reactor, 1g of magnesium metal was smelted successfully. Also, in order to accurately estimate the energy, a demonstration furnace about 5 times larger than the experimental furnace was produced and experiments were conducted, resulting in the successful smelting of about 7g of magnesium metal. This can reduce energy by 68.6% compared with the conventional method.
Future Developments
This success in saving energy for smelting magnesium metal has led to the possibility of this technique being developed and applied to the high temperature reduction process of oxides. In the future, through further development of this research, it will be applied to the smelting of other metal materials to save energy with steel, metals, materials, and chemistry, which have not advanced, and help reduce carbon dioxide, which is one of the causes of global warming.
Original publication
Other news from the department science
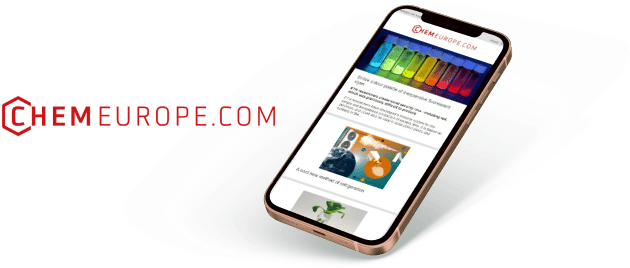
Get the chemical industry in your inbox
By submitting this form you agree that LUMITOS AG will send you the newsletter(s) selected above by email. Your data will not be passed on to third parties. Your data will be stored and processed in accordance with our data protection regulations. LUMITOS may contact you by email for the purpose of advertising or market and opinion surveys. You can revoke your consent at any time without giving reasons to LUMITOS AG, Ernst-Augustin-Str. 2, 12489 Berlin, Germany or by e-mail at revoke@lumitos.com with effect for the future. In addition, each email contains a link to unsubscribe from the corresponding newsletter.