Cold plasma: Get started with the Disc Jet
Plasmas are often found in the center of stars – on Earth, the electrically charged gas mixtures are a rare occurrence, such as in lightning discharges or aurora borealis lights. However, you can provide some help with high heat or high electrical voltages. Fraunhofer researchers have produced cold plasmas and used them for the surface treatment of temperature-sensitive materials. In doing so, recesses or undercuts were no longer a problem, thanks to a new technology – the Disc Jet can reach everywhere.
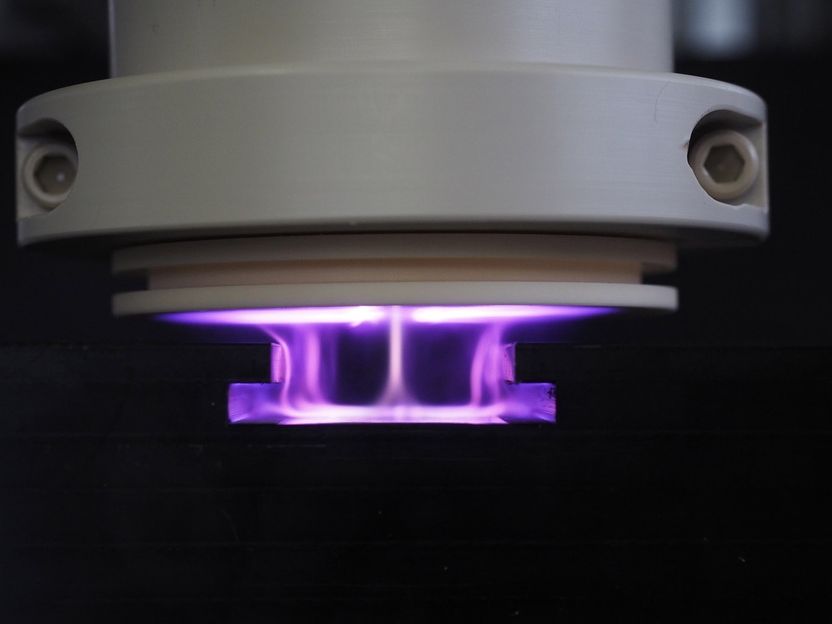
The Disc Jet can also be used to process cavities.
© Foto HAWK
Plasmas have long been used in industry to clean surfaces or to process them such that materials like paints or glues adhere to them more effectively. The advantage: Chemical pre-treatment with solvents or other substances can be dispensed with. This saves money and is environmentally friendly. The problem: Previously, only flat surfaces could be treated; the plasma simply slid over recesses, cavities or undercuts. Researchers at the Fraunhofer Institute for Surface Engineering and Thin Films IST have now combined two plasma processes – the plasma jet and the glide discharge – in order to be able to also process three-dimensional components effectively.
Optimal for the treatment of plastics or wood
"Inside the plasma jet, which essentially consists of an electrode and a nozzle, a cold plasma is generated with the help of alternating voltage," explains Martin Bellmann, engineer in the Application Center for Plasma and Photonics of the Fraunhofer IST. Depending on the requirements, different gases or gas mixtures are used. The high electrical voltage of the electrode ensures that negatively charged electrons leave the atomic shell; the larger, positively charged ions remain behind: the gas becomes conductive and, therefore, turns into energetic plasma. "Because the plus and minus poles of the electrode change constantly, the ions hardly move and release little energy in the form of heat, while only shaking back and forth a little," says Bellmann. In this way, the temperature can be kept low at 30 to 60 degrees Celsius – which is ideal for the treatment of heat-sensitive materials, such as plastics or wood.
Process also detects cavities, recesses and undercuts
The free electrons are then blown onto the component with a nozzle. Because the material surface is not conducting, they cannot react with it. Therefore, they fire back to the underside of the jet. This results in numerous small flashes, so-called sliding discharges, which spread out concentrically around the nozzle between the underside of the device and the component. "The shape of this spread is reminiscent of a CD, which is why we have christened our development the Disc Jet." The result: uniform treatment of the complete surface – wells, recesses and undercuts included.
Plasma radiation functions physically and chemically
The plasma jet works not only physically by roughening the surface slightly (which makes it easier for applied substances to adhere) but also chemically. This occurs because the unstable atoms and molecules of the plasma are highly reactive. If air is used as plasma gas, for example, the individual oxygen atoms dissolve hydrogen atoms from the plastic surfaces, thereby enabling a better adhesion of paints or adhesives.
Organizations
Other news from the department science
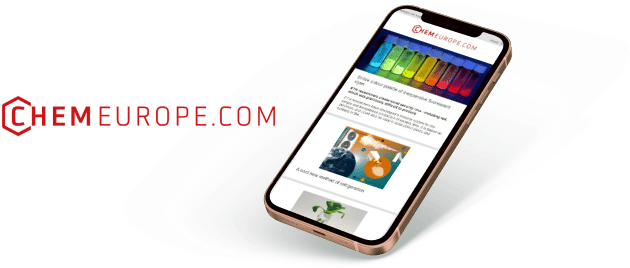
Get the chemical industry in your inbox
By submitting this form you agree that LUMITOS AG will send you the newsletter(s) selected above by email. Your data will not be passed on to third parties. Your data will be stored and processed in accordance with our data protection regulations. LUMITOS may contact you by email for the purpose of advertising or market and opinion surveys. You can revoke your consent at any time without giving reasons to LUMITOS AG, Ernst-Augustin-Str. 2, 12489 Berlin, Germany or by e-mail at revoke@lumitos.com with effect for the future. In addition, each email contains a link to unsubscribe from the corresponding newsletter.
Most read news
More news from our other portals
Last viewed contents
BASF increases prices for PolyTHF worldwide
Polymer extends life and increases power of lithium sulphide batteries
OLCO_Petroleum_Group
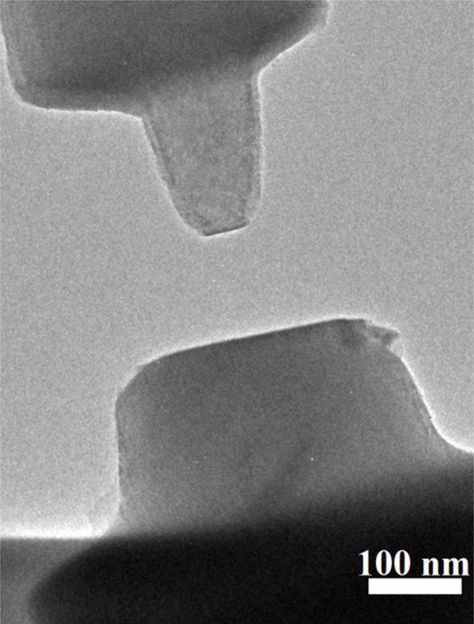
Forces that align crystals and help them snap together measured
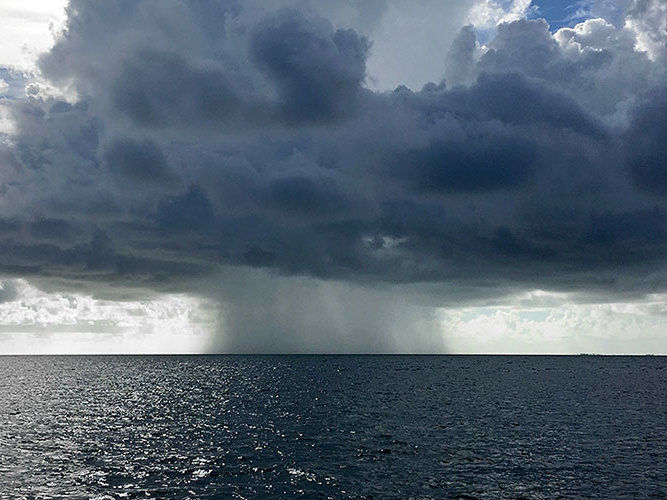
How mercury gets into the sea - Chemical fingerprint reveals origin
Dongyang_Cement
Lineweaver-Burk_plot
University of Wyoming uses NTA to characterize nanoparticles in natural environments
INP_(Korea)
Ace_Industry
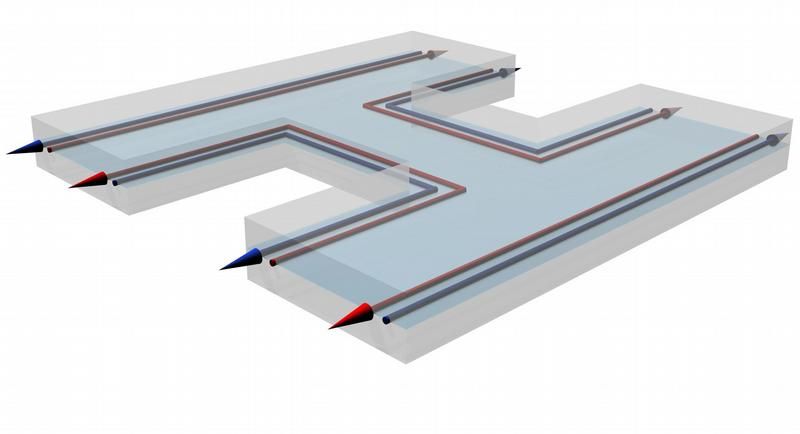