New application of the selective laser melting method
Scientists of Peter the Great St. Petersburg Polytechnic University (SPbPU) and Delft University of Technology developed a technology for obtaining new metal structures by selective laser melting method (additive technology of manufacturing three-dimensional objects from metal powders).
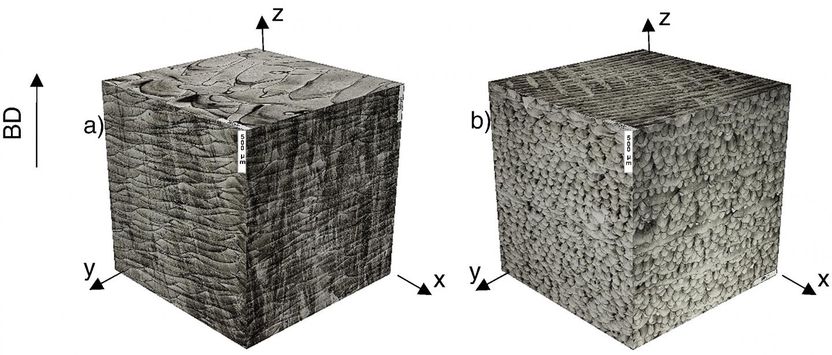
Researchers of Peter the Great St. Petersburg Polytechnic University and Delft University of Technology obtained a gradient microstructure of the material and created a product, combining properties of two metals.
Peter the Great St. Petersburg Polytechnic University
Due to this technology it is possible to obtain a gradient microstructure of the material and create a product, combining the properties of two metals. This material is characterized by high performance characteristics, such as temperature and pressure effects, strength, durability.
"This technology can be used for manufacturing of products operating in extreme conditions, such as high pressure and temperature," says Vadim Sufiiarov, assistant professor of "Development, technologies and materials in aircraft engine building" department of the Institute of Metallurgy, Mechanical Engineering and Transport SPbPU.
"Therefore, this development can be applied for manufacturing of gas turbines elements for aviation, energy and marine," adds Sufiiarov.
Generally, selective laser melting may be used to produce a fine-grained microstructure of the metal, which provides high mechanical properties at room temperature. However, the gases at combustion chamber exit of the gas turbine engine have the highest temperature and pressure. The gases aggressively act on the elements of the hot part of the turbine, primarily on blades and vanes, which are responsible for the rotor mechanism.
The first and second stage blades have the highest load, so they are not simply made using specially designed high-temperature alloys, but also form a special microstructure in the product. It is either single-crystal (when the product consists of one crystal and one grain type) or directionally crystallized (no grain boundaries in the transverse direction, all grain boundaries are located only along longitudinal direction).
With the help of this technology it is possible to create both equiaxial structures, where the grains have approximately the same dimensions in all directions, as well as directionally crystallized grains and combine their arrangement in one product. Developed approach of additive technologies allows flexible control of material microstructure formation.
Original publication
Most read news
Original publication
V.A. Popovich and E.V. Borisov and A.A. Popovich and V.Sh. Sufiiarov and D.V. Masaylo and L. Alzina; "Functionally graded Inconel 718 processed by additive manufacturing: Crystallographic texture, anisotropy of microstructure and mechanical properties"; Materials & Design; 2017
Topics
Organizations
Other news from the department science
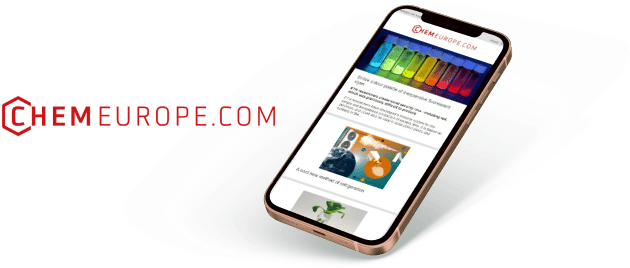
Get the chemical industry in your inbox
By submitting this form you agree that LUMITOS AG will send you the newsletter(s) selected above by email. Your data will not be passed on to third parties. Your data will be stored and processed in accordance with our data protection regulations. LUMITOS may contact you by email for the purpose of advertising or market and opinion surveys. You can revoke your consent at any time without giving reasons to LUMITOS AG, Ernst-Augustin-Str. 2, 12489 Berlin, Germany or by e-mail at revoke@lumitos.com with effect for the future. In addition, each email contains a link to unsubscribe from the corresponding newsletter.
Most read news
More news from our other portals
Last viewed contents
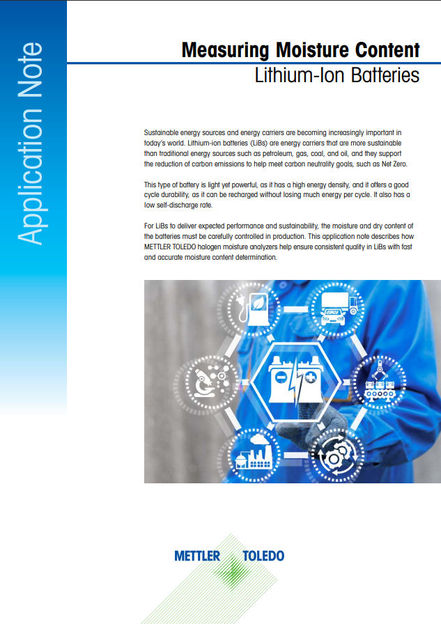
Measuring Moisture in Lithium-Ion Batteries - Fast and Accurate Moisture Content Testing for Reliable Production
ICOS Shareholders Vote to Approve Merger With Eli Lilly
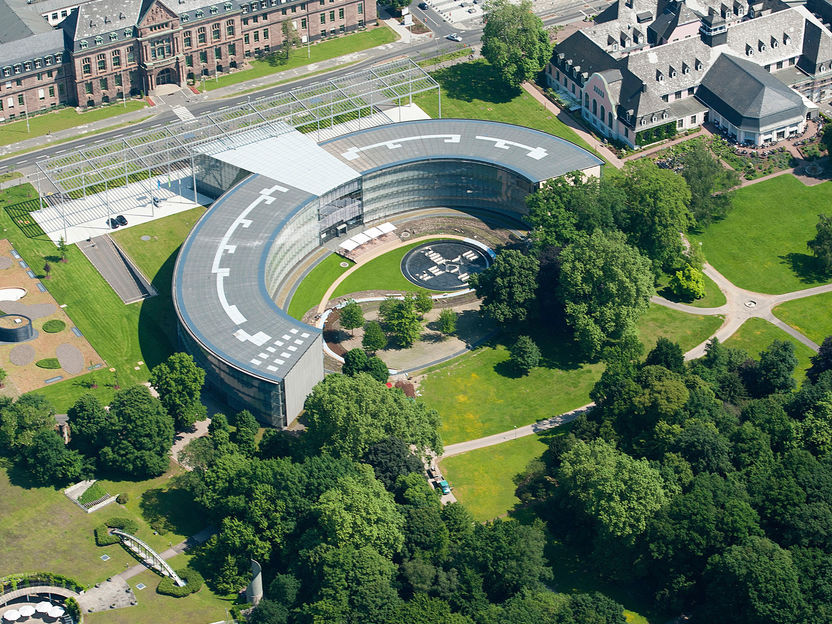