Liquid metal 3-D printer for manufacturing
A father and son team in the START-UP NY program have invented a liquid metal printing machine that could represent a significant transformation in manufacturing. A breakthrough idea five years ago by former University at Buffalo student Zack Vader, then 19, has created a machine that prints three-dimensional objects using liquid metal.
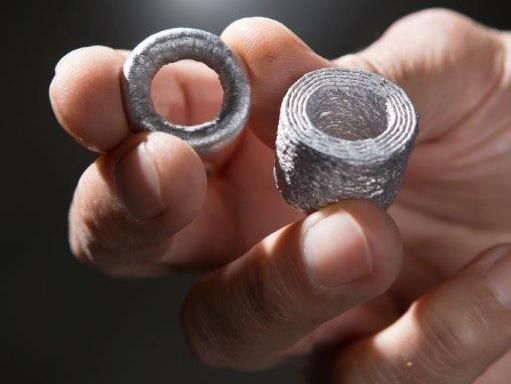
These are products printed with Vader Systems liquid metal 3-D printer.
Douglas Levere
Vader Systems is innovating and building the machines in a factory in the CrossPoint Business Park in Getzville. Zack's father Scott, a mechanical engineer, is the CEO. Zack is the chief technology officer. His mother, Pat Roche, is controller.
The machine is so novel it represents a quantum leap in the ability to print three-dimensional objects in metal. Other metal printers exist, but most use a process of laying down powered metal and melting it with a laser or electron beam. In that process, some particles of the powder do not get melted, creating weakened spots.
Manufacturers are very interested in the Vader machine, with one automotive parts maker expressing an interest in eventually buying at least 50 of them. A printer with multiple nozzles could cost more than $1 million.
UB engineering faculty and students work closely with the company
UB has been a source of intellectual assistance, grants and personnel for the startup as it transforms from a brilliant idea into an industry.
The Vaders were working on their invention in the basement of their home in Amherst when Scott decided to reach out to UB for help. "We were working alone in our basement and tackling some pretty deep technical problems," he said.
"We knocked at the door of the university and they welcomed us in," he said. "They set up an impressive first meeting with faculty experts within UB, and they said, 'What are you trying to do? What are your problems and how can we help?'"
The Vaders now have three faculty advisors, are part of the START-UP NY tax-free entrepreneurial program and have won grants from UB's Center for Industrial Effectiveness (UB TCIE), UB's Center for Advanced Biomedical and Bioengineering Technology (UB CAT) grant and a National Grid grant through UB.
In addition, and perhaps most importantly, Scott Vader said, access to university students for internships has helped the company grow. Vader Systems already has hired three mechanical engineering graduates.
"This is what makes really good young engineers, to go from the theory and being able to mix in an internship with a local industry," he said. "They realize that the lab they took is something a company really needs."
Inspiration spawned by disappointment
Zack Vader, now 24, started focusing on metal printing when his plans to hire a company to 3-D print parts for a microturbine generator were stymied. No company could print the parts he needed, so he decided to make his own metal printer. His breakthrough came when he thought to expose molten metal in a confined chamber with an orifice to a pulsed magnetic field. The transient field induces a pressure with the metal that ejects a droplet. That was the key to making droplets of liquid metal eject from a nozzle.
Professor Edward P. Furlani, PhD, in UB's Chemical and Biological Engineering and Electrical Engineering departments, said that Vader's process mimics drop-on-demand inkjet printing and is based on the principles of magnetohydrodynamics, i.e. the manipulation of conductive fluids using a magnetic field. In Vader's device, an electrically-pulsed magnetic field permeates liquid metal in an ejection chamber and creates circulating electrical currents that interact with the magnetic field to produce a pressure that squeezes a droplet out of the ejector nozzle.
"It's a transformative technology," Furlani said. "It's very exciting interdisciplinary engineering. I think its application base will continue to broaden and expand for the foreseeable future."
Ciprian N. Ionita, PhD, a research assistant professor in the Biomedical Engineering Department -- a joint effort of the School of Engineering and Applied Sciences and the Jacobs School of Medicine and Biomedical Sciences at UB -- foresees the Vader Systems printer ultimately printing out custom stents and other surgical devices right in the hospital.
"This is a game changer," he said. The metal powder used in the current metal printing processes is a contaminant that is difficult to clean up and can be toxic inside the body.
The Vader printer also will be valuable making custom knee and hip replacements, he said.
Cheaper, faster, better
The third UB professor advising the Vaders, Chi Zhou, an assistant professor in the Industrial Systems Engineering Department and a 3-D printing expert, said another advantage of the Vader system is that it is "much, much cheaper" than using powered metal.
"I can see at this stage that it can complement traditional metal printing, but later, maybe 10 years later, it can dominate the metal printing market because it can print better quality, cheaper and faster," Zhou said.
Zhou has helped write original open-source software to control the printer. "If they want to add functionality, we can. We have the source code," he said.
One of the most fascinating qualities of a 3-D printer is that a complex part is just as cheap to make as a simple part.
"Complexity does not add cost," Zack Vader said, which is the opposite of traditional manufacturing. That makes the machines very attractive to companies making many complex parts.
Steel printing on the horizon
On a Vader machine, a strand of aluminum is fed into a heat element that melts it at 750 degrees Celsius. The liquefied metal is then passed to a ceramic tube that forms an ejection chamber and has a submillimeter orifice. A magnetic coil surrounds the tube and receives a short-lived electrical pulse to create a pressure within the tube that ejects a droplet of liquid metal through the orifice. The ejected drop is projected downward onto a heated platform that maneuvers to create solid 3-D shapes based on layer-by-layer deposition and the coalescence of the droplets.
Zack Vader said plans are to modify the device, adding nozzles to make it faster. Eventually the machines will be able to melt and print steel at 1,400°C.
As the machine evolves, the Vaders plan to expand their operation into an assembly line manufacturing facility. Applications for the device run the gamut. Scott Vader said the automotive industry may be interested in making parts that are now solid metal into hollow and honey-combed structures. The hollow parts would be lighter, stronger and much cheaper. And as for the tiny generator that Zack Vader was hoping to print, it may emerge again someday, now that the technology to make it is advancing.
"That's just been put on the shelf for a while," he said.
Other news from the department science
Most read news
More news from our other portals
Something is happening in the chemical industry ...
This is what true pioneering spirit looks like: Plenty of innovative start-ups are bringing fresh ideas, lifeblood and entrepreneurial spirit to change tomorrow's world for the better. Immerse yourself in the world of these young companies and take the opportunity to get in touch with the founders.