Cement made from steel production byproduct can lead to a huge CO2 reduction
steel production generates some hundred million tons of steel slag worldwide each year. This giant mountain of leftovers is largely dumped. Eindhoven University of Technology professor of building materials, Jos Brouwers, will be working with industrial partners to investigate whether he can make cement out of it. If he succeeds, more CO2 emissions can be cut than is yearly produced by all the traffic in the Netherlands.

A stockpile of steel slag, next to a steel factory.
TU Eindhoven
Steel slag is produced by the conversion of raw iron into steel - around 125 million tons of it per year. Much of that is dumped and only a small portion used, in embankments. That's a shame, professor Jos Brouwers says, because the mineralogical composition very closely resembles that of cement. It contains the same components, but in different ratios. And it is public knowledge that the cement industry emits a very high amount of CO2: five percent of the global total. A cement substitute with no extra CO2 emissions would, therefore, be most welcome.
But before this can happen, Brouwers' team has to overcome a number of scientific and technical hurdles. First, the researchers will use the very latest methods to gain a good picture of the physical and chemical properties of the steel slag as well as take a detailed look at what different additives can bring in terms of cement-like qualities.
They will then use this knowledge and computational models to design new types of cement and concrete, and test them out. "It is important that it is possible to change the composition of the steel slag by adjusting the steel production processes," Brouwers explains. "You can keep the quality of the steel consistent and still ensure that the properties of the steel slag are more favorable."
Brouwers is hopeful that he will be able to succeed in making cement from steel slag that can replace 'normal cement'. While it may well require twice as much for the same result, this new cement will still be suitable for many common applications. It will make a difference of tens of millions of tons of CO2 emissions each year. For comparison, all the traffic and transport in the Netherlands produces emissions of around thirty million tons a year. Moreover, the new cement is also a money maker. "Steel companies now have to pay for their slag to be removed; it has a negative value. If we succeed, or only in part, it could mean tens of millions of euros in the Netherlands alone," says Brouwers.
Brouwers' group is getting 750,000 euros from the STW technology foundation for this research, from the High Tech Materials funding program. With additional cash from the industrial partners, including Tata Steel, Heidelberg Cement and Inashco, the total research budget tops a million euros. In addition to Brouwers and university lecturers Qingliang Yu (co-applicant) and Miruna Florea, three PhDs and a postdoc will be working on the four-year project.
Topics
Organizations
Other news from the department science
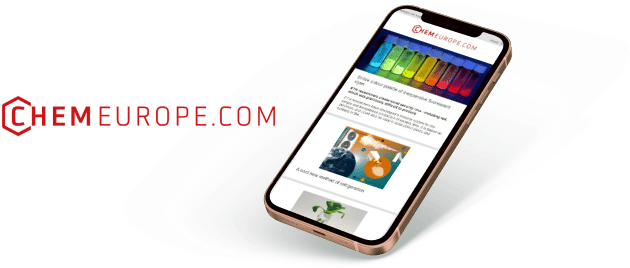
Get the chemical industry in your inbox
By submitting this form you agree that LUMITOS AG will send you the newsletter(s) selected above by email. Your data will not be passed on to third parties. Your data will be stored and processed in accordance with our data protection regulations. LUMITOS may contact you by email for the purpose of advertising or market and opinion surveys. You can revoke your consent at any time without giving reasons to LUMITOS AG, Ernst-Augustin-Str. 2, 12489 Berlin, Germany or by e-mail at revoke@lumitos.com with effect for the future. In addition, each email contains a link to unsubscribe from the corresponding newsletter.