New method increases energy density in lithium batteries
Yuan Yang, assistant professor of materials science and engineering at Columbia Engineering, has developed a new method to increase the energy density of lithium (Li-ion) batteries. He has built a trilayer structure that is stable even in ambient air, which makes the battery both longer lasting and cheaper to manufacture. The work may improve the energy density of lithium batteries by 10-30%.
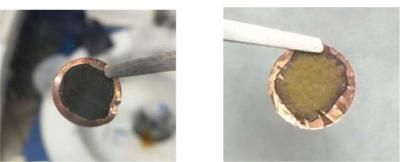
raphite/PMMA/Li trilayer electrode before (left) and after (right) being soaked in battery electrolyte for 24 hours. Before soaking in electrolyte, the trilayer electrode is stable in air. After soaking, lithium reacts with graphite and the color turns golden.
Yuan Yang, Columbia Engineering
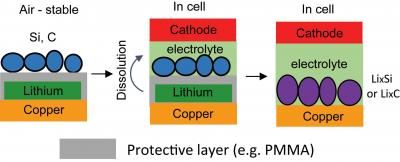
This is an illustration showing the procedure to fabricate the trilayer electrode. PMMA is used to protect lithium and make the trilayer electrode stable in ambient air. PMMA is dissolved in battery electrolyte and graphite contacts with lithium to compensate the loss due to reduction of electrolyte.
Yuan Yang, Columbia Engineering
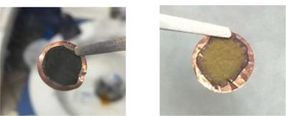

"When lithium batteries are charged the first time, they lose anywhere from 5-20% energy in that first cycle," says Yang. "Through our design, we've been able to gain back this loss, and we think our method has great potential to increase the operation time of batteries for portable electronics and electrical vehicles."
During the first charge of a lithium battery after its production, a portion of liquid electrolyte is reduced to a solid phase and coated onto the negative electrode of the battery. This process, usually done before batteries are shipped from a factory, is irreversible and lowers the energy stored in the battery. The loss is approximately 10% for state-of-the-art negative electrodes, but can reach as high as 20-30% for next-generation negative electrodes with high capacity, such as silicon, because these materials have large volume expansion and high surface area. The large initial loss reduces achievable capacity in a full cell and thus compromises the gain in energy density and cycling life of these nanostructured electrodes.
The traditional approach to compensating for this loss has been to put certain lithium-rich materials in the electrode. However, most of these materials are not stable in ambient air. Manufacturing batteries in dry air, which has no moisture at all, is a much more expensive process than manufacturing in ambient air. Yang has developed a new trilayer electrode structure to fabricate lithiated battery anodes in ambient air. In these electrodes, he protected the lithium with a layer of the polymer PMMA to prevent lithium from reacting with air and moisture, and then coated the PMMA with such active materials as artificial graphite or silicon nanoparticles. The PMMA layer was then dissolved in the battery electrolyte, thus exposing the lithium to the electrode materials. "This way we were able to avoid any contact with air between unstable lithium and a lithiated electrode," Yang explains, "so the trilayer-structured electrode can be operated in ambient air. This could be an attractive advance towards mass production of lithiated battery electrodes."
Yang's method lowered the loss capacity in state-of-the-art graphite electrodes from 8% to 0.3%, and in silicon electrodes, from 13% to -15%. The -15% figure indicates that there was more lithium than needed, and the "extra" lithium can be used to further enhance cycling life of batteries, as the excess can compensate for capacity loss in subsequent cycles. Because the energy density, or capacity, of lithium-ion batteries has been increasing 5-7% annually over the past 25 years, Yang's results point to a possible solution to enhance the capacity of Li-ion batteries. His group is now trying to reduce the thickness of the polymer coating so that it will occupy a smaller volume in the lithium battery, and to scale up his technique.
"This three-layer electrode structure is indeed a smart design that enables processing of lithium-metal-containing electrodes under ambient conditions," notes Hailiang Wang, assistant professor of chemistry at Yale University, who was not involved with the study. "The initial Coulombic efficiency of electrodes is a big concern for the Li-ion battery industry, and this effective and easy-to-use technique of compensating irreversible Li ion loss will attract interest."
Original publication
Other news from the department science
These products might interest you
Most read news
More news from our other portals
See the theme worlds for related content
Topic World Battery Technology
The topic world Battery Technology combines relevant knowledge in a unique way. Here you will find everything about suppliers and their products, webinars, white papers, catalogs and brochures.
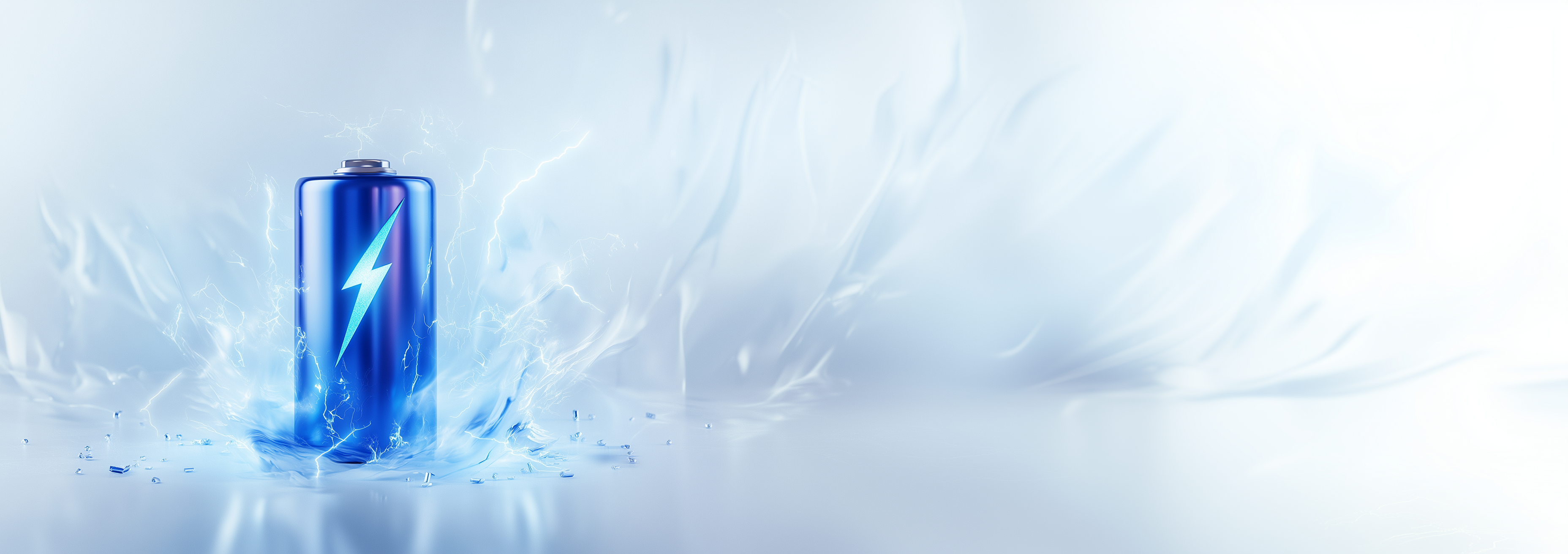
Topic World Battery Technology
The topic world Battery Technology combines relevant knowledge in a unique way. Here you will find everything about suppliers and their products, webinars, white papers, catalogs and brochures.