Asphalt-based carbon-capture material advances
Scientists improve method to pull greenhouse gas from natural gas streams
A Rice University laboratory has improved its method to turn plain asphalt into a porous material that can capture Greenhouse Gases from natural gas.

Rice University scientists have improved their asphalt-derived porous carbon’s ability to capture carbon dioxide, a greenhouse gas, from natural gas. The capture material derived from untreated Gilsonite asphalt has a surface area of 4,200 square meters per gram.
Alma Jalilov
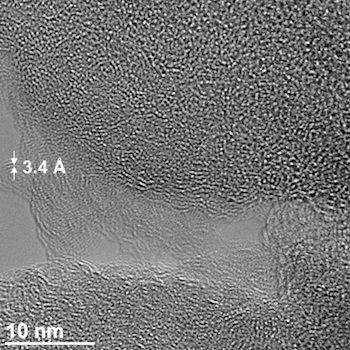
A transmission electron microscope image of Gilsonite-derived asphalt shows a micropore in the structure. The pores sequester carbon dioxide under common pressures at natural gas wellheads.
Courtesy of the Tour Group
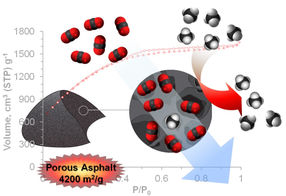
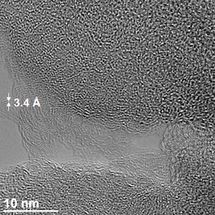
In research detailed this month in Advanced Energy Materials, Rice researchers showed that a new form of the material can sequester 154 percent of its weight in carbon dioxide at high pressures that are common at gas wellheads.
Raw natural gas typically contains between 2 and 10 percent carbon dioxide and other impurities, which must be removed before the gas can be sold. The cleanup process is complicated and expensive and most often involves flowing the gas through fluids called amines that can soak up and remove about 15 percent of their own weight in carbon dioxide. The amine process also requires a great deal of energy to recycle the fluids for further use.
“It’s a big energy sink,” said Rice chemist James Tour, whose lab developed a technique last year to turn asphalt into a tough, sponge-like substance that could be used in place of amines to remove carbon dioxide from natural gas as it was pumped from ocean wellheads.
Initial field tests in 2015 found that pressure at the wellhead made it possible for that asphalt material to adsorb, or soak up, 114 percent of its weight in carbon at ambient temperatures.
Tour said the new, improved asphalt sorbent is made in two steps from a less expensive form of asphalt, which makes it more practical for industry.
“This shows we can take the least expensive form of asphalt and make it into this very high surface area material to capture carbon dioxide,” Tour said. “Before, we could only use a very expensive form of asphalt that was not readily available.”
The lab heated a common type asphalt known as Gilsonite at ambient pressure to eliminate unneeded organic molecules, and then heated it again in the presence of potassium hydroxide for about 20 minutes to synthesize oxygen-enhanced porous carbon with a surface area of 4,200 square meters per gram, much higher than that of the previous material.
The Rice lab’s initial asphalt-based porous carbon collected carbon dioxide from gas streams under pressure at the wellhead and released it when the pressure was released. The carbon dioxide could then be repurposed or pumped back underground while the porous carbon could be reused immediately.
In the latest tests with its new material, Tours group showed its new sorbent could remove carbon dioxide at 54 bar pressure. One bar is roughly equal to atmospheric pressure at sea level, and the 54 bar measure in the latest experiments is characteristic of the pressure levels typically found at natural gas wellheads, Tour said.
Original publication
Other news from the department science
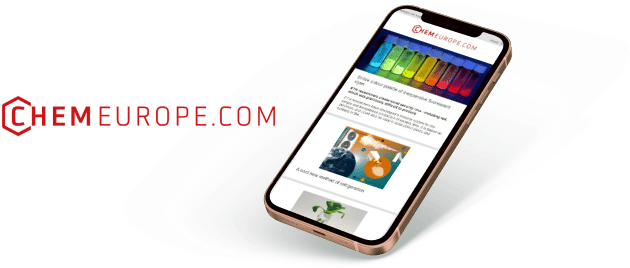
Get the chemical industry in your inbox
By submitting this form you agree that LUMITOS AG will send you the newsletter(s) selected above by email. Your data will not be passed on to third parties. Your data will be stored and processed in accordance with our data protection regulations. LUMITOS may contact you by email for the purpose of advertising or market and opinion surveys. You can revoke your consent at any time without giving reasons to LUMITOS AG, Ernst-Augustin-Str. 2, 12489 Berlin, Germany or by e-mail at revoke@lumitos.com with effect for the future. In addition, each email contains a link to unsubscribe from the corresponding newsletter.
Most read news
More news from our other portals
Last viewed contents
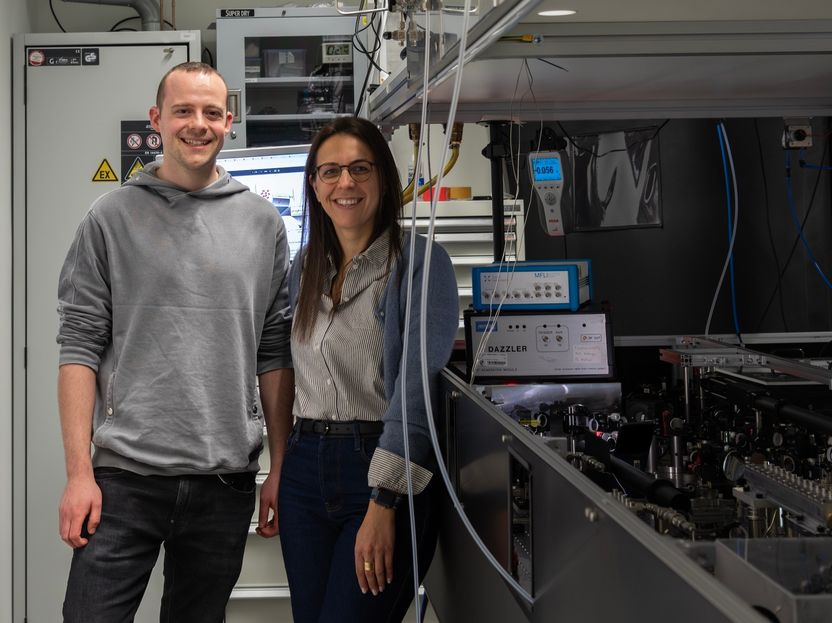