Lacquering before polishing
Technical Coatings for Additive Manufacturing
Additive Manufacturing (AM) has many advantages: custom manufacturing, flexible production and easy customization, for example. Yet many products have a high surface roughness and porosity. The post processing of the thus fabricated parts is time consuming and often a significant cost factor for manufacturers. Technical coatings open up new possibilities for the AM market, especially in industrial production.
In a joint project, researchers from the Belgian NPO Sirris and the Fraunhofer Institute for Applied polymer research IAP have investigated technical coatings for additive manufacturing (TCAM) with promising results.
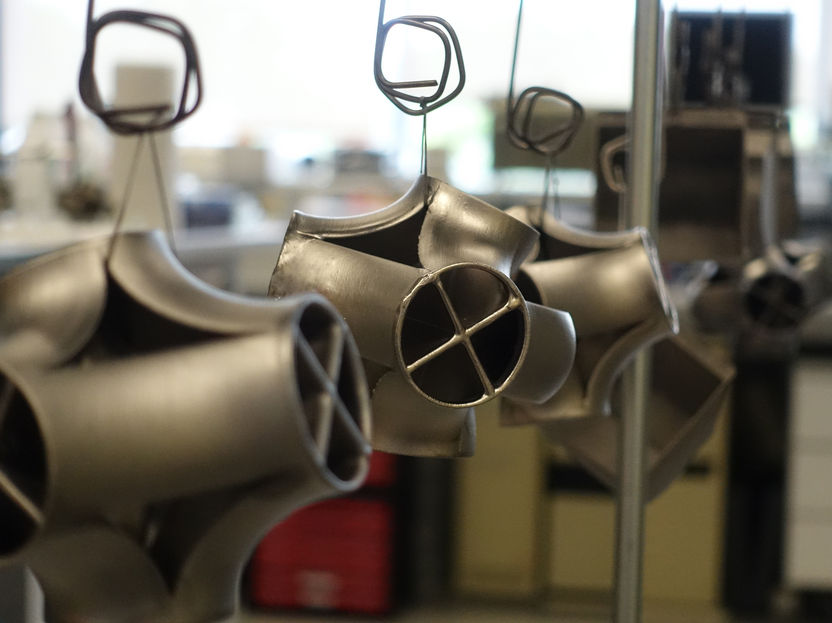
Complex AM-fabricated parts dry after their metallization.
Fraunhofer IAP
AM describes the construction of an object layer by layer using a 3D-model. The technologies vary but 3D printing is probably the best known. However, selective laser sintering (SLS), stereolithography (SLA) or material jetting (MJ) play important roles in the AM market. While the first AM technologies were developed for rapid prototyping, today, AM is taking the leap into industrial production. It is one of the important future technologies that will influence the manufacturing market and beyond. The industry can profit from AM with its production on-demand capabilities, its and flexible adaptability and the possibility to produce small quantities. However, the surface of the fabricated components is usually very rough and porous.
To meet this challenge, two partners investigated technical coatings for additive manufacturing in a joint project: Sirris is an organization focused on finding solutions for technological challenges, usually in projects with universities, research centers, companies, associations and other institutions. Researchers at the Fraunhofer IAP, among other areas of expertise, have long years of experience in technical coatings.
“Today, with the transition from rapid prototyping to industrial production, the demands on AM-manufactured components are growing. Being able to warrant consistent material quality is essential for industry producers. In addition, demands on the surface quality are growing”, says Dr. Andreas Holländer, expert in surface technology at the Fraunhofer IAP.
Technical Coatings enable smooth and sealed surfaces with specific functions
With technical coatings, the Sirris and Fraunhofer researchers were able to significantly improve AM-produced parts regarding surface roughness and porosity. It turned out that the combination of lacquering and polishing is the most efficient technique for surface optimization in AM. In addition, components can be functionalized further by using special lacquers or surface treatments. In the current project, the scientists metallized the smoothed components. The metal coating is a visible example for the functionalization process. Improved scratch resistance, antimicrobial properties and many more features are applicable.
Sirris provided different components made with SLS, SLA, MJ, and FDM (fused deposition modeling = 3D printing). All methods pose different challenges to surface treatment.
"With years of expertise in surface treatment, we are able to meet a wide range of requirements. We analyzed each part in the first step to determine the specific properties. Afterwards we were able to activate, paint, and polish and, in this case, metallize the respective surface with the appropriate method", says Holländer, who leads the research group at the Fraunhofer IAP.
Patrick Cosemans from Sirris Flanders adds: "If we only polish our finished components, it takes a long time, and especially with fine, detailed features, we change their shape. It comes to abrasion, which we want to avoid. With the Fraunhofer IAP we have developed possibilities to overcome the current problems, especially the porous and rough surface, in additive manufacturing."
Is combining AM with established technologies the future?
Conventional production methods often reach their limits with complex components. The more complex a component, the more difficult and expensive it becomes in conventional production. AM opens up possibilities to produce complex components faster and more cost-efficiently. With AM, a component that would conventionally consist of many individual parts and would have to be assembled can be created in one step.
"It is important", says Dr. Holländer, "that every part of the component’s surface has the required quality. In complicated parts, some surfaces are difficult to reach. With the appropriate surface treatment technology, which in future will even be integrated into the AM machines, we are able to functionalize even complex components completely."
Finishing the project both partners conclude that AM in combination with established technologies provides even better capabilities and more possible applications than AM alone.
Other news from the department science
These products might interest you
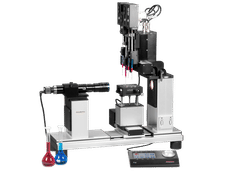
OCA 200 by DataPhysics
Using contact angle meter to comprehensively characterise wetting behaviour, solids, and liquids
With its intuitive software and as a modular system, the OCA 200 answers to all customers’ needs
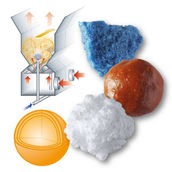
Tailor-made products for specific applications by IPC Process Center
Granulates and pellets - we develop and manufacture the perfect solution for you
Agglomeration of powders, pelletising of powders and fluids, coating with melts and polymers
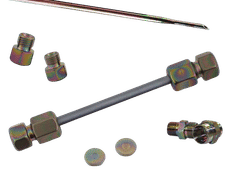
Dursan by SilcoTek
Innovative coating revolutionizes LC analysis
Stainless steel components with the performance of PEEK - inert, robust and cost-effective
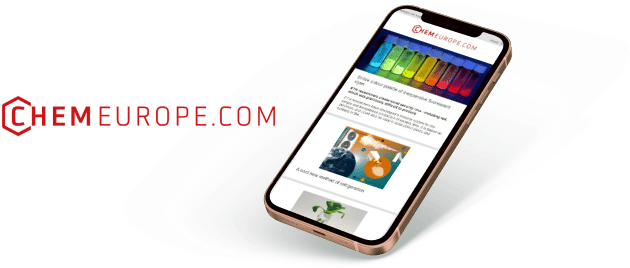
Get the chemical industry in your inbox
By submitting this form you agree that LUMITOS AG will send you the newsletter(s) selected above by email. Your data will not be passed on to third parties. Your data will be stored and processed in accordance with our data protection regulations. LUMITOS may contact you by email for the purpose of advertising or market and opinion surveys. You can revoke your consent at any time without giving reasons to LUMITOS AG, Ernst-Augustin-Str. 2, 12489 Berlin, Germany or by e-mail at revoke@lumitos.com with effect for the future. In addition, each email contains a link to unsubscribe from the corresponding newsletter.
Most read news
More news from our other portals
Last viewed contents
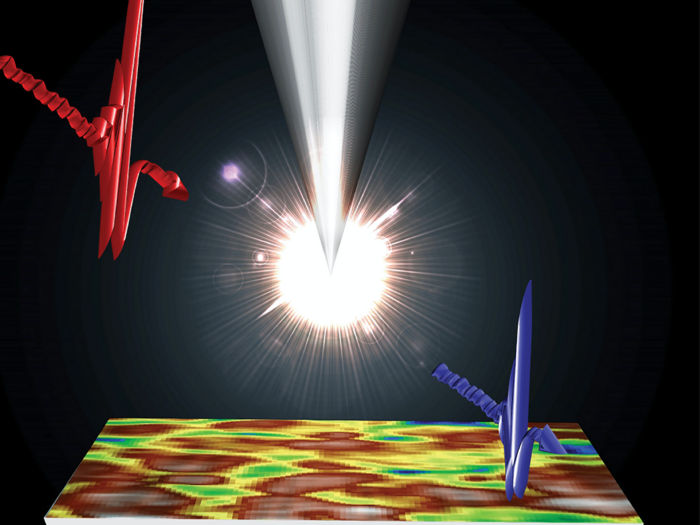
New discoveries made about a promising solar cell material, thanks to new microscope
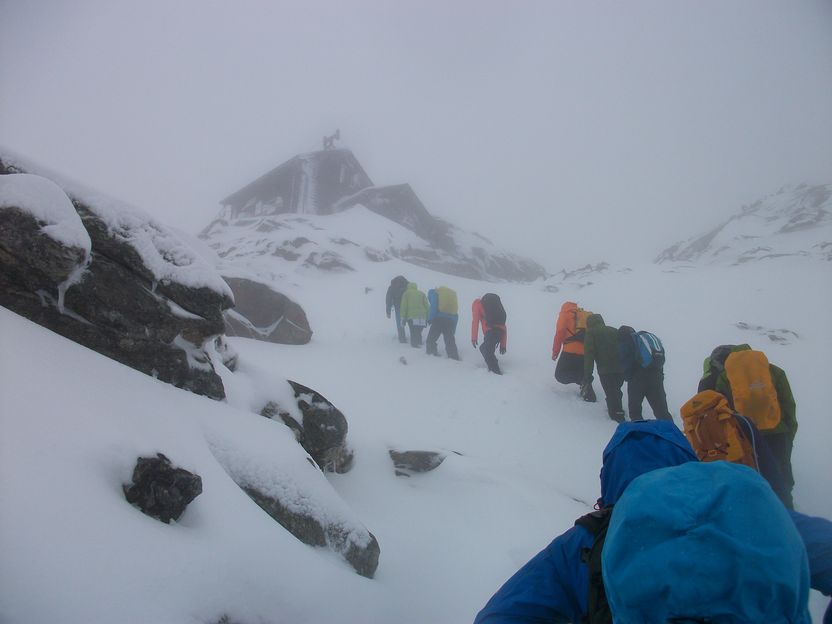
Plastic snowfall in the Alps - Nanoplastic in the environment: New chemical method for counting plastic particles developed
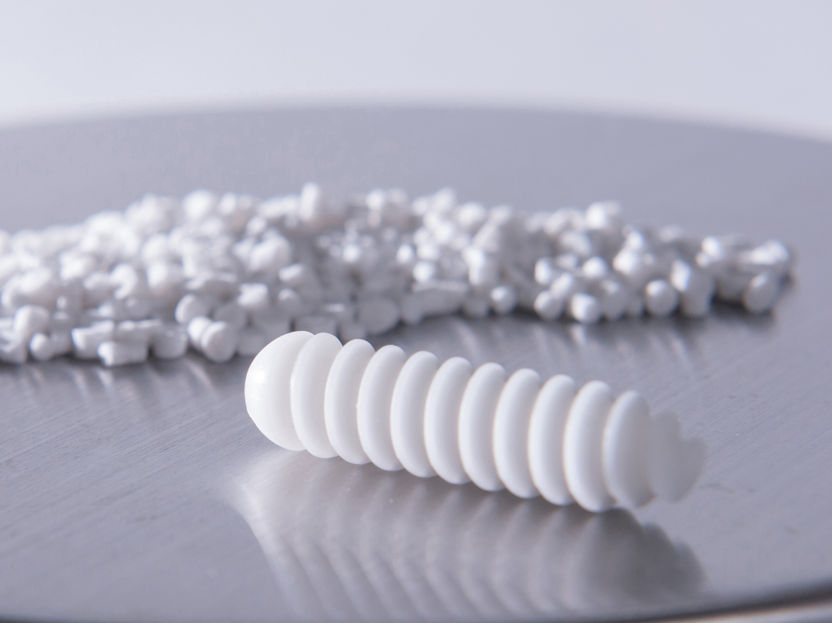