Rice's 'antenna-reactor' catalysts offer best of both worlds
In a find that could transform some of the world's most energy-intensive manufacturing processes, researchers at Rice University's Laboratory for Nanophotonics have unveiled a new method for uniting light-capturing photonic nanomaterials and high-efficiency metal catalysts.
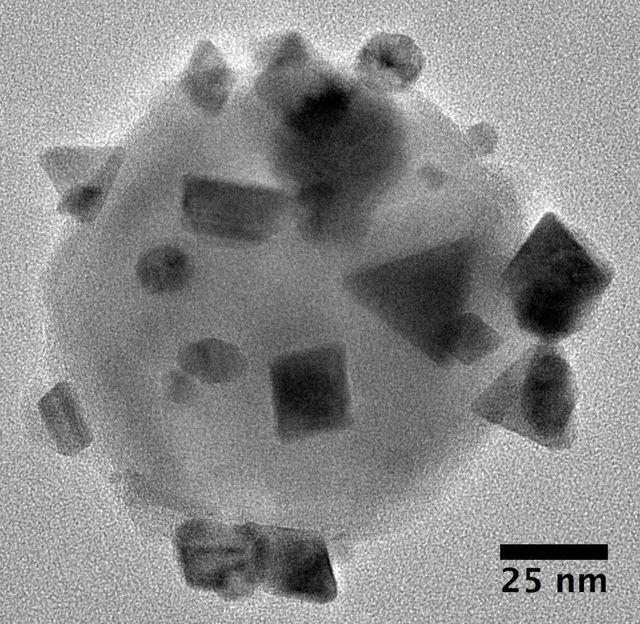
Rice University's antenna-reactor plasmonic catalysts combine light-harvesting nanomaterials with highly efficient metal catalysts. In this image, "islands" of reactive palladium dot the aluminum oxide surface of an underlying aluminum crystal, which serves as a photonic antenna to capture light and activate the catalytic islands.
D. Swearer/Rice University
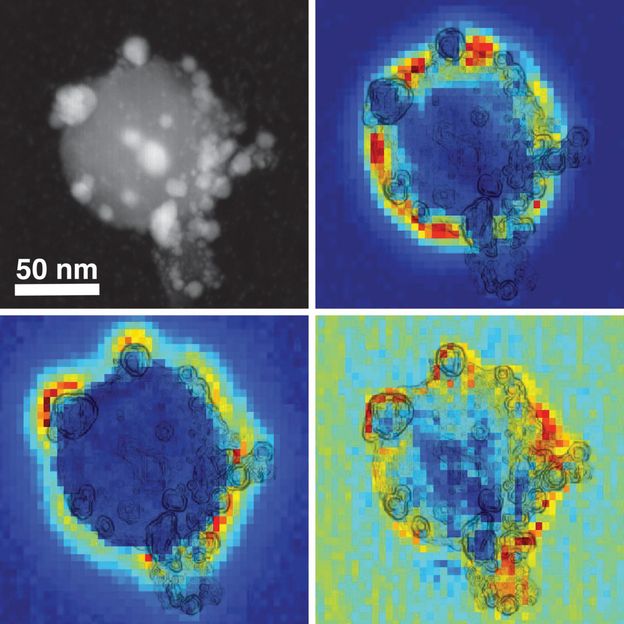
A composite image shows a scanning transmission electron microscope view of an antenna-reactor catalyst particle (top left) along with electron energy loss spectroscopy maps that depict the spatial distribution of individual plasmon modes around the palladium islands. These plasmon modes are responsible for capturing light energy and transferring it to the catalyst particles.
D. Swearer/Rice University
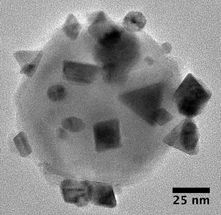
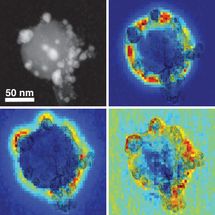
Each year, chemical producers spend billions of dollars on metal catalysts, materials that spur or speed up chemical reactions. Catalysts are used to produce trillions of dollars worth of chemical products. Unfortunately, most catalysts only work at high temperatures or high pressure or both. For example, the U.S. Energy Information Agency estimated that in 2010, just one segment of the U.S. chemical industry, plastic resin production, used almost 1 quadrillion British thermal units of energy, about the same amount of energy contained in 8 billion gallons of gasoline.
Nanotechnology researchers have long been interested in capturing some of the worldwide catalysis market with energy-efficient photonic materials, metallic materials that are tailor-made with atomic precision to harvest energy from sunlight. Unfortunately, the best nanomaterials for harvesting light -- gold, silver and aluminum -- aren't very good catalysts, and the best catalysts -- palladium, platinum and rhodium -- are poor at capturing solar energy.
The new catalyst, which is described in a study in the Proceedings of the National Academy of Sciences, is the latest innovation from LANP, a multidisciplinary, multi-investigator research group headed by photonics pioneer Naomi Halas. Halas, who also directs Rice's Smalley-Curl Institute, said a number of studies in recent years have shown that light-activated "plasmonic" nanoparticles can be used to increase the amount of light absorbed by adjacent dark nanoparticles. Plasmons are waves of electrons that slosh like a fluid across the surface of tiny metallic nanoparticles. Depending upon the frequency of their sloshing, these plasmonic waves can interact with and harvest the energy from passing light.
In summer 2015, Halas and study co-author Peter Nordlander designed an experiment to test whether a plasmonic antenna could be attached to a catalytic reactor particle. Graduate student Dayne Swearer worked with them, Rice materials scientist Emilie Ringe and others at Rice and Princeton University to produce, test and analyze the performance of the "antenna-reactor" design.
Swearer began by synthesizing 100-nanometer-diameter aluminum crystals that, once exposed to air, develop a thin 2- to 4-nanometer-thick coating of aluminum oxide. The oxidized particles were then treated with a palladium salt to initiate a reaction that resulted in small islands of palladium metal forming on the surface of the oxidized particles. The unoxidized aluminum core serves as the plasmonic antenna and the palladium islands as the catalytic reactors.
Swearer said the chemical industry already uses aluminum oxide materials that are dotted with palladium islands to catalyze reactions, but the palladium in those materials must be heated to high temperatures to become an efficient catalyst.
"You need to add energy to improve the catalytic efficiency," he said. "Our catalysts also need energy, but they draw it directly from light and require no additional heating."
One example of a process where the new antenna-reactor catalysts could be used is for reacting acetylene with hydrogen to produce ethylene, Swearer said.
Ethylene is the chemical feedstock for making polyethylene, the world's most common plastic, which is used in thousands of everyday products. Acetylene, a hydrocarbon that's often found in the gas feedstocks that are used at polyethylene plants, damages the catalysts that producers use to convert ethylene to polyethylene. For this reason, acetylene is considered a "catalyst poison" and must be removed from the ethylene feedstock -- often with another catalyst -- before it can cause damage.
One way producers remove acetylene is to add hydrogen gas in the presence of a palladium catalyst to convert the poisonous acetylene into ethylene -- the primary component needed to make polyethylene resin. But this catalytic process also produces another gas, ethane, in addition to ethylene. Chemical producers try to tailor the process to produce as much ethylene and as little ethane possible, but selectivity remains a challenge, Swearer said.
As a proof-of-concept for the new antenna-reactor catalysts, Swearer, Halas and colleagues conducted acetylene conversion tests at LANP and found that the light-driven antenna-reactor catalysts produced a 40-to-1 ratio of ethylene to ethane, a significant improvement in selectivity over thermal catalysis.
Swearer said the potential energy savings and improved efficiency of the new catalysts are likely to capture the attention of chemical producers, even though their plants are not currently designed to use solar-powered catalysts.
"The polyethylene industry produces more than $90 billion of products each year, and our catalysts turn one of the industry's poisons into a valuable commodity," he said.
Halas said she is most excited about the broad potential of the antenna-reactor catalytic technology.
"The antenna-reactor design is modular, which means we can mix and match the materials for both the antenna and the reactor to create a tailored catalyst for a specific reaction," she said. "Because of this flexibility, there are many, many applications where we believe this technology could outperform existing catalysts."