Researchers develop faster, precise silica coating process for quantum dot nanorods
Materials researchers at North Carolina State University have fine-tuned a technique that enables them to apply precisely controlled silica coatings to quantum dot nanorods in a day - up to 21 times faster than previous methods. In addition to saving time, the advance means the quantum dots are less likely to degrade, preserving their advantageous optical properties.
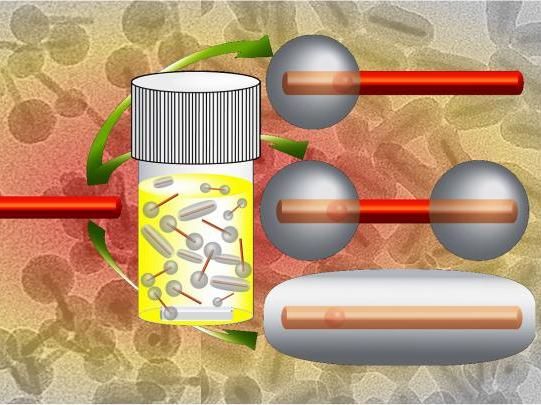
Morphological control of the silica shell on CdSe/CdS core/shell quantum dot nanorods is reported, giving single or double lobes of silica or a uniform silica shell.
Joe Tracy
Quantum dots are nanoscale semiconductor materials whose small size cause them to have electron energy levels that differ from larger-scale versions of the same material. By controlling the size of the quantum dots, researchers can control the relevant energy levels - and those energy levels give quantum dots novel optical properties. These characteristics make quantum dots promising for applications such as opto-electronics and display technologies.
But quantum dots are surrounded by ligands, which are organic molecules that are sensitive to heat. If the ligands are damaged, the optical properties of the quantum dots suffer.
"We wanted to coat the rod-shaped quantum dots with silica to preserve their chemical and optical properties," says Bryan Anderson, a former Ph.D. student at NC State who is lead author of a paper on the work. "However, coating quantum dot nanorods in a precise way poses challenges of its own."
Previous work by other research teams has used water and ammonia in solution to facilitate coating quantum dot nanorods with silica. However, those techniques did not independently control the amounts of water and ammonia used in the process.
By independently controlling the amounts of water and ammonia used, the NC State researchers were able to match or exceed the precision of silica coatings achieved by previous methods. In addition, using their approach, the NC State team was able to complete the entire silica-coating process in a single day - rather than up to one to three weeks needed for other processes.
"The process time is important, because the longer the process takes, the more likely it is that the quantum dot nanorods being coated will degrade," says Joe Tracy, an associate professor of materials science and engineering at NC State and senior author on the paper. "The time factor may also be important when we think about scaling this process up for manufacturing processes."
That said, researchers still have a problem.
The process of applying the silica coating etches the cadmium sulfide surface of the quantum dot nanorods, which shortens the length of the nanorods by as much as four or five nanometers. That shortening is indicative of etching, which reduces the brightness of the light emitted by the quantum dot nanorods.
"We think ammonia may be the culprit," Tracy says. "We have some ideas that we're pursuing, focused on how to substitute another catalyst for ammonia in order to minimize the etching and better preserve the quantum dot nanorod's optical properties."
Original publication
Other news from the department science
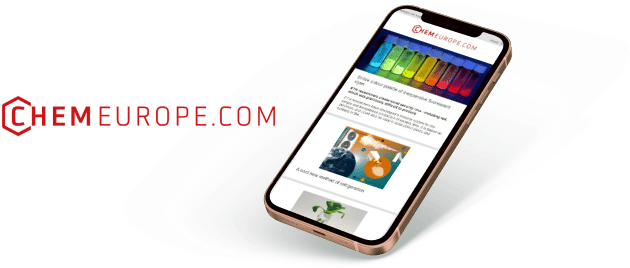
Get the chemical industry in your inbox
By submitting this form you agree that LUMITOS AG will send you the newsletter(s) selected above by email. Your data will not be passed on to third parties. Your data will be stored and processed in accordance with our data protection regulations. LUMITOS may contact you by email for the purpose of advertising or market and opinion surveys. You can revoke your consent at any time without giving reasons to LUMITOS AG, Ernst-Augustin-Str. 2, 12489 Berlin, Germany or by e-mail at revoke@lumitos.com with effect for the future. In addition, each email contains a link to unsubscribe from the corresponding newsletter.