Casting of SiSiC: new perspectives for chemical and plant engineering
Despite its outstanding chemical, thermal and tribological properties, the high costs of production currently prevent the use of silicon-infiltrated SiSiC in many applications. A novel method overcomes technical manufacturing limitations of conventional shaping methods.
Researchers at Fraunhofer IKTS in Dresden developed a process to realize large-scale, complex SiSiC components with differences in wall thickness and demanding undercuts cost-effectively. They adapted the established production process for silicon-filled reaction resin concretes by SICcast Mineralguss GmbH to the ceramic production. Coarse particles mixed with a polymeric binder are casted and cured in one single pressure step into open molds. In this way, cost-intensive material-, machine- and personnel-consuming conventional modular construction and process combinations can be bypassed.
Increased lifetime and productivity, minimized costs
"The efficient manufacturing process allows the substitution of conventional materials in, among others, chemical and plant engineering. By using silicon-infiltrated SiSiC, the lifetime of machines and their productivity can be significantly improved. This presents great potential to increase competitiveness", says Jörg Adler, department head at Fraunhofer IKTS in Dresden.
Radial pump impellers were manufactured as first process application together with SICcast Mineralguss GmbH and Düchting Pumpen GmbH. Such ceramic pumps are primarily applied for processing technically demanding media, such as corrosive chemicals or suspensions highly enriched with abrasive particles at very high temperatures. Other potential applications are nozzles, mills, burners and large-scale structural components for high-precision applications in the optical industry.
Organizations
Other news from the department science
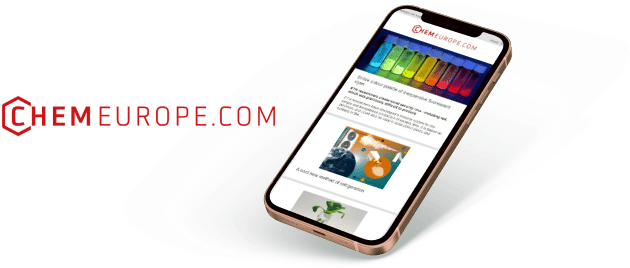
Get the chemical industry in your inbox
By submitting this form you agree that LUMITOS AG will send you the newsletter(s) selected above by email. Your data will not be passed on to third parties. Your data will be stored and processed in accordance with our data protection regulations. LUMITOS may contact you by email for the purpose of advertising or market and opinion surveys. You can revoke your consent at any time without giving reasons to LUMITOS AG, Ernst-Augustin-Str. 2, 12489 Berlin, Germany or by e-mail at revoke@lumitos.com with effect for the future. In addition, each email contains a link to unsubscribe from the corresponding newsletter.