BASF: Fertilizer from Plastic Waste
Environmentally friendly packaging from compostable synthetics
Vegetable waste belongs in the green bin-that has now become an established practice in Germany. Soon, however, the film in which the broccoli was packaged could also go into the compost. Researchers at BASF have developed the world's first food wrap that even acts as a fertilizer. It is made of the fully biodegradable plastic material Ecoflex®.
Films and wrappings made of Ecoflex rot along with the organic waste. In the composting system, microorganisms decompose the plastic refuse and leave only natural residues like water, carbon dioxide and biomass behind. The product is turning out to be a bestseller: In the year 2000, BASF was able to sell three times as much as in 1999.
Microbes decompose the plastic in the field - The Story
Currently, 90 percent of the annual output goes to applications in which renewable raw materials are used in addition to Ecoflex. Usually these involve food packaging, such as cardboard boxes or starch-based containers. If one were to use the natural material by itself in such cases, that would have a big drawback: Fats and liquids would soon penetrate. Coating with Ecoflex provides a remedy and creates a hygienic and completely biodegradable disposable wrapping.
Properties like resistance to water and grease also make it feasible to use pure Ecoflex for trash bags, grocery bags and airtight films. After use, it is no longer necessary to clean the dirty plastic garbage for recycling-which would, of course, require additional energy and therefore impact the environment. Instead, it can be disposed of with the organic waste. This means that municipal districts do not need to adjust existing waste-disposal arrangements, because Ecoflex decomposes in normal composting systems almost as fast as vegetable starch.
Furthermore, it is by no means necessary to take the roundabout route involving organic waste all the time. In agriculture, plastic sheeting is often drawn over entire fields for such purposes as protecting small, fragile lettuce plants from frost. After the harvest, the farmer must then laboriously collect the protective covering again. Thanks to Ecoflex, agricultural sheeting of this kind acquires an entirely new merit as a product: It is simply plowed under and left to decompose in the soil, thereby fertilizing the field.
As it happens, Ecoflex proves to be an adaptable product in regard to manufacturing, too: The new synthetic material can be processed with the same systems that are used for the traditional plastic, polyethylene (PE).
Molecular construction kit modeled on nature - The Background
In the production of Ecoflex, the chemists at BASF combine the constituents adipic acid, butanediol and terephthalic acid to form the finished polymer. The length of the molecular chains along with their branchings and interconnections affects the properties of the biodegradable plastic. This variable composition allows Ecoflex to be used as a molecular construction kit for making customized products. Regardless if they are formed as flexible films or sturdy containers, they are always biodegradable. The fact that the constituents are derived from petrochemicals has no effect on the biodegradability.
In principle, the arrangement of the components in Ecoflex corresponds precisely to that of chemical compounds that occur in nature. For that reason, a multitude of common microorganisms in soil and compost can break down the plastic. They decompose the Ecoflex structure into its original constituents and use them in the creation of natural metabolic products. As a result, after only three months in the composting system, water, carbon dioxide and biomass are all that is left of the synthetic material.
Most read news
Other news from the department science
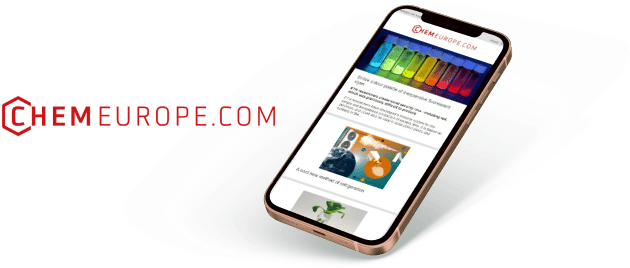
Get the chemical industry in your inbox
By submitting this form you agree that LUMITOS AG will send you the newsletter(s) selected above by email. Your data will not be passed on to third parties. Your data will be stored and processed in accordance with our data protection regulations. LUMITOS may contact you by email for the purpose of advertising or market and opinion surveys. You can revoke your consent at any time without giving reasons to LUMITOS AG, Ernst-Augustin-Str. 2, 12489 Berlin, Germany or by e-mail at revoke@lumitos.com with effect for the future. In addition, each email contains a link to unsubscribe from the corresponding newsletter.