Climate killer as a climate rescuer
Surplus electrical power converts carbon dioxide into synthetic natural gas
When clouds cloak the sun, the production of solar power drops abruptly. When the wind lulls, wind parks quit producing energy. On the other hand, there are days on which wind power stations must be shut down because there is too much electricity in the grid. The “iC4” project funded by the German Federal Ministry for Education and Research (BMBF) aims to optimize the conversion of carbon dioxide into synthetic natural gas – a process that has been known for over 100 years – to make the process economically viable. First successes have now been made.
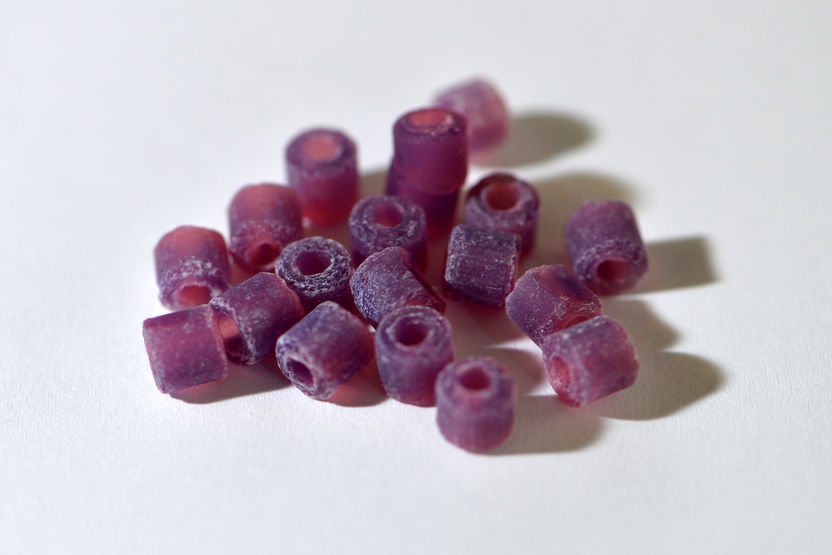
Cobalt containing catalyst for the conversion of carbon dioxide into methane.
Andreas Battenberg / TUM
The much-scolded “greenhouse gas” carbon dioxide could become a cornerstone of the German energy policy turnaround: Scientists at the Technische Universitaet Muenchen (TUM), in collaboration with researchers from Wacker Chemie AG and Clariant AG, are developing efficient catalytic converters to transform carbon dioxide into methane. The hydrogen needed for the reaction is produced through electrolysis using surplus electrical energy.
In the context of the BMBF-funded project iC4 (Integrated Carbon Capture, Conversion and Cycling), the scientists tested more than 250 different catalyst systems, ranging from commercially available systems to catalysts newly developed within the project. The most promising candidates are being optimized further.
At a pilot facility of MAN Diesel & Turbo at the Deggendorf site, the best catalysts to date achieve yields between 92 and more than 95 percent, enough methane to feed the gas into the natural gas pipelines. But the main focus of the research is to explore the exact course of the reaction and the reactions taking place on the surfaces of the catalysts. "This knowledge is the key to economic methane production in an industrial scale," says Prof. Bernhard Rieger, head of the Wacker-Chair of Macromolecular Chemistry at the Technische Universitaet Muenchen and Spokesman of iC4 consortium.
Synthetic natural gas as an energy store
“We can neither produce enough batteries, nor build as many pumped-storage power plants as would be required to bridge the gap between produced and consumed electrical power,” says Professor Rieger. “The only way to stockpile such immense amounts of energy is via chemical storage.”
To the researchers, methane is a particularly valuable form of storage since Germany already has an extensive distribution network and storage capacities sufficient to bridge a supply interruption of several weeks. In addition, there are decades of experience using natural gas as a fuel in automobiles.
The raw material, carbon dioxide, is also abundantly available: In addition to its energy carrier, methane, natural gas comprises up to 10 percent carbon dioxide. Biogas plants generate up to 50 percent carbon dioxide alongside methane. However, the largest source of carbon dioxide lies in coal, oil and gas fired power plants and energy intensive processes as the production of cement or metal production.
Large-scale technical implementation
A key challenge to tapping these sources of carbon dioxide lies in the purity of the gas. Flue gasses contain aggressive sulphur dioxide. Biogas often also contains sulphur compounds. An optimal catalyst should be able to handle these kinds of interfering substances to keep down the cost of carbon dioxide purification. In their search for robust and even more active catalytic converter systems, the researchers at TU Muenchen are now investigating the interactions between various catalytically active metals and substrate materials, as well as the influence different methods of preparation have on both stability and activity.
A further challenge is the multi-stage reaction itself, which releases large amounts of energy. “Although we already have the first demonstration plants for methane production, the reaction kinetics of the various reaction stages are not yet fully understood,” says Professor Rieger. An important aim of the research work is, thus, theoretically modeling all reaction steps at the computer. Such model calculations are an important basis for the development of efficient large-scale plants.
The joint project for the use of carbon dioxide as an energy store stands on four columns: the separation of carbon dioxide from natural gas and biogas, the separation of carbon dioxide from exhaust gasses (power stations, cement industry, …), the catalytic conversion of carbon dioxide to methane, and the direct use of carbon dioxide via photocatalysis. With companies like Clariant AG, e.on AG, Linde AG, MAN Diesel & Turbo SE, Siemens AG and Wacker Chemie AG, as well as the Fraunhofer Institute of of Interfacial Engineering and Biotechnology and TU Muenchen, the iC4 consortium bundles the competency required in all value-creation steps. The project is funded by the German Federal Ministry for Education and Research (BMBF).