Faster X-ray technology paves the way for better catalysts
Researchers observe a catalyst surface at work with atomic resolution
By using a novel X-ray technique, researchers have observed a catalyst surface at work in real time and were able to resolve its atomic structure in detail. The new technique, pioneered at DESY's X-ray light source PETRA III, may pave the way for the design of better catalysts and other materials on the atomic level. It greatly speeds up the determination of atomic surface structures and enables live recordings of surface reactions like catalysis, corrosion and growth processes with a time resolution of less than a second. "We can now investigate surface processes that were not observable in real time before and that play a central role in many fields of materials science," explains DESY researcher Prof. Andreas Stierle. The Swedish-German research team around lead author Dr. Johan Gustafson of Lund University present their work in the US journal Science.
Materials scientists currently lack a method to record data of the full atomic structure of surfaces during dynamic processes within a reasonable time. Existing methods are either too slow or require ultra high vacuum, prohibiting the flow of gas in the test chamber and thus ruling out a live investigation of dynamic reaction processes involving gas phases at near atmospheric pressures.
"Our goal was to observe surfaces under reactive, application-oriented conditions in real time," says Stierle. The team used the high-energy X-rays from DESY's light source PETRA III. When X-rays strike a solid material, they are diffracted into a characteristic pattern that yields information about the atomic structure of the material. In conventional X-ray measurements performed at lower photon energies, the sample and the detector must be rotated to map out the full diffraction pattern painstakingly step by step, a procedure that can easily consume ten hours or more.
In contrast, the high-energy X-rays of PETRA III are scattered into a much smaller angular range, producing a much more compact diffraction pattern that can be recorded at once with a high-end two-dimensional detector at the High Energy Materials Science measuring station P07. "This approach makes it possible to record data 10 to 100 times faster," explains Stierle. As a consequence, scientists can gain a full surface structure in less than ten minutes or track individual structural features with a temporal resolution of less than a second. "It also allows us to more easily identify unknown or unexpected structures," underlines Stierle.
For their investigations, the researchers installed a test chamber, in which the gas pressure can be up to 1 bar — the same as normal atmospheric pressure — to approach realistic reaction conditions. A mass spectrometer allows for on-line monitoring of the gas distribution within the test chamber during measurements.
To demonstrate the new approach, the researchers watched a catalyst of the precious metal palladium live at work: a two millimetre thick palladium single crystal with a diameter of one centimetre converts toxic carbon monoxide into harmless carbon dioxide, much like catalytic converters do in cars. The technique enabled the scientists to observe how the palladium began to convert the carbon monoxide (CO) into carbon dioxide (CO2) as soon as oxygen (O2) also flowed into the chamber. "We can watch how the catalyst switches from a non-reactive state into a reactive one," explains Stierle who heads the NanoLab at DESY and also holds an appointment as professor at the University of Hamburg.
The researchers hope to identify the catalyst's active phase by using this new approach. For decades, scientists have debated whether the conversion of carbon monoxide into carbon dioxide, for example, takes place on the bare metallic surface, on an oxide layer, or on oxide islands on the surface. "The new technology gives us the opportunity to identify the reaction centres in real time at atomic resolution," says Stierle.
In the end, the findings could be used to optimise catalysts. In general, catalysts are substances that accelerate chemical reactions without being consumed by them. The new X-ray technique has a wide variety of applications for materials research. The scientists expect completely new insights into the kinetics of surface processes, enabling the design of new materials on the atomic level. "The combination of the extremely bright X-ray source, the sample environment and the 2D detector at PETRA III is worldwide unique," emphasises Stierle.
Other news from the department science
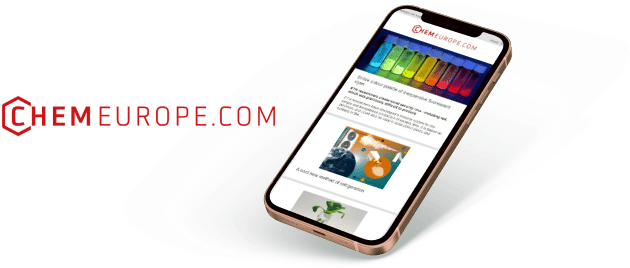
Get the chemical industry in your inbox
By submitting this form you agree that LUMITOS AG will send you the newsletter(s) selected above by email. Your data will not be passed on to third parties. Your data will be stored and processed in accordance with our data protection regulations. LUMITOS may contact you by email for the purpose of advertising or market and opinion surveys. You can revoke your consent at any time without giving reasons to LUMITOS AG, Ernst-Augustin-Str. 2, 12489 Berlin, Germany or by e-mail at revoke@lumitos.com with effect for the future. In addition, each email contains a link to unsubscribe from the corresponding newsletter.