Power Supply Systems for Deep Sea Factories
Siemens is developing power technology for deep sea factories. These self-sufficient oil and gas extraction facilities should one day exploit raw material deposits on the seafloor. Located thousands of meters under water, the factories must operate reliably for several decades. However, there is still no empirical data about the high water pressure's long-term effects on transformers and other network components. As reported in "Pictures of the Future", Siemens is testing components for deep sea facilities in a special pressure chamber in Trondheim, Norway. Beginning in 2020, the Norwegian energy company Statoil plans to build oil and gas extraction facilities deep under water.
Subsea facilities are currently only set up in relatively shallow waters. In these systems, power cables and pipes connect pumps that are distributed across the seafloor to a floating platform. This technology can be used to extract about 40 percent of a raw material reservoir. However, self-sufficient deep sea factories could increase the rate to 60 percent. These factories pump oil or gas directly out of the wells and compress the gas before transporting it to the surface. The facilities' power supply units (transformers, frequency converters, and switchgear) are also under water, where they provide the correct voltage. As a result, they can supply power to more pumps than surface systems. The only connections between the deep sea and the surface are a pipeline and an electricity and data cable.
The Siemens research center near Trondheim is ensuring the reliability of the deep sea power network by putting the components into a pressure chamber, where they have to withstand up to 460 bars for several months. This pressure is equivalent to the pressure found 4,600 meters under water. The researchers put the individual components into oil-filled pipes that are then placed inside the pressure chamber. The completed facilities will also be filled with oil instead of being installed into conventional air-filled housings. The oil offsets the high pressure and has better cooling and electrical insulation properties than air, allowing the deep sea facilities to be more compact than would otherwise be the case. Special aging tests ensure that the parts will last for at least 20 years. Only components that pass all of the tests and the subsequent inspection are installed into the electricity network components.
Siemens has already assembled the first deep sea transformer in Trondheim. A switchgear system will be completed by the end of the year, and a frequency converter is scheduled to be finished by the end of 2014.
Most read news
Other news from the department science
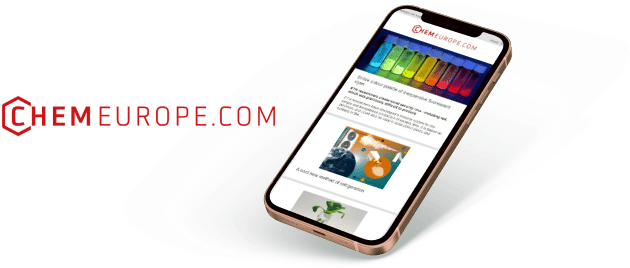
Get the chemical industry in your inbox
By submitting this form you agree that LUMITOS AG will send you the newsletter(s) selected above by email. Your data will not be passed on to third parties. Your data will be stored and processed in accordance with our data protection regulations. LUMITOS may contact you by email for the purpose of advertising or market and opinion surveys. You can revoke your consent at any time without giving reasons to LUMITOS AG, Ernst-Augustin-Str. 2, 12489 Berlin, Germany or by e-mail at revoke@lumitos.com with effect for the future. In addition, each email contains a link to unsubscribe from the corresponding newsletter.