Disorder creates rust protection
A material’s nanostructure is decisive in determining how resistant it is against corrosion
corrosion eats away 75 billion euros of economic output annually in Germany alone. But it may soon be possible to better assess which steels and other alloys will be affected, and how to limit the damage: An international team led by scientists from the Max-Planck-Institut für Eisenforschung GmbH in Düsseldorf analysed an amorphous steel comprising iron, chromium, molybdenum, boron and carbon. They found that the more ordered a material’s structure is, and the more uneven the distribution of its atoms, the more easily it is corroded by rust. If the elements of the alloy don’t form a regular crystal lattice and are distributed completely uniformly across the material, then, under corrosive conditions, a passivation layer forms on its surface and protects it from rusting. If, in contrast, ordered nanocrystals form that sometimes contain more chromium and sometimes more molybdenum, the corrosion quickly eats away the material because no protective passivation layer forms. These findings give materials scientists clues as to what they should pay attention to regarding the composition and production of materials.
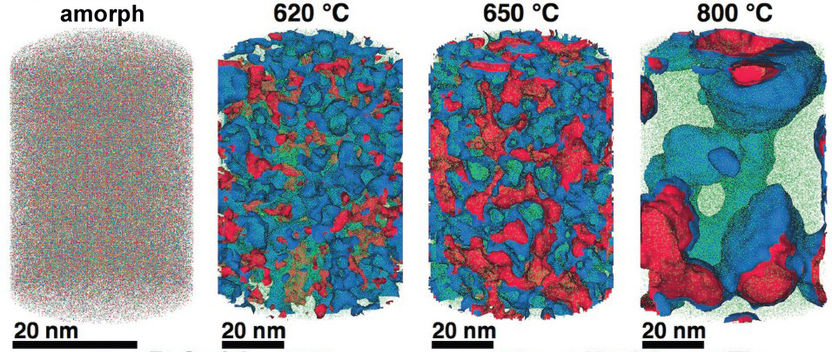
A steel in the tomograph: Just how the elements in a compound are distributed can be determined with atomic precision using an atom probe. This allows materials researchers in Düsseldorf to understand how the nanostructure of a model alloy comprising iron (green), chromium (blue), molybdenum (red), carbon and boron (for clarity, carbon and boron are not shown) depends on the temperature to which it was previously exposed. In the amorphous material (left) with a disordered structure, the elements are distributed completely uniformly. In the samples that were treated at 620 and 650 degrees, the elements gradually separate, creating different regions that each contain more iron, chromium or molybdenum than corresponds to the chemical composition. In the process, crystalline structures increasingly form. A sample treated at 800 degrees Celsius is completely crystalline, and the different areas can be up to 50 nanometres in size. As the researchers established in further studies, the nanostructure strongly influences the material’s corrosion resistance.
© Science/MPI für Eisenforschung
In humid air, chemistry gnaws at every metal, unless it happens to be gold or another precious metal. But oxygen in the air is only too happy to hook up with the less precious representatives of this class of materials. Humidity helps it in its search for a partner, and all the more so the saltier it is. At the outset of a corrosive attack, some metals, such as chromium and zinc, become coated with a dense oxide layer that prevents further advances on the part of the oxygen. If no such passivation layer forms, the metal corrodes, leaving behind a porous and brittle surface that causes a car body or a ship’s hull to gradually crumble. This is how corrosion destroys up to 4 percent of the economic output of the industrialised nations every year.
“Our findings explain why some materials are particularly susceptible to corrosion despite having the exact same composition as corrosion-resistant steels,” says Frank Renner, who headed the study at the Max-Planck-Institut für Eisenforschung GmbH and is now a professor at Hasselt University in Belgium. It is still difficult to say anything about the corrosion resistance of alloys that are currently used in automotive manufacturing, shipbuilding and plant construction. These materials have numerous components. How resistant they are to corrosion depends not only on their composition, but also on how the material was processed and what temperature it is exposed to in use, for instance in a power plant turbine.
A model for the transition from amorphous to crystalline steel
The team of Max Planck researchers has now comprehensively investigated for the first time how the micro- or nanostructure of an alloy that chemists describe using the formula Fe50Cr15Mo14C15B6 influences its corrosion resistance. This alloy is one of the amorphous steels that are used, for example, as abrasion-resistant coatings. The elements in it are present in an irregular structure, but they are distributed completely uniformly in the material. “We are interested in the alloy primarily as a model system in which we can study the transition from the amorphous form to the crystalline form,” says Frank Renner. Since it’s similar to common chromium-molybdenum steels, the researchers’ findings are also relevant for materials used in actual practice. The researchers’ test alloy does, however, contain significantly more carbon than common steels, and also the high boron content is rather unusual for steels from the blast furnace. However, this was the mixture that allowed the team to produce the amorphous variant of the alloy.
The amorphous form of the alloy marked the starting point of a series of measurements that led, via multiple intermediate stages, to the ordered crystalline form. The extent to which the alloy crystallises depends on the temperature at which the researchers bake the elements together: the material remains amorphous at 550 degrees Celsius, while it takes on the completely crystalline form at 800 degrees. The scientists obtained the intermediate stages at 620 to 670 degrees Celsius.
The team used atom probe tomography to reveal the nanostructures of their steel varieties. In this process, the atoms of a sample are evaporated one by one and collected by a detector. The element can be deduced from the time it takes an atom to reach the detector, and its position in the probe from the point of impact. This allowed the researchers to obtain precise maps of the materials, and the maps helped them understand how the atoms regroup with increasing manufacturing temperature. “Different regions form, in each of which one of the metals is concentrated,” explains Jazmin Duarte, who carried out these studies. The sample that the materials scientists produced at 620 degrees Celsius remains largely disordered. “But crystalline structures can already be seen in this sample, too,” says Jazmin Duarte. “In contrast, the form produced at 800 degrees is completely crystalline, with each of the regions extending up to 50 nanometres only.”
Chromium resists corrosion the longest
The researchers now compared the precise information about the nanostructure of the steel variants with electrochemical measurements to assess how easily the various forms fall victim to corrosion. To do this, they wetted the sample surfaces with a saline solution and applied an electrical voltage to the alloy. The higher the voltages a sample withstands in the lab without corroding, the more resistance it shows to the rust attack in practice, too. “The completely amorphous and the largely amorphous forms proved to be almost as resistant as pure chromium,” explains Julia Klemm, who performed the relevant experiments. Under normal conditions, corrosion stands little chance against chromium, because it is sealed by a thin passivation oxide layer. Such a protective layer also forms on the amorphous steels. In the largely crystalline forms of the alloy, however, that is app+arently no longer possible. Here, the rust already eats holes in the sample at relatively low voltages.
To learn more about the destructive work of corrosion, the team additionally analysed which elements are released from the material at which voltages. For this, they used a method that Karl Mayrhofer developed at the Düsseldorf-based Max Planck Institute: they placed a plastic cell with an opening on their sample. Tubes lead into such a cell from two sides, allowing the researchers to have a saline solution flow onto their sample on the one side, and be collected again on the other side. They evaporate the effluent solution with a plasma beam and determine its ion content in a mass spectrometer.
“According to our measurements, at low voltages, especially iron and molybdenum leak out of the amorphous sample,” says Julia Klemm. Hence, the chromium is left and forms an impenetrable protective layer on the entire material. However, as the voltage increases, more and more chromium is dissolved, while the proportion//ratio of dissolved iron and molybdenum remains the same or even decreases. A similar thing happens in the partially crystalline sample. In the completely crystalline sample, in contrast, molybdenum-rich areas corrode noticeably faster with increasing voltage, while chromium-rich areas remain stable over a larger voltage range. In other words, in the crystalline material, the rust spares the chromium-rich areas, and a sponge-like material remains.
Corrosion creates a porous material for filters or catalysts
“It was rather by chance that we discovered that our model alloy makes it possible to electrochemically produce porous structures of the very hard compound of iron, chromium and carbon,” says Frank Renner. “Due to their very large surface, they could be suitable as membranes for filters or substrate materials for catalysts.” After all, the larger their active surface is, the better both filters and catalysts perform.
For car bodies, aircraft fuselages or turbine blades, on the other hand, a crystalline chromium-molybdenum steel perforated by rust is useless. The researchers can also explain why no protective passivation layer develops on the crystalline forms of the alloy. Since the corrosion protection is based primarily on the chromium and its oxide layer, the entire material remains protected only when there is sufficient chromium. If the chromium accumulates in individual areas that lie relatively far apart from one another, then only these regions will be protected.
The connection between chromium distribution and corrosion protection also gives the materials scientists a clue as to why amorphous steels are already corrosion resistant with a chromium content of 4 to 5 percent, while crystalline steels require 12 to 13 percent: the latter must contain more chromium overall so that there will be enough also in the chromium-depleted crystallites to form the passivation layer over the entire material.
The researchers in Düsseldorf aren’t yet able to provide clear instructions for making industrial steels more resistant to rust. “But our study shows that already the separation in the nanometre range strongly influences how corrosion resistant a material is,” says Frank Renner. Thus, the fact that all components in a material should be distributed as uniformly as possible to avoid rust corrosion could provide a clue for practical materials science.