75 years of Perlon: from ladies' hosiery to tough hawsers for ships
The synthetic material discovered by Paul Schlack 75 years ago on January 29, 1938, still has a very diverse range of applications. The fiber first made its name through its use in Perlon stockings in the 1950s. Today, however, it no longer adorns women's legs but is instead used as a strong plastic filament in tough hawsers for ships, fishing lines, field fencing and lines for oyster baskets. In addition to Perlon, this range of high-quality plastics also includes the Bayco and Atlas brands and is manufactured by Perlon-Monofil GmbH, a subsidiary of company LANXESS.
It is impossible to imagine life now without these extremely high-performance plastic fibers, or monofilaments. Perlon-Monofil develops and produces more than 60 million kilometers of monofilaments per year. That is about the same as the distance from Earth to Mars. Among other things, the monofilaments are used in industrial fabrics, paper machine clothing, trellises and staple wires for wine and fruit growing, and fishing lines for sports fishing.
Giants of the seas held fast with hawsers from Perlon-Monofil
The high-tech plastic from the LANXESS subsidiary is also important in the production of ships' hawsers. All over the world, these hawsers have been securing tankers and container ships to dry land for almost 50 years. Each year, LANXESS produces around 27,000 kilometers of monofilament for use in the shipping industry. The plastic filaments are then combined with an additional special fiber and made into Atlas brand ropes at three plants in Germany, Belgium and South Korea. Approximately 360 kilometers of ropes and cables are produced per year, ranging from 20 to 95 millimeters in thickness. The strength of the fibers is proven by the load tests – the strongest rope must withstand a tensile force of 190 metric tons. Other test criteria include resistance to sea water, buoyancy, strength and flexibility.
Innovative, sustainable oyster farming
However, plastic filaments from Perlon-Monofil also play a very different role in the marine environment, with the monofilaments from Germany helping oyster farmers in Australia. The oysters grow in baskets attached to plastic lines “made in Dormagen”. These lines are used to pull the baskets up to the surface of the water and then lower them again, so that the oysters can be cleaned and their growth monitored. This method is proven to put less of a strain on the delicate maritime ecosystem. In contrast, oyster farms where the oysters are cultivated on the seabed require young oysters to be placed upon a suitable substrate. Once they have grown to the required size for sale, they are collected in dredging nets. The disadvantage of this is that the nets can cause significant damage to the seabed and the flora and fauna that live there. The nets can also trap unwanted bycatch.
For better connections
Monofilaments have also made their mark in the communications and electrical engineering sectors. The flexibility of these monofilaments, coupled with their diameter accuracy, tensile strength and durability, makes pulling wires manufactured under the brand names Atlas and Bayco dependable and robust tools for industry and craftsmen alike. Special UV-, heat- or weather-resistant monofilaments satisfy a variety of requirements in industrial applications.
Most read news
Other news from the department research and development
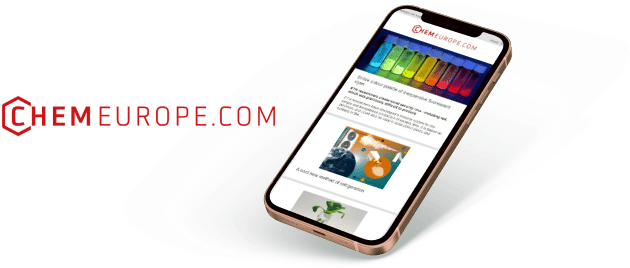
Get the chemical industry in your inbox
By submitting this form you agree that LUMITOS AG will send you the newsletter(s) selected above by email. Your data will not be passed on to third parties. Your data will be stored and processed in accordance with our data protection regulations. LUMITOS may contact you by email for the purpose of advertising or market and opinion surveys. You can revoke your consent at any time without giving reasons to LUMITOS AG, Ernst-Augustin-Str. 2, 12489 Berlin, Germany or by e-mail at revoke@lumitos.com with effect for the future. In addition, each email contains a link to unsubscribe from the corresponding newsletter.