The solar industry could gain sizeable cost advantages by using the right lasers
Contactless and material-selective laser processes are of critical importance for the production of sensitive electronic components such as solar cells. lasers can achieve a decisive step to greater efficiencies and lower manufacturing costs for crystalline and thin-film photovoltaics. With this goal in mind, the Fraunhofer Institute for Laser Technology ILT is developing industrial-scale processes, e.g. for the high-resolution structuring of thin layers, along with corresponding mechanical components to raise production throughput rates. Selecting the most suitable laser to optimize such processes plays a predominant role in these research activities.
Competitive process engineering for the production of electronic components calls for high speeds, small structure sizes, and large-scale applicability. In organic electronics, structured printing currently allows feature sizes as small as 10 micrometers at high speeds. A significantly higher resolution and productivity can be obtained with structuring by laser. Especially important here is choosing a laser that is ideally suited to the requirements of the particular application. “Most companies in the solar industry don’t know how much time and costs they can save by using the right laser for manufacturing thin-film solar modules or crystalline solar cells,” explains Dr. Malte Schulz-Ruthenberg, project manager at Fraunhofer ILT. “For example, completely different beam guiding and shaping approaches are required for high-speed drilling of back-contact solar cells than those used to create complex structures on electronic circuits at high processing rates .”
Series connection for rigid and flexible solar modules
In addition to machine technology, one focus of research at Fraunhofer ILT is on further developing structuring processes for thin-film solar modules. These modules require small strips of cells connected in series in order to reduce current densities, which in turn reduces electrical losses within the module. What many companies are still carrying out by means of mechanical scribing can be done quicker and more cleanly by means of laser radiation. The challenge ILT researchers now face is to do this without impairing the functionality of the layers of conducting, semi-conducting, or insulating materials, which have thicknesses ranging from a few nanometers to a few micrometers. If, for example, residues of ablated material or thermal damage to neighboring areas occur during processing, the extreme thinness of these layers can lead to their degradation and cause the entire solar module not to work. The laser structuring processes therefore have to be adapted to the different characteristics of each individual layer. Ultrashort pulse lasers can be used for physical processes that are not feasible at longer pulse durations. This opens up new process windows, and paves the way towards new industrial-scale processes.
In the FlexLas project a laser structuring technique for organic solar cells on flexible film substrates is being developed at Fraunhofer ILT. This type of solar module is considered an economical, forward-looking product in the field of solar energy. It might well be possible one day to make textiles or handbags with flexible solar cells, which could be used to charge a cell phone. The laser structuring processes being developed in Aachen can also be applied to other products with multiple-layer systems, such as smart phone screens and flat lighting elements.
Other news from the department science
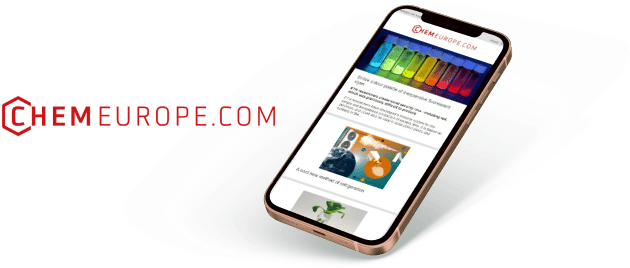
Get the chemical industry in your inbox
By submitting this form you agree that LUMITOS AG will send you the newsletter(s) selected above by email. Your data will not be passed on to third parties. Your data will be stored and processed in accordance with our data protection regulations. LUMITOS may contact you by email for the purpose of advertising or market and opinion surveys. You can revoke your consent at any time without giving reasons to LUMITOS AG, Ernst-Augustin-Str. 2, 12489 Berlin, Germany or by e-mail at revoke@lumitos.com with effect for the future. In addition, each email contains a link to unsubscribe from the corresponding newsletter.