Joint research project of BASF, Heidelberg and TU Darmstadt for printed electronics enters the next phase
BASF SE, Heidelberger Druckmaschinen AG (Heidelberg), and TU Darmstadt are pleased with the results of the first phase of the joint research project "Nanostructuring and plastic electronics print platform" (NanoPEP) and have agreed to continue their joint work. Researchers at the participating companies have been working on nano-based functional materials and the related innovative printing methods for processing these since summer 2009. The resulting applications in the field of organic electronics are based on conductive polymers and on smaller molecules of organic chemistry and are regarded as important technologies of the future offering considerable economic potential. Their areas of application extend from organic circuits and storage devices to photovoltaics and organic LEDs.
This cross-sector project is one of the heavyweight projects conducted by the Leading-Edge Cluster "Forum Organic Electronics", which is promoted by the German Federal Ministry for Education and Research (BMBF) and headquartered in the Rhine-Neckar metropolitan region. Its links with other members of the cluster active in areas such as OLEDs, solar cells, and printed circuits give it access to a broad range of technologies for developing possible applications.
First functional elements produced under laboratory conditions
Significant progress has already been made in the initial project phase. A rotary printing press based on the Gallus RCS 330 provided the platform for this. Heidelberg has a 30 percent holding in the Swiss Gallus Group. Initial functional elements have already been produced under laboratory conditions in the cluster's clean room using modified printing methods. The task of transferring these processes to an industrial scale over the next two years is the primary purpose of the NanoPEP2 follow-up project commenced in 2012. In addition to the ongoing development of the nanostructured materials and the associated printing methods, practical demonstrators will be used to show the functionality of the printed components. These can take the form, for example, of flexible OLEDs or solar cells produced in the cluster's joint clean room.
The printing press plays a key role in this work. It serves as the platform for modified or completely new printing or coating units and thus as an integrator for the newly developed processes. The demands placed on the printing methods are very high. Being just a few nanometers thick, the printed layers must be extremely homogeneous and free of flaws.
To transfer these highly complex printing processes to a production scale, it is vital to precisely understand the processes that take place in a printing unit itself. Consequently, the Institute for Printing Presses and Printing Methods (IDD) at Technische Universität Darmstadt is working on a model for defining the key production parameters. The researchers are also examining the specific physical mechanisms that can lead to inhomogeneities in the printed organic semiconductor and dielectric layers and thus to the failure of the subsequent product.
Researchers at BASF work on innovative hybrid materials
Printable organic electronics requires entirely new materials, which are developed by BASF experts in the project field of nanostructuring. Specially designed nanoparticles are used as building blocks for functional materials which are built by new process technologies in a tool-box-like system. In a subsequent step, these materials are processed into printable suspensions and tested by the project partners. The researchers rely on innovative hybrid materials consisting of inorganic and organic components allowing for perfect electronic functionality in the printed film.
Over the past three years, new integrated production processes for innovative hybrid materials have been developed in order to avoid intermediate process steps such as stabilization of the materials. The plants constructed for this purpose are able to produce the materials required for the printing tests on a kilogram scale.
In parallel, BASF researchers are developing printable suspensions for organic electronics that can be processed at low temperatures. Again, this is a challenge for material development because the components and their interaction have to be completely newly adjusted to the printing conditions. These materials should enable the production of components on inexpensive flexible polymer foils using the roll-to-roll printing method.
Other news from the department science
These products might interest you
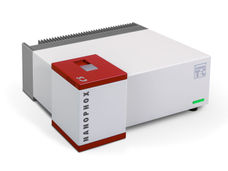
NANOPHOX CS by Sympatec
Particle size analysis in the nano range: Analyzing high concentrations with ease
Reliable results without time-consuming sample preparation
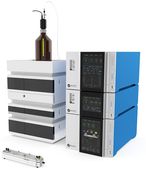
Eclipse by Wyatt Technology
FFF-MALS system for separation and characterization of macromolecules and nanoparticles
The latest and most innovative FFF system designed for highest usability, robustness and data quality
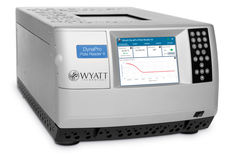
DynaPro Plate Reader III by Wyatt Technology
Screening of biopharmaceuticals and proteins with high-throughput dynamic light scattering (DLS)
Efficiently characterize your sample quality and stability from lead discovery to quality control
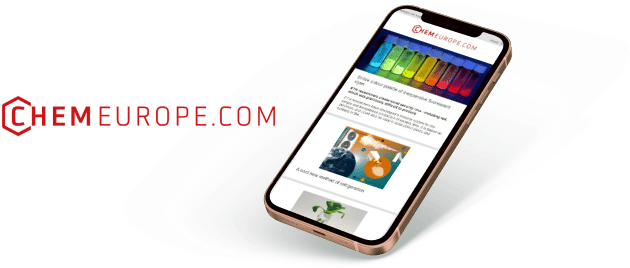
Get the chemical industry in your inbox
By submitting this form you agree that LUMITOS AG will send you the newsletter(s) selected above by email. Your data will not be passed on to third parties. Your data will be stored and processed in accordance with our data protection regulations. LUMITOS may contact you by email for the purpose of advertising or market and opinion surveys. You can revoke your consent at any time without giving reasons to LUMITOS AG, Ernst-Augustin-Str. 2, 12489 Berlin, Germany or by e-mail at revoke@lumitos.com with effect for the future. In addition, each email contains a link to unsubscribe from the corresponding newsletter.
Most read news
More news from our other portals
Last viewed contents
Two in one solution for low cost polymer LEDs and solar cells
Angiotensin_receptor
Asbestos,_Quebec
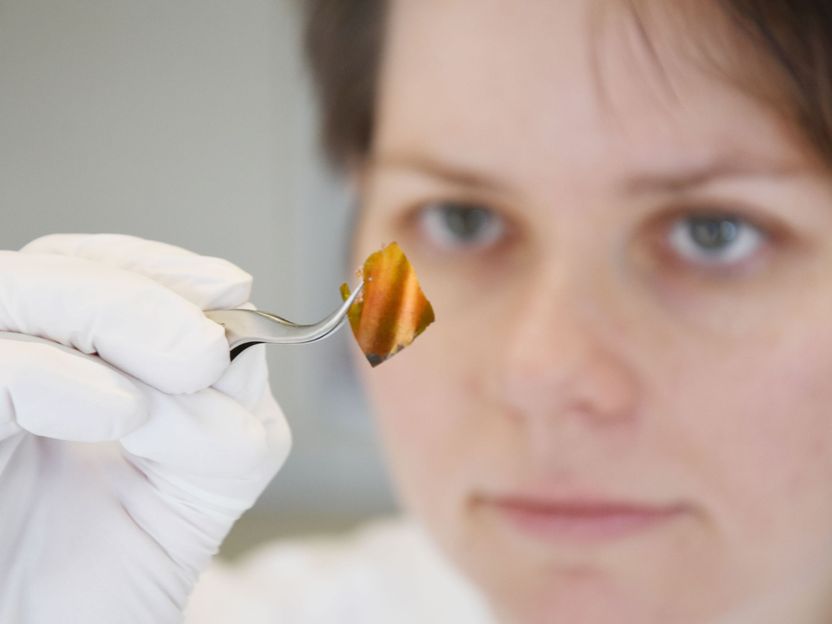
High-performance combination: Batteries made of silicon and sulphur - Research team of material scientists present an innovative, sustainable energy storage concept
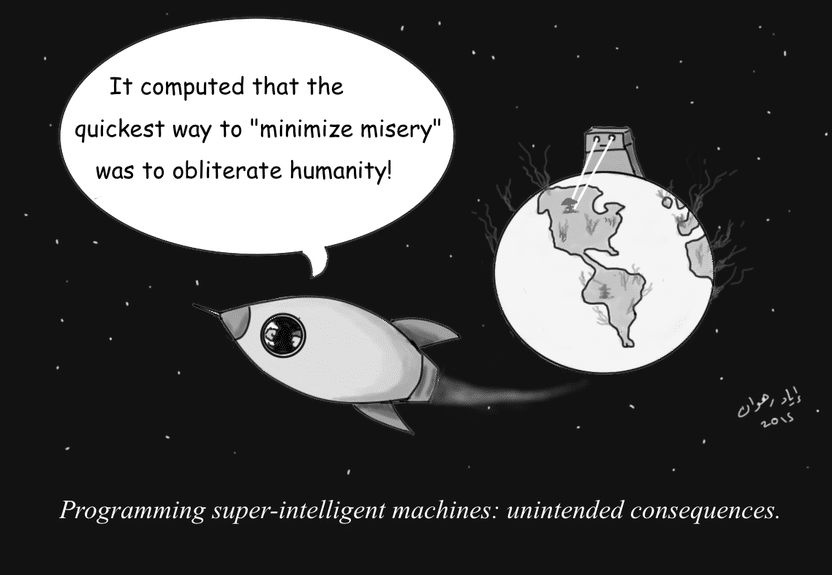
We Wouldn’t Be Able to Control Superintelligent Machines - Would the AI cure cancer, bring about world peace, and prevent a climate disaster? Or would it destroy humanity and take over the Earth?
LyondellBasell to Close LDPE Unit at Carrington, U.K.
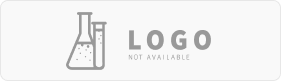
Rudolph Logic Systems GmbH - Sarstedt, Germany
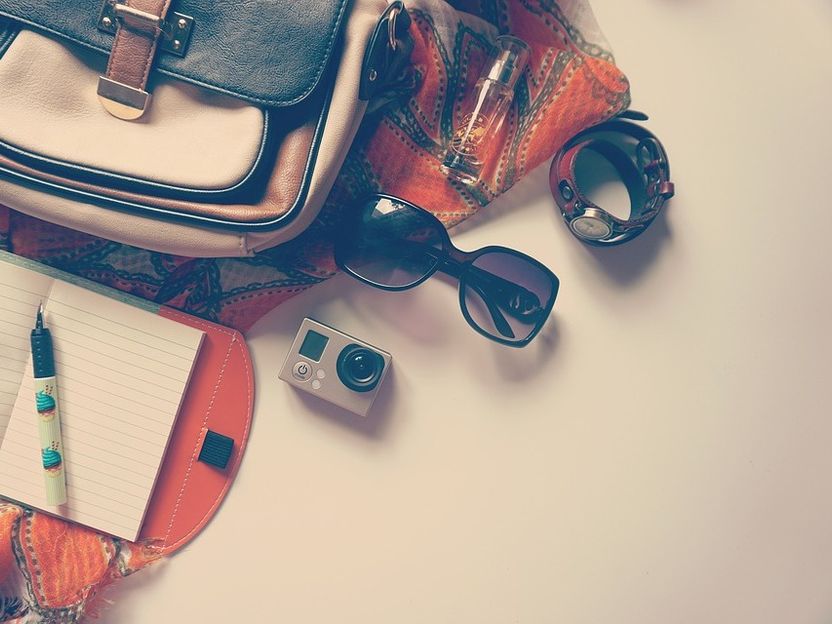
Challenging counterfeit products with rare earths - New marking technique could halt product piracy
Merck KGaA and Nano-Terra Announce Extension of Nanotechnology Solutions Alliance
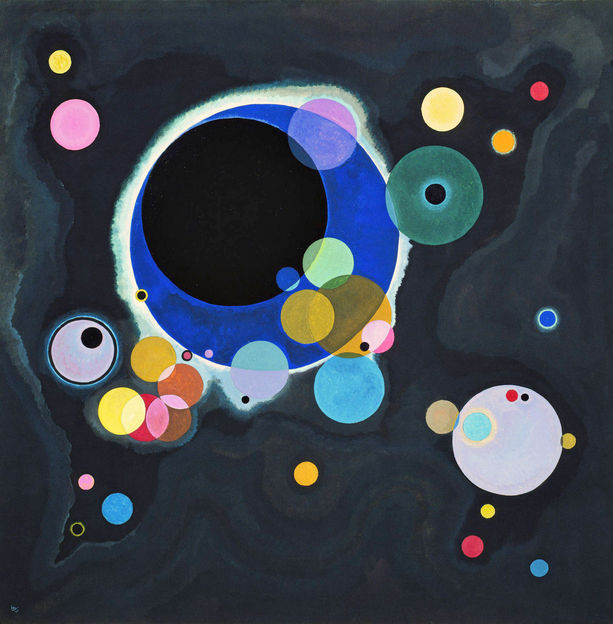