Cheap and Cheerful: Iron to Replace Palladium
Scientists Develop Alternative Catalyst for Polyethylene Production
precious metals are expensive and in demand, not just for jewellery or as a financial investment, but also in industry. Here, valuable metals are used, among other things, as catalysts in chemical reactions. For example, palladium is crucial in a decisive step in the production of polyethylene, the material from which, among other things, plastic bags are manufactured. In search of cheaper alternatives, scientists from Jülich, Dresden, Berlin, Munich and Budapest have developed a catalyst made from iron and aluminium, which works just as well as palladium but is much cheaper.
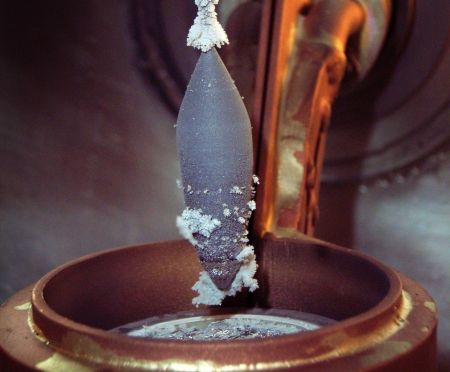
An alternative to precious metals: Czochralski single crystals of an iron-aluminium compound. These crystals have been found to catalyse an important step in the synthesis of the production of polyethylene. Until now, a material containing palladium has been used in industry.
Forschungszentrum Jülich
Polyethylene is the material from which, among other things, light, strong and flexible plastic bags are manufactured. To prevent them tearing easily, the starting material ethene (ethylene) must not be contaminated with ethyne (acetylene). However, both compounds are manufactured from petroleum and are hard to separate. Therefore, in the manufacture of plastics, ethyne is processed into ethene with the help of palladium. In the future, this expensive catalyst can potentially be replaced by a compound of iron and aluminium. Scientists from Forschungszentrum Jülich, the Max Planck Institute for Chemical Physics of Solids in Dresden, the Fritz Haber Institute in Berlin, the LMU in Munich and the Budapest Centre for Energy Research have proposed this material as a substitute, as it hydrogenates ethyne to ethene just as efficiently as catalysts containing precious metals.
The key to this breakthrough lay in the use of a systematic approach; researchers used their knowledge of exactly how the reaction takes place on platinum, concluded from this the necessary characteristics of the catalyst, and then searched for a compatible material. It is well known that palladium only delivers the desired product when active centres that are as small as possible are present, approximately in the shape of single palladium atoms in an otherwise inactive matrix. Failing this, the reaction of the ethyne molecules does not stop at the point of semi-hydrogenation. In other words, they take up not two but four hydrogen atoms and become ethane, which is of no use in the chain reaction that produces polyethylene. This is how the idea came about, to “fix” the active centres, initially single palladium atoms in a crystal lattice made from gallium.
The next step consisted of finding alternative materials. Iron and aluminium proved to be suitable in the form of what is sometimes referred to as a complex intermetallic alloy. Unlike more conventional alloys, the metals involved do not blend together in a relatively random fashion, but form ordered crystal structures. In this way, it is possible for the individual catalytic centres made of iron atoms to be separated from each other by aluminium atoms. The materials tested were produced at the Peter Grünberg Institute in Jülich and at the LMU in Munich.
The iron-aluminium compound was found to be just as reliable a catalyst as the palladium-gallium compound. Before the new catalyst can be used by industry to lower the costs of polyethylene production, the material must stand the test of its large scale technological application. If successful, the catalyst could then demonstrate its strengths in selective hydrogenation, as well as in the manufacture of other types of plastics.
“What really counts is that we gain a better understanding of the physical processes which take place during catalysis,” explains Michael Feuerbacher of the Peter Grünberg Institute. “That helps us on the one hand in the further optimization of the iron-aluminium catalyst, and on the other in our search for other catalytic materials”. The scientists plan to continue their systematic search for catalysts that can be used in other reactions, especially in the area of alternative energy technologies. For this reason, they are investigating other complex intermetallic alloys, for example with regard to their suitability for the conversion of methane to hydrogen, a necessary process in cars fuelled by hydrogen.
Original publication
Other news from the department science
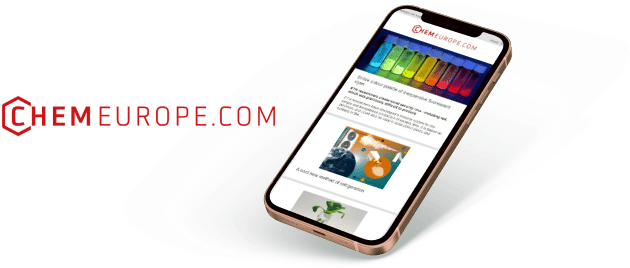
Get the chemical industry in your inbox
By submitting this form you agree that LUMITOS AG will send you the newsletter(s) selected above by email. Your data will not be passed on to third parties. Your data will be stored and processed in accordance with our data protection regulations. LUMITOS may contact you by email for the purpose of advertising or market and opinion surveys. You can revoke your consent at any time without giving reasons to LUMITOS AG, Ernst-Augustin-Str. 2, 12489 Berlin, Germany or by e-mail at revoke@lumitos.com with effect for the future. In addition, each email contains a link to unsubscribe from the corresponding newsletter.
Most read news
More news from our other portals
Last viewed contents
Günter_Wirths
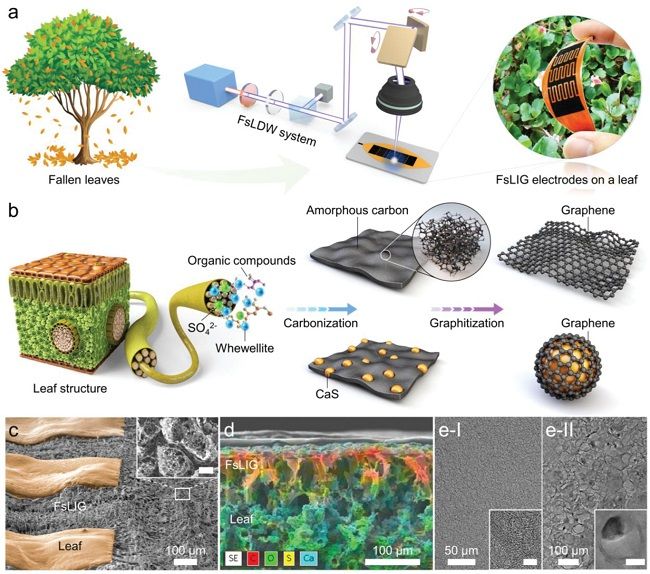
Eco-friendly micro-supercapacitors using fallen leaves - Femtosecond micro-supercapacitors on a single leaf could easily be applied to wearable electronics, smart houses, and IoTs
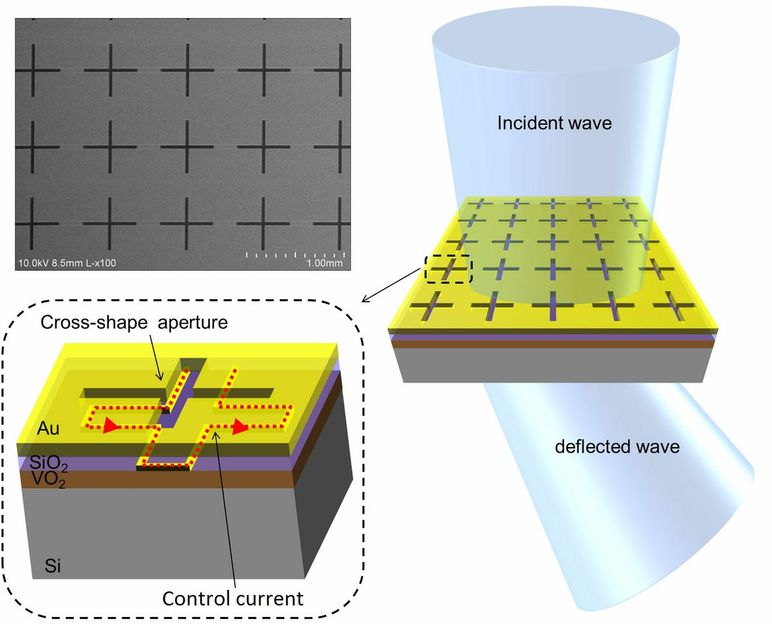
New metamaterial paves way for terahertz technologies
Early Screening, Innovative Solutions to Underline Importance of ADME/Tox Technologies in Successful Drug Development - Considerable Time, Cost Savings to Accrue from Advanced ADME/Tox Technologies
Wacker Boosts Supply for Surface Coating Resins
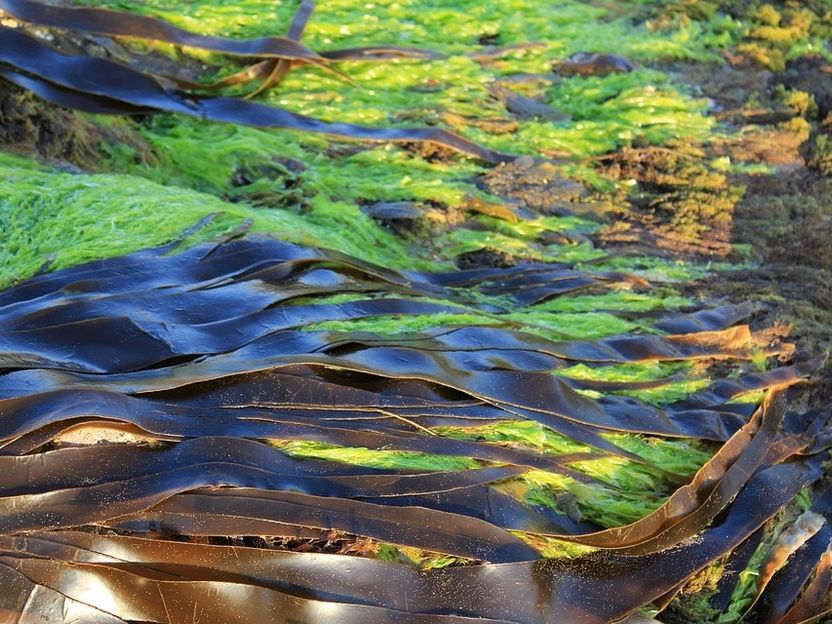
Fueling the future - Scientists promote new method of algal hydrogen production
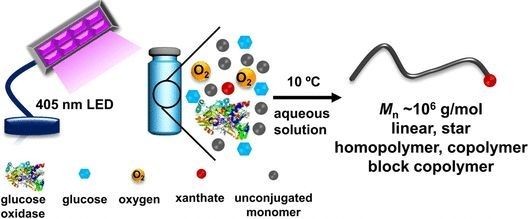
Ultraheavy precision polymers - Controlled photoenzymatic RAFT polymerization of nonconjugated polymers
New technique for detecting mold contamination in homes and other buildings
Gems_of_Sri_Lanka
Category:ADP_receptor_inhibitors
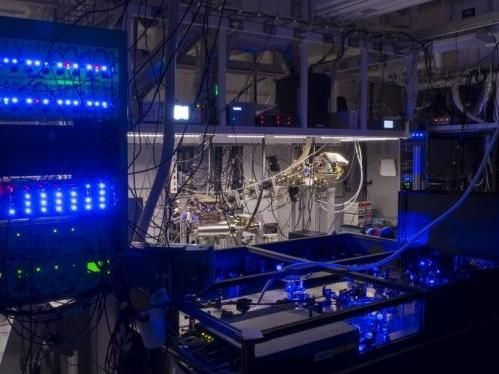