Bayer MaterialScience commissions new hydrogenation technical center
Pooling of research activities for the efficient production of MDI and TDI
Bayer MaterialScience has commissioned a new technical center for the development of isocyanate production processes at Chempark Dormagen. The research center was erected in just under a year with an investment of EUR 5 million.
“All global research activities related to the production of aromatic isocyanates have now been pooled in the new hydrogenation technical center,” said Dr. Joachim Wolff, head of the polyurethanes business and member of the Executive Committee of Bayer MaterialScience, on the occasion of the commissioning. “The associated efficiency gains in the research and optimization of the production processes will help to further expand our global technological leadership.”
The state-of-the-art facility is focused on hydrogenation technology for the production of precursors to diphenylmethane diisocyanate (MDI) and toluene diisocyanate (TDI). MDI is the starting product for rigid polyurethane foam, which enables particularly efficient insulation of buildings, in particular. Over its service life, it saves as much as 70 times more energy than is needed to produce the foam. TDI is used to make flexible polyurethane foam for comfortable upholstered furniture and mattresses.
MDI is based on benzene, which is first nitrated into nitrobenzene and then hydrogenated to produce aniline. An additional step then converts the aniline to diphenylmethane diamine, the direct precursor to MDI. A catalyst is used to produce aniline from nitrobenzene and hydrogen gas. With the conventional isothermic process, which is performed at a constant temperature, the substantial heat generated during the reaction must be dissipated using heat transfer oils. The reaction takes place inside a reactor block, in which many thousands of tubes containing the catalyst have been welded together. Finally, the aniline must be painstakingly purified of byproducts before it can be used further.
The adiabatic variant developed by Bayer MaterialScience is a current example of innovative process development in the area of hydrogenation. The technology eliminates the need for heat transfer and enables a substantial gain in efficiency. Here the reaction takes place in a large steel vessel, in which the catalyst is placed on a grating. The heat of reaction is dissipated together with the gas flow, eliminating the need for the circulating oil loop. In addition, the product is also of significantly higher purity. “The technology is already proving to be extremely successful in our world-scale facility in Shanghai, China, with an annual production capacity of 350,000 metric tons. The conventional process would have been too complex and too expensive for a facility of this size,” said Dr. Thorsten Dreier, who heads the isocyanate research department at polyurethane production.
The researchers plan to concentrate on the further optimization of both process variants at the new technical center. Other focal points will be researching and improving the hydrogenation of dinitrotoluene to obtain toluene diamine, the direct precursor to TDI, and also the Deacon process for the oxidation of hydrogen chloride.
Organizations
Other news from the department business & finance
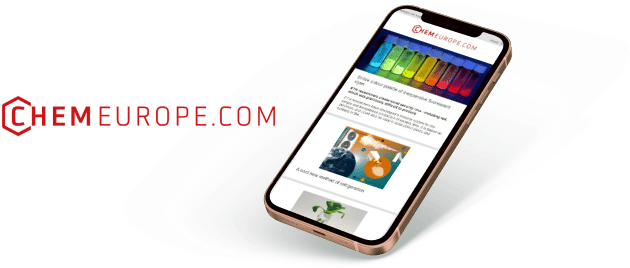
Get the chemical industry in your inbox
By submitting this form you agree that LUMITOS AG will send you the newsletter(s) selected above by email. Your data will not be passed on to third parties. Your data will be stored and processed in accordance with our data protection regulations. LUMITOS may contact you by email for the purpose of advertising or market and opinion surveys. You can revoke your consent at any time without giving reasons to LUMITOS AG, Ernst-Augustin-Str. 2, 12489 Berlin, Germany or by e-mail at revoke@lumitos.com with effect for the future. In addition, each email contains a link to unsubscribe from the corresponding newsletter.
Most read news
More news from our other portals
Last viewed contents
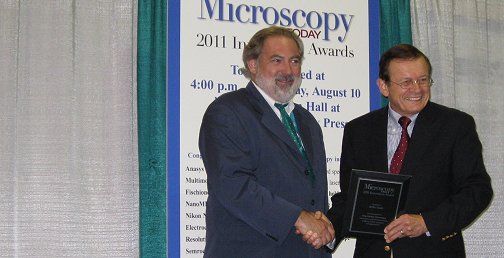
True Surface Microscopy wins Microscopy Today Innovation Award 2011 - Third Consecutive Award
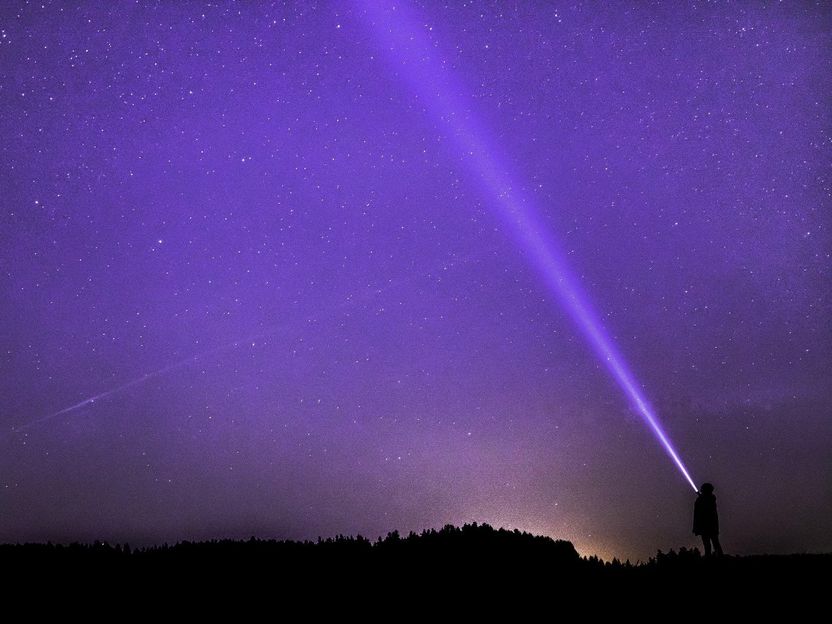
Solar cell keeps working long after sun sets - Harvesting energy from the temperature difference between photovoltaic cell, surrounding air leads to a viable, renewable source of electricity at night
New rapid technique detects food bacteria - CU researchers announce new technique for rapidly detecting illness-causing bacteria in food
Materia_medica
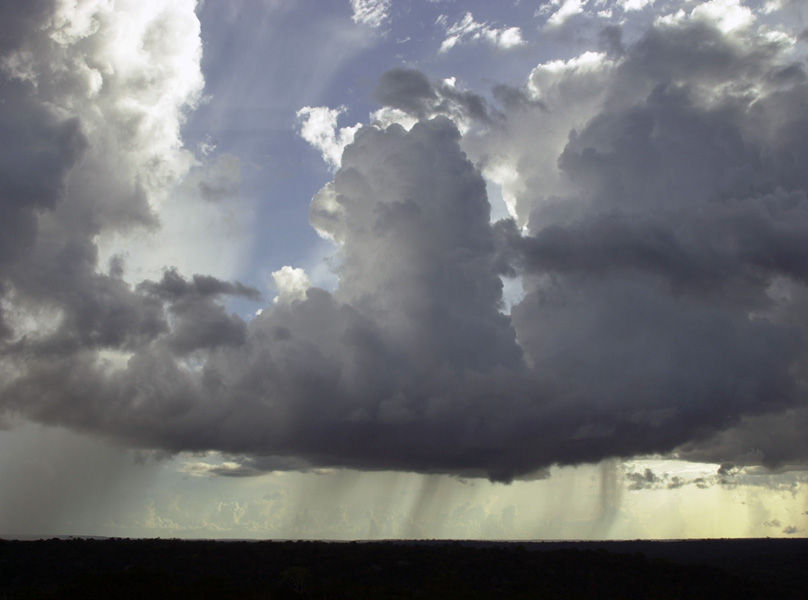
The Amazon rainforest -- a cloud factory
Transition metal catalyst prompts 'conjunctive' cross-coupling reaction
European_Gemological_Laboratory_(USA)
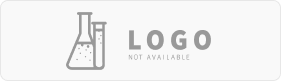