Fraunhofer ISE Demonstrates Ultrafine Transport Layers for Electrolyzers
proton exchange membranes (PEM) are one of the most promising technologies for the production of green hydrogen by electrolysis. To reduce the material and manufacturing costs for PEM electrolyzers, the Fraunhofer Institute for Solar Energy Systems ISE is researching scalable production processes. Now, for the first time, it has succeeded in producing ultra-fine porous transport layers made of titanium using a screen printing process, thereby reducing the cost of catalyst materials. Industry-standard, scalable equipment was used.
PEM electrolysis is a key technology for the market ramp-up of the green hydrogen economy because it can be operated at high power density and the flexible power supply from renewable energies. In addition to the catalyst-coated membrane, the porous transport layers (PTL) are central to its performance. “As the ‘lungs’ of the catalyst-coated membrane, the PTLs are responsible for transporting water and gases, among other things. Optimizing the PTL and its surface properties is a major lever for reducing costs and increasing performance in PEM electrolysis. This is why this layer is increasing-ly becoming the focus of our research,” explains project manager Stefan Bercher of Fraunhofer ISE.
To improve the surface properties, microporous titanium layers (MPL) are applied between the PTL layer and the catalyst-coated membrane. Thanks to their low surface roughness, they allow the use of catalyst layers with significantly reduced iridium loading, as they significantly improve catalyst contacting and thus utilization. They also facilitate the use of thinner membranes, which reduces ohmic losses. The goal of the Fraunhofer ISE project group was to match the titanium-based MPLs optimally to the catalyst layer to be contacted and to make them as fine as possible, since these metals are among the main cost factors in electrolyzers.
“At Fraunhofer ISE, we have decades of experience in manufacturing and characterizing components for PEM electrolysis. We are using this know-how in interface engineering to optimize both layers together, rather than separately as in the past,” explains Tom Smolinka, head of the Electrolysis and Hydrogen Infrastructure department at Fraunhofer ISE.
Successful proof of concept with screen printing process
To print the ultra-fine MPL structures, Fraunhofer ISE is using the screen printing process, with which the institute has many years of production experience in the field of photovoltaics. Since screen printing allows precise control of the thickness and structure of the layers, the project team sees great potential in this technology.
In a series of tests, the researchers investigated whether PTLs coated with microporous transport layers achieve better results than commercially available PTLs. The individual production steps and parameters of the printing process were optimized, from mixing the ink with titanium particles to the actual screen printing process on standard industrial equipment and sintering. During the subsequent characterization of the MPL layer printed on a coarse PTL, the surface roughness and performance were measured in particular. “We were able to print very fine layers about 20 µm thick and reduce the surface roughness by 46 percent. This improves the contacting of the catalyst layer, in which the load of the expensive precious metal iridium is continuously reduced,” says Stefan Bercher. This is the key to achieving the European targets for material savings and market launch despite limited resources. The research team is now looking for industrial partners to further optimize and adapt the microporous layer to customer-specific porous transport layers.
Other news from the department science
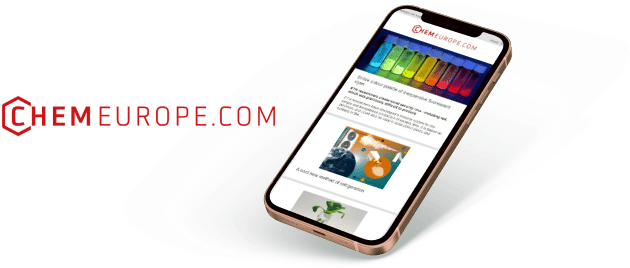
Get the chemical industry in your inbox
By submitting this form you agree that LUMITOS AG will send you the newsletter(s) selected above by email. Your data will not be passed on to third parties. Your data will be stored and processed in accordance with our data protection regulations. LUMITOS may contact you by email for the purpose of advertising or market and opinion surveys. You can revoke your consent at any time without giving reasons to LUMITOS AG, Ernst-Augustin-Str. 2, 12489 Berlin, Germany or by e-mail at revoke@lumitos.com with effect for the future. In addition, each email contains a link to unsubscribe from the corresponding newsletter.