Polyurethane with Shape Memory: From Foil to Foam
Isocyanate-free foaming increases occupational safety
Researchers at the Fraunhofer Institute for Applied Polymer Research IAP have developed a foil that changes into polyurethane foam (PU foam) when heated – entirely without health risks. The foil allows for isocyanate-free foaming, thus improving workplace safety. Additionally, it offers logistics advantages for storage and transportation. The material can be customized for various applications ranging from the automotive and construction industries to packaging.
"A frequently discussed aspect in the production of PU foam is the health risk at work from isocyanates, one of the main components in the chemical reaction that forms polyurethane," explains Dr. Thorsten Pretsch, head of the Synthesis and Polymer Technology research division at Fraunhofer IAP in the Potsdam Science Park. "Our foil enables isocyanate-free foaming. It minimizes health risks in the workplace and improves occupational safety, especially for on-site applications such as in the construction industry," emphasizes Dr. Pretsch.
Isocyanate-free foaming
Strict regulations and protective measures apply when handling isocyanates. They are toxic and have a sensitizing effect on the respiratory tract and skin; some isocyanates are suspected of causing cancer. The newly developed foil transforms into a PU foam simply by the application of heat, without undergoing any chemical reaction. The research team's innovative approach also represents a new technology for foam production itself: thermal foaming. The product is named FOIM – a combination of the words “foil” and “foam”.
Flexible: polyurethane foam with shape memory
The novel material is a shape memory polymer. It is capable of returning to its original shape after being deformed. An external stimulus such as heat triggers the shape memory effect. For the foil, the researchers synthesized a polyurethane foam and then compressed it. At a temperature of sixty degrees Celsius, the foil expands from 2.5 millimeters thick to a foam of 40 millimeters thickness – an expansion by a factor of 16. The result is a soft-elastic PU foam with a density of 80 kilograms per cubic meter. According to the DIN EN ISO 33861 standard, this is a low-density foam that is suitable for use as packaging material, among other things.
Space-saving: semi-finished products made of shape-memory foam
Industrial production often uses polyurethane foams as standardized, prefabricated intermediate product in cut form. These so-called semi-finished products are further processed or directly integrated into end products in the manufacturing process. They enable mass production while maintaining consistent quality. Their drawback: polyurethane foams take up a lot of volume. "Our foil saves space during transport and storage," emphasizes Dr. Pretsch. It is only when heated to sixty degrees Celsius that the foil foams up. "This benefits industries looking to reduce logistics costs and those where low transport volume is desirable, such as the aerospace industry," says the research scientist.
Versatile: insulating, backfilling, fixing with foil foam
Low-density PU foams are suitable for numerous fields of application and industries: furniture manufacturers use them for upholstery, in the packaging industry they protect fragile goods during transportation, in the construction industry PU foams backfill joints, and in vehicle interiors they are used for insulation or cladding. Application tests for filling hollow cavity structures with the new foil were successful. The material foamed almost completely when heated, even in complex geometric shapes. The foil is also suitable for use in bonding and joining technology. The researchers demonstrated that two objects can be fixed in place by foaming a cavity between them. The properties of the innovative material are variable: the research scientists can individually adjust the flexibility and transparency of the foil before foaming. The same applies to the density, thermal conductivity, elasticity and compression properties of the foam. "We adapt the properties of the material to the technical requirements of different applications. From car interiors to medical treatments and the protection of fragile goods," concludes Dr. Pretsch.
Original publication
Other news from the department science
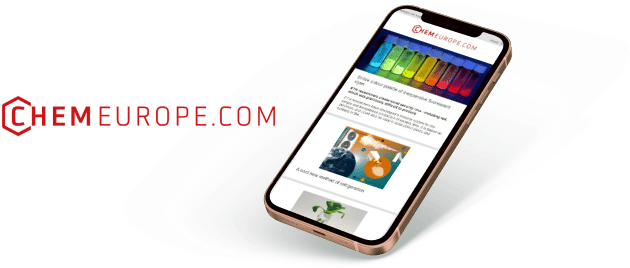
Get the chemical industry in your inbox
By submitting this form you agree that LUMITOS AG will send you the newsletter(s) selected above by email. Your data will not be passed on to third parties. Your data will be stored and processed in accordance with our data protection regulations. LUMITOS may contact you by email for the purpose of advertising or market and opinion surveys. You can revoke your consent at any time without giving reasons to LUMITOS AG, Ernst-Augustin-Str. 2, 12489 Berlin, Germany or by e-mail at revoke@lumitos.com with effect for the future. In addition, each email contains a link to unsubscribe from the corresponding newsletter.