Taking a cue from lightning, eco-friendly reactor converts air and water into ammonia
Without any carbon footprint
There’s a good chance you owe your existence to the Haber-Bosch process. This industrial chemical reaction between hydrogen and nitrogen produces ammonia, the key ingredient to synthetic fertilizers that supply much of the world’s food supply and enabled the population explosion of the last century. It may also threaten the existence of future generations. The process consumes about 2% of the world’s total energy supply, and the hydrogen required for the reaction mostly comes from fossil fuels.
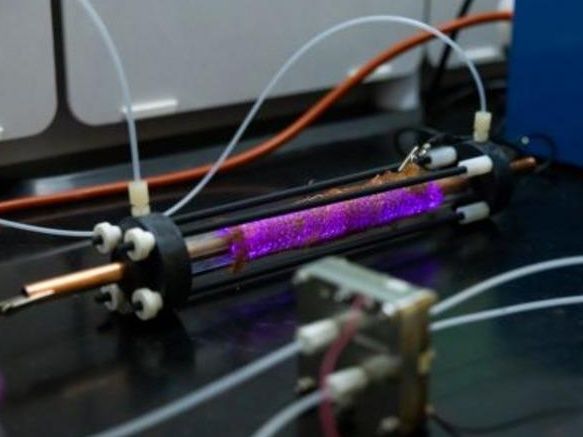
A plasma-electrochemical reactor developed by the team of Chris Li can convert nitrogren in the air into ammonia without a carbon footprint.
Douglas Levere/University at Buffalo
Taking inspiration from how nature —including lightning — produces ammonia, a team led by the University at Buffalo has developed a reactor that produces the chemical commodity from nitrogen in the air and water, without any carbon footprint.
This plasma-electrochemical reactor, described in a study published by theJournal of the American Chemical Society, can sustain a high ammonia production rate of approximately 1 gram per day for over 1,000 hours at room temperature, and does so directly from air.
The researchers say this is a significant advance toward green ammonia synthesis at an industrially competitive production rate and reaction stability.
“Ammonia is often considered the chemical that feeds the world, but we also have to face the realization that the Haber-Bosch process has not been modernized since its invention 100 years ago. It still uses a high-temperature, high-pressure processing, and generates a large carbon footprint, making it unsustainable for the long term,” says the study’s corresponding author, Chris Li, PhD, assistant professor of chemistry in the UB College of Arts and Sciences. “Our process only requires air and water, and can be powered by renewable electricity.”
Mimicking nature’s nitrogen cycle
Nature has its own way of producing fertilizer. In nitrogen fixation, the electrical energy of a lightning strike breaks up nitrogen molecules in the atmosphere to form different nitrogen oxide species. After falling down as rainwater, nitrogen oxides are converted into ammonia by bacteria in the soil, supplying plants with nutrients.
In the UB-led team’s two-step reactor, the role of lightning is replaced with plasma and the role of bacteria replaced by a catalyst of copper-palladium.
“Our plasma reactor converts humidified air into nitrogen oxide fragments, which are then placed in an electrochemical reactor that uses the copper-palladium catalyst to convert them into ammonia,” Li says.
Crucially, the catalyst is able to adsorb and stabilize the numerous nitrogen dioxide intermediates created by the plasma reactor. The team’s graph theory algorithm identified that most the nitrogen oxide compounds have to cycle through nitric oxide or amine as an intermediate step before becoming ammonia. This allowed the team to intelligently design a catalyst that binds favorably with those two compounds.
“When plasma energy or a lightning strike activates nitrogen, you generate a soup of nitrogen oxide compounds. To simultaneously convert, in our case, up to eight different chemical compounds into ammonia is incredibly difficult,” says Xiaoli Ge, the study’s first author and a postdoctoral researcher in Li’s lab. “Graph theory essentially allows us to map out all the different reaction paths and then identify a bottleneck chemical. We then optimize our electrochemical reactor to stabilize the bottleneck chemical, so that all the different intermediates will be selectively conferred into ammonia.”
Scaling up
Li’s team is currently in the process of scaling up their reactor and are exploring both a startup and partnerships with industry to help commercialize it. UB’s Technology Transfer Office has filed a patent application on the reactor and methods for its use.
Over half the world’s ammonia is produced by four countries — China, the United States, Russia and India — while many developing countries are unable to produce their own. While the Haber-Bosch process must be conducted on a large scale in a centralized power plant, Li says their system can be done at a much smaller scale.
“You can imagine our reactors in something like a medium-sized shipping container with solar panels on the roof. This can then be placed anywhere in the world and generate ammonia on demand for that region,” he says. “That's a very exciting advantage of our system, and it will allow us to produce ammonia for underdeveloped region with limited access to the Haber-Bosch process.”
Original publication
Xiaoli Ge, Chengyi Zhang, Mayuresh Janpandit, Shwetha Prakash, Pratahdeep Gogoi, Daoyang Zhang, Timothy R. Cook, Geoffrey I.N. Waterhouse, Longwei Yin, Ziyun Wang, Yuguang C. Li; "Controlling the Reaction Pathways of Mixed NOxHy Reactants in Plasma-Electrochemical Ammonia Synthesis"; Journal of the American Chemical Society, 2024-12-12
These products might interest you
See the theme worlds for related content
Topic world Synthesis
Chemical synthesis is at the heart of modern chemistry and enables the targeted production of molecules with specific properties. By combining starting materials in defined reaction conditions, chemists can create a wide range of compounds, from simple molecules to complex active ingredients.
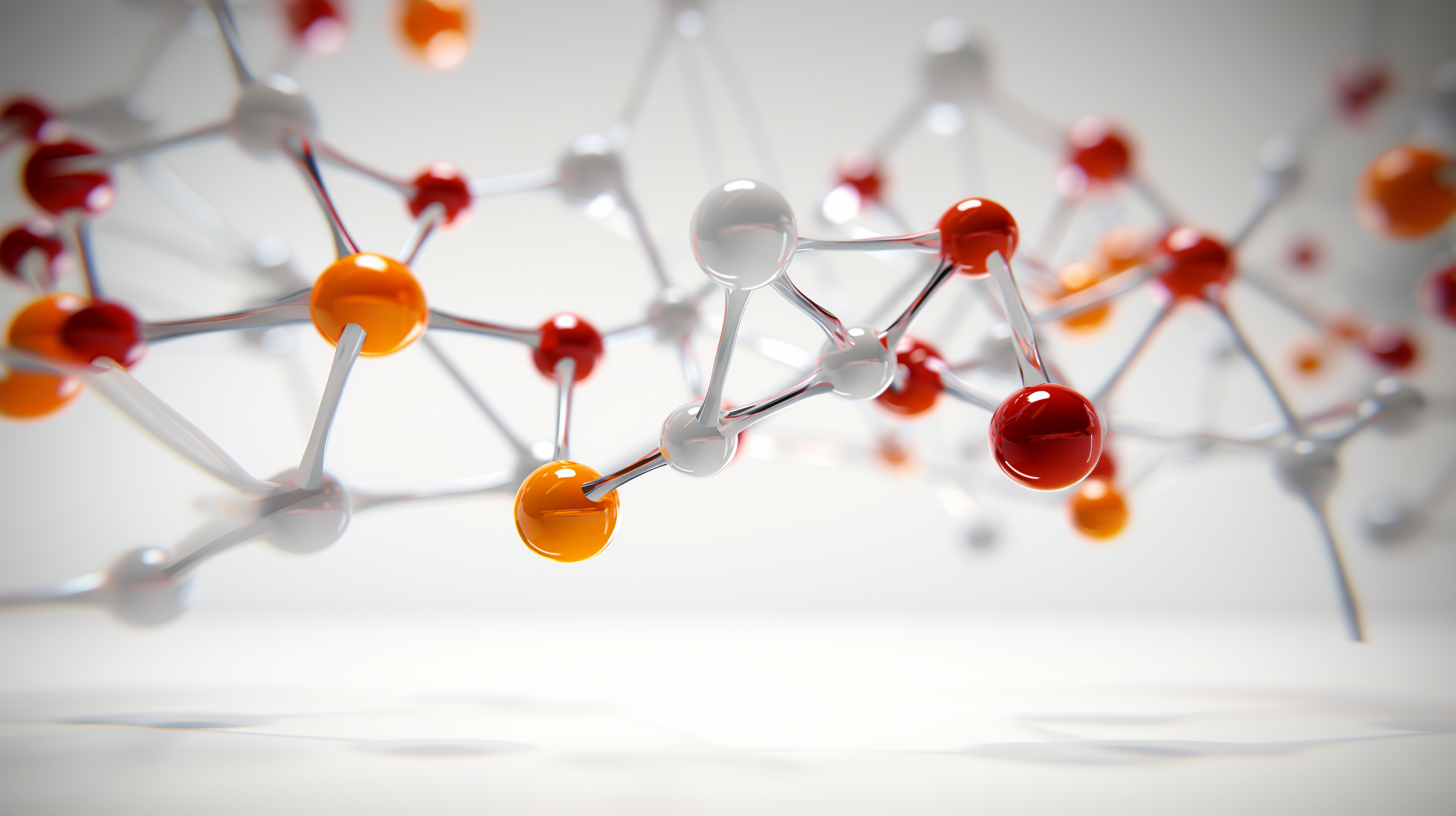
Topic world Synthesis
Chemical synthesis is at the heart of modern chemistry and enables the targeted production of molecules with specific properties. By combining starting materials in defined reaction conditions, chemists can create a wide range of compounds, from simple molecules to complex active ingredients.