Fresh iron from old mining sludge
Great interest in pilot plant
It sounds like utopia: mining sludge is transformed into valuable metals and new building materials. Over the past three years, researchers at TU Bergakademie Freiberg have successfully trialled this innovative process in a pilot plant. The team succeeded in extracting iron and zinc from mining sludge and wastewater and processing the residues into a building material based on geopolymer technology. In the end, they release clean water into the original watercourse. The chemists proved that the innovative process works at the so-called Roter Graben near Freiberg - they want to further develop the process with regional partners in the future. However, the recycling technology could also provide solutions for post-mining in other regions.
In the former mining area, ferrous water and more than 13,000 cubic metres of sludge from the Freiberg mining district seep into an artificial stream, the "Roter Graben". What is considered a contaminated site and has to be dredged and disposed of at great expense is pumped through a filter press and dewatered in the new process. "Several membranes filter out the solid components and remove any heavy metals in a further step," explains Professor Martin Bertau from the Institute of Technical Chemistry at TU Bergakademie Freiberg. The result is clean water and a residual sludge.
From these residues, Bertau's team extracts the valuable metals iron and zinc. The researchers are using an established process to ensure that the entire process can be operated economically. "The material can be used in a smelting plant that produces iron and zinc from it," explains project team member Dr Michael Kraft. "In Freiberg, for example, this would be Befesa GmbH." The pollutants arsenic, lead and cadmium collect in the electrostatic precipitator and are thus permanently removed from the environment and disposed of properly. This not only recovers the valuable materials in the sludge, but also solves a real environmental problem. The chemists even recycle the remaining mineral residue. "We can turn it into so-called geopolymer building materials by mixing it with fired clay and caustic soda, which is known at home as drain-free," explains Dr Michael Kraft.
Climate-friendly cement alternative
Geopolymers are binding agents that are modelled on natural minerals in their composition. They have properties that equal or even surpass cement. For example, the mine sludge can be used to produce stable bricks that can be recycled indefinitely. The researchers have applied for a patent for their process. With regard to the EU Water Framework Directive, which requires the treatment of mining water, a significant contribution can be made at an early stage to fulfil official requirements and relieve nature of pollutants. "The technology for using mine sludge not only saves landfill space," says Professor Martin Bertau. "Around eight per cent of global CO2 emissions are attributable to cement. With geopolymers, they can be reduced by 80 per cent - that's a real contribution to the climate!" summarises Dr Michael Kraft.
Great interest in pilot plant
Several locations have already expressed interest in the test containers. "The test facility will be cleaned over the winter and then moved to a new location in the spring," the chemists reveal. This is because the Freiberg technology will be presented in the German Pavilion at the World Expo 2025 in Osaka next year.
Most read news
Topics
Organizations
Other news from the department science
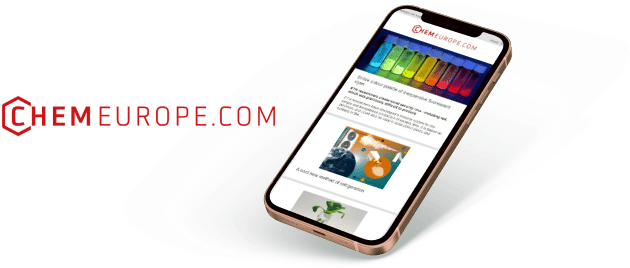
Get the chemical industry in your inbox
By submitting this form you agree that LUMITOS AG will send you the newsletter(s) selected above by email. Your data will not be passed on to third parties. Your data will be stored and processed in accordance with our data protection regulations. LUMITOS may contact you by email for the purpose of advertising or market and opinion surveys. You can revoke your consent at any time without giving reasons to LUMITOS AG, Ernst-Augustin-Str. 2, 12489 Berlin, Germany or by e-mail at revoke@lumitos.com with effect for the future. In addition, each email contains a link to unsubscribe from the corresponding newsletter.