Packaging industry: Plasma-coated paper as a plastic substitute
Environmentally harmful plastic waste has increased continuously in Germany in recent years. Packaging generates a particularly large amount of waste. Coatings for paper packaging based on plant-based ingredients could provide a sustainable replacement in the future. In the BioPlas4Paper project, researchers at the Fraunhofer Institute for Surface Engineering and Thin Films IST and their partners used a coating process known as plasma polymerization to create water-repellent barrier layers on paper based on plant substances, thereby improving the material's resistance to weathering.
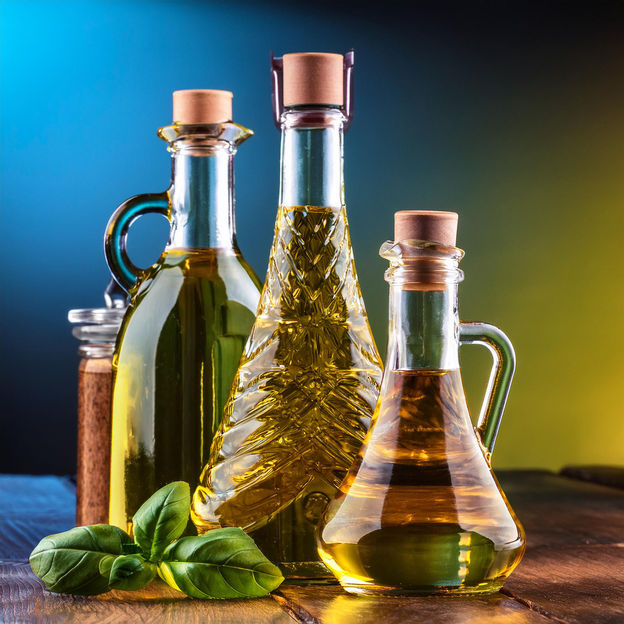
Researchers at the Fraunhofer IST use vegetable oils to make paper water-repellent
© Fraunhofer IST using Adobe Firefly
Plastic packaging continues to be a major problem for the environment. Paper, on the other hand, is made from renewable raw materials and has the advantage over petroleum-based plastic that it decomposes and does not remain in the soil for many years. However, uncoated paper does not form a barrier against moisture or oxygen. It is temperature-sensitive, reacts sensitively to moisture and bacteria and is characterized by uneven surfaces. In order to fully exploit the potential of the material, improve recycling options, replace plastic packaging and open up new fields of application, the durability, resistance and quality of paper products must be improved. Researchers at the Fraunhofer IST are working on this task in close cooperation with the Technical University of Darmstadt and the Thünen Institute of Wood Research in the BioPlas4Paper project. In order to produce homogeneous, moisture-repellent layers on paper, the project partners are relying on plant substances such as oregano or chia oil as well as extractives obtained from bark material. These plant substances are characterized by their antibacterial effect, among other things.
Bio-based plasma polymers cross-link with the paper surface
"We use previously unused plant substances with a high proportion of unsaturated fatty acids to make paper hydrophobic, i.e. water-repellent. To do this, we use atmospheric pressure plasma technology, in which gas is excited by means of high voltage under ambient pressure in such a way that a plasma, i.e. a mixture of particles consisting of ions, free electrons and usually also neutral atoms or molecules, ignites. A discharge occurs between the electrodes," says Martin Bellmann, a scientist at the Fraunhofer IST in Braunschweig. The plant substances are converted into an aerosol by the addition of nitrogen and introduced into the plasma as vaporous organic precursor compounds in order to form polymer networks. Experts refer to this process, in which the precursor compounds are activated by a plasma, as plasma polymerization. The micrometre-sized particles bond with each other to form plasma polymers, but the tiny droplets also crosslink with the paper and lie flat on the rough paper substrate, penetrating deep into the pores and fibres of the surface. "Only when the plasma is used do the plant molecules become reactive and crosslink to form polymers," explains the researcher.
Innovative plasma source concept
The plasma is generated using a plasma source by ionizing gas between two rotationally symmetrical electrodes to which high voltage is applied. The geometric arrangement of the electrodes and the way in which the aerosol is introduced and the plasma is ignited are new. The combination of these measures results in an innovative concept, which the researchers developed specifically for the project, so that the effects of the ambient air are reduced to a minimum under atmospheric pressure, even at higher coating speeds, and the results are consistent and reproducible. "Due to the roughness of the paper surface, the ambient air is swirled at high processing speeds, which changes the plasma properties. We can avoid these harmful influences with our concept," says Bellmann. The plasma source is brought close to the paper surface and thus completely displaces the ambient air. The researchers work with plasma temperatures of around 70 degrees in order to avoid damaging the paper itself, the bio-based precursor molecules and the properties of the plasma polymers produced.
Water-repellent layers through olive oil
In numerous tests with a wide range of vegetable oils and extracts, the researchers were able to prove that biobased substances can be reproducibly and homogeneously deposited or separated using plasma. Very good hydrophobic layers could be achieved with olive and chia oil, for example. Depending on the precursor compounds used and the coating parameters, the researchers can influence and optimize the layers. The aim is to equip paper as a material for increasingly demanding usage scenarios and thus replace plastic materials in the future. "One application example is moving boxes, which can be exposed to rain for longer periods without softening thanks to our hydrophobic coatings. "Our aim is to reduce dependence on fossil resources and support the transition to a resource-efficient economy," says Bellmann.
Note: This article has been translated using a computer system without human intervention. LUMITOS offers these automatic translations to present a wider range of current news. Since this article has been translated with automatic translation, it is possible that it contains errors in vocabulary, syntax or grammar. The original article in German can be found here.